It is not only in lightweight automotive construction or aerospace technology that aluminium is a byword for dynamism and pushing the boundaries of accepted engineering limits. It also facilitates everyday life wherever large structures have to be moved by human hands, such as the diverse range of access solutions offered by ALTEC Aluminium-Technik GmbH & Co. KGaA.
The medium-sized enterprise from Mayen in the western German state of Rhineland-Palatinate has an extremely broad product portfolio: from rolling scaffolds, facade scaffolds and flat roof fall-protection systems to complete docking systems for the aviation industry and numerous special solutions. These include mobile maintenance stairs, working platforms, transitions or platform stairs for industrial applications.
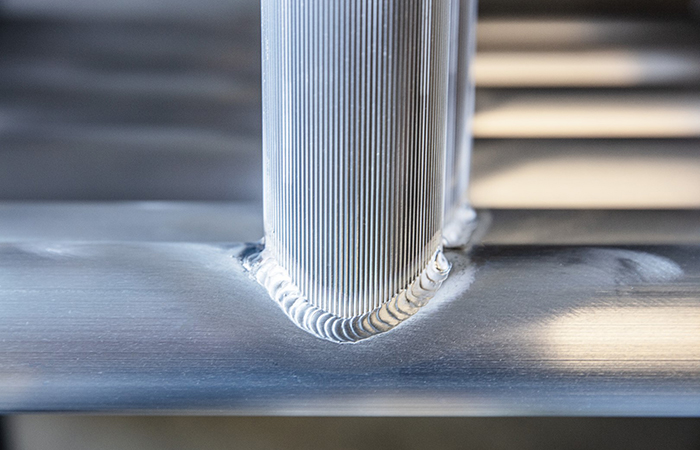
Certified welding company with the latest technology
Up to 95 percent of the metal processed and welded on ALTEC’s production lines is aluminium. Steel applications account for just five percent. Yet as a specialist welding company with EN 1090-1 and 1090-3 certification, ALTEC and its 50 employees can master even the most complex orders thanks to 35 years of experience in welding aluminium components.
In order to be able to meet its customers’ demands, ALTEC has always relied on pioneering process and manufacturing technology, despite its relatively modest size. “This includes state-of-the-art CAD workstations as well as fully automated robotic welding cells and the associated high-tech welding process technology,” explains Siegfried Berenz, a certified master metalworker and international welding specialist (IWS). Having spent the past 15 years being primarily active in the fields of aluminium welding and processing, he took over as plant manager of ALTEC in 2019.

Fronius welding technology moves in at ALTEC
As part of an ongoing automation process, a specific aluminium framework part (AlSi1, two millimetres) that has since become required in large quantities was to be transferred from manual production to robotic welding. One of the main goals here was to achieve a high welding speed in order to gain a competitive advantage. At the same time, the structure was to be joined with the greatest possible process reliability.
As a specialist in thin sheet and aluminium applications, Fronius therefore had the opportunity to beat the competition in 2018 as ALTEC found the best possible solution for its needs with the Fronius CMT (Cold Metal Transfer) process. When deployed in combination with the high-tech TPS 320i welding system platform, CMT delivers particularly high welding speeds, especially in the thin sheet range. As a result, Fronius succeeded in establishing itself in ALTEC’s production operations.
After 25 years of automated production, however, other areas of ALTEC’s robotic welding technology were also becoming long in the tooth. Plant manager Berenz therefore made it his mission to ensure the company’s production environment was equipped to guarantee long-term competitiveness. Following the positive experiences gained with the CMT process, the welding expert once again turned to the German sales and service team at Fronius Kaiserslautern.
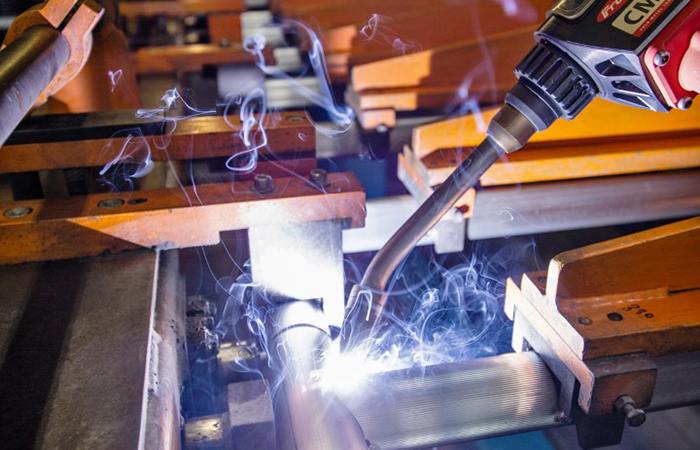
Further manufacturing challenges for ALTEC
In the case of the scaffolding system concerned, the outdated welding technology from a third-party supplier was now causing up to 70 percent rework due to a steady increase in weld seam defects. Time, material and labour costs were therefore no longer in proportion, and the advantages of robotic welding were being completely cancelled out. In addition, the weld seam appearance no longer came close to satisfying ALTEC’s strict demands. However, the production volume of the component was not high enough to justify investing in a modern robot system.
ALTEC’s requirements were therefore clear – a new system would first have to be compatible with the old robot technology. In addition, the greatest possible process reliability had to be ensured, which would reduce downtimes to almost zero. If possible the system should also be capable of welding in a single action in order to reduce processing times; it was this target that represented the greatest challenge. Due to the round style and the semi-circular fabrication of the rung, the unmanipulated welding operation would have to produce a vertical-up, flat and vertical-down seam in a single action. One process for all positional welds was thus a basic requirement.
At the same time, there was a gap of two millimetres in the flat-seam section due to the pre-processing. Particularly high gap-bridging ability therefore also had to be ensured in the future process technology. In order to be able to clearly distinguish itself from the competition in the production of scaffold and framework structures, the future welding process also had to deliver the best possible weld seam appearance. And on this basis ALTEC started its search for alternative modernization options.
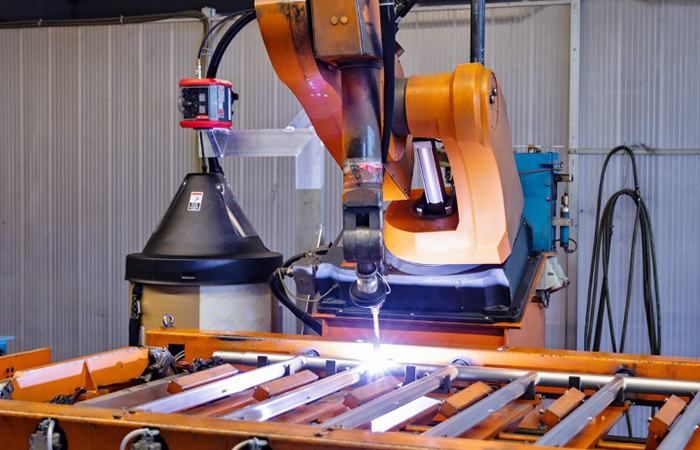
Conversion to PMC Rippledrive
Extensive welding tests conducted at the Fronius Germany competence centre for application engineering in Neuhof-Dorfborn near Fulda ultimately led to a successful conclusion. The PMC Rippledrive welding process variant, a special characteristic used for pulse welding, represented the most suitable solution for ALTEC’s welding challenges.
Rippledrive works in a way that is as ingenious as it is simple. Between a number of pulses defined by the welder, defined pause times are set in which the arc is completely switched off. This gives the weld pool time to cool down, making welding possible in all positions. The necessary gap-bridging ability of two millimetres is also guaranteed without any problems. In terms of appearance, the Rippledrive function also leaves a rippling pattern that is in no way inferior to the elegance of TIG welding.
The Pulse Multi Control (PMC) functions also allow the number, shape and size of the individual welding spots to be set by precisely defining the pulse currents. The TIG-like seam pattern can thus also be varied in its final execution.
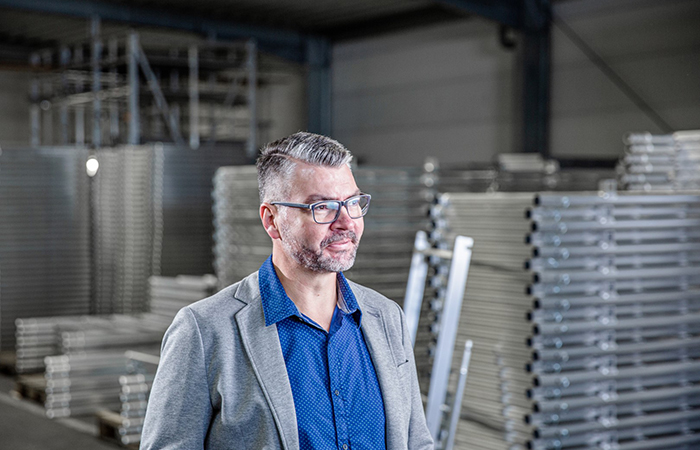
TPSi compatible with all robot systems
However, ALTEC also had to deal with the problem of connecting the welding technology to the robot. The task now was to mate the newly acquired TPS 320i digital high-tech welding system platform and the Fronius Robacta-Drive push-pull welding torch needed for the Rippledrive solution with the veteran but fully operational robot technology. ALTEC decided to take this step not least because of the wide range of fieldbus protocols (modern interfaces) available from Fronius, as well as the option of connecting the TPSi using conventional digital or analogue interface technology.
This results in the extraordinary advantage that the TPSi is truly compatible with almost every robot. Furthermore, the high-tech power source is equipped with numerous standardised hardware and software interfaces for various robot manufacturers right from the start. This reduces the installation time required to integrate the power source into the robot system to a minimum.
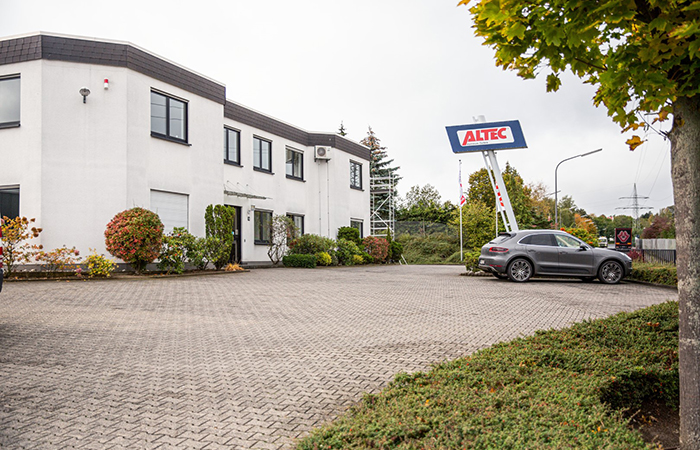
Impressive service and technical expertise from Fronius
ALTEC plant manager Siegfried Berenz is thoroughly impressed with the welding results and the service: “The expert advice from the Fronius application engineers and our experience to date with the new Rippledrive welding process have absolutely convinced us of the worth of the Fronius system. It has enabled us to reduce welding times by around 20 percent.”
One of the reasons for this is that the welding robot now no longer has to travel from the centre of the weld seam in both directions. “By using Rippledrive, it became possible for the first time at ALTEC for the robot to weld from left to right – through all the challenging vertical-up and vertical-down positions – in a single action. At the same time, weld seam defects have become an absolute exception, which means that the rework that was previously necessary is now almost zero,” continues Berenz. The highly precise wire guidance is also responsible for this: from the wire drum to the contact tip, all the components of the welding system involved are perfectly matched to each other. Only in this way can the particularly soft AlSi 5 wire be conveyed with the necessary precision over the required seven (!) metres.
Reduction of downtimes by almost 100 percent
“This fact, as well as the modernization of the plant itself, has reduced downtimes to a minimum. As a result, downtimes hardly ever occur any more. The high process stability of the Fronius welding system that has made this possible has therefore completely convinced us,” assures the plant manager.
“Should system failures nevertheless occur, the Fronius technicians are on site in no time at all thanks to the dense support network, which in our case is fulfilled by the Fronius Kaiserslautern sales and service team. Maintenance and servicing work is conducted reliably and highly professionally.”
High-quality process technology for high-quality parts
“The visual appearance of the welded parts has also improved significantly, making post-weld cleaning almost superfluous,” adds a visibly delighted Siegfried Berenz. However, in his eyes, the almost perfect Rippledrive TIG weld seam appearance is not only a bonus, but also an important prerequisite for underlining the high quality of ALTEC products.
Fronius and ALTEC have thus been able to develop a particularly trusting and mutually valuable relationship.
Emergency law passed to protect UK steelmaking
<b>(:-))</b> Gareth Stace as director general of trade body UK Steel, is obviously an expert on blast furnace technology & operation. Gareth...