Working with biocompatible hydrogels, Biomedical Engineering Professor Sam Sia at Columbia Engineering has invented a new technique that is said to stack the soft material in layers to make devices that have three-dimensional, freely moving parts.
The study - titled “Additive manufacturing of hydrogel-based materials for next-generation implantable medical devices,”, published online in Science Robotics is said to demonstrate a fast manufacturing method Sia has dubbed “implantable microelectromechanical systems” (iMEMS).
By exploiting the unique mechanical properties of hydrogels, the researchers developed a locking mechanism for precise actuation and movement of freely moving parts, which can function as valves, manifolds, rotors, pumps, and drug delivery systems.
They were able to tune the biomaterials within a wide range of mechanical and diffusive properties and to control them after implantation without a sustained power supply, such as a battery. They then tested the payload delivery in a bone cancer model and found that the triggering of releases of doxorubicin from the device over 10 days showed high treatment efficacy and low toxicity, at 1/10th of the standard systemic chemotherapy dose.
“Overall, our iMEMS platform enables development of biocompatible implantable microdevices with a wide range of intricate moving components that can be wirelessly controlled on demand and solves issues of device powering and biocompatibility,” said Sia. “We’re really excited about this because we’ve been able to connect the world of biomaterials with that of complex, elaborate medical devices. Our platform has a large number of potential applications, including… drug delivery.”
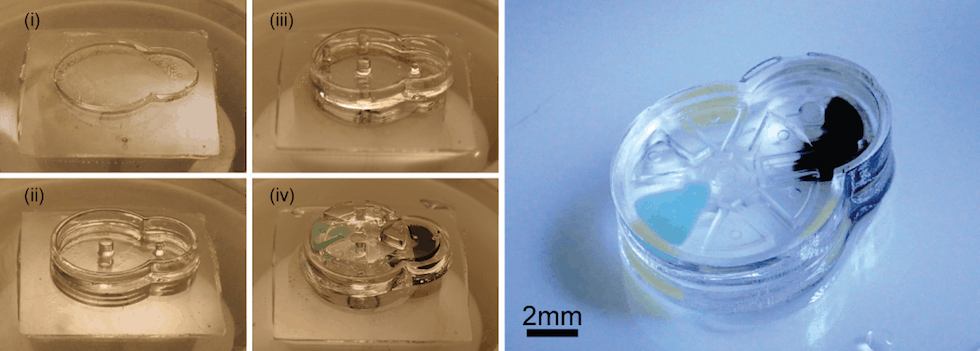
According to Columbia, most current implantable microdevices have static components rather than moving parts and, because they require batteries or other toxic electronics, have limited biocompatibility. Sia’s team spent over eight years solving this problem.
"Hydrogels are difficult to work with, as they are soft and not compatible with traditional machining techniques,” said Sau Yin Chin, lead author of the study. “We have tuned the mechanical properties and carefully matched the stiffness of structures that come in contact with each other within the device.
“Gears that interlock have to be stiff in order to allow for force transmission and to withstand repeated actuation. Conversely, structures that form locking mechanisms have to be soft and flexible to allow for the gears to slip by them during actuation, while at the same time they have to be stiff enough to hold the gears in place when the device is not actuated. We also studied the diffusive properties of the hydrogels to ensure that the loaded drugs do not easily diffuse through the hydrogel layers."
The team used light to polymerize sheets of gel and incorporated a stepper mechanisation to control the z-axis and pattern the sheets layer by layer, giving them three-dimensionality. Controlling the z-axis enabled the researchers to create composite structures within one layer of the hydrogel while managing the thickness of each layer throughout the fabrication process. They were able to stack multiple layers that are precisely aligned and, because they could polymerize a layer at a time, the complex structure was built in under 30 minutes.
IET sounds warning on AI doll trend
I agree that we need to reduce cooling water demand for servers. And yes, generative AI consumes a large amount. But what about BitCoins? Their...