In the intricate tapestry of the UK's workforce, a noticeable gap is emerging—one that poses a significant challenge for the future of manufacturing. The shortage of skilled welders has become a pressing concern, casting a shadow on the robust machinery and manufacturing sectors that rely heavily on this specialised skill set.
Welding, often overlooked but indispensable, forms the backbone of various industries. As the demand for precision engineering and metal fabrication rises, so does the need for adept welders. Unfortunately, the UK is experiencing a shortage that threatens to impede progress in the manufacturing realm.
Covid and Brexit have exacerbated a national skills shortage in the construction industry. The most recent Construction Skills Network (CSN) report forecasts that the construction industry may need an additional 225,000 workers by 2027. With many existing welders expected to retire by 2027, attracting new welding talent will be a critical part of the mix and central to filling the 36,000 new jobs that are expected.
In fact, the ageing workforce is a significant factor contributing to this shortfall. Skilled welders, often veterans in their field, are retiring without a sufficient influx of new talent to fill their shoes. The nature of welding demands a blend of theoretical knowledge and hands-on experience, making it a craft that requires time to master. The shortage is exacerbated by a lack of comprehensive training programs and educational pathways that can channel aspiring individuals into the welding profession.
This scarcity has tangible consequences for the manufacturing landscape. Projects face delays, and businesses grapple with increased labour costs as they compete for the limited pool of skilled welders. Moreover, the lack of welding expertise can compromise the quality of finished products, affecting the overall competitiveness of UK manufacturing on the global stage.
To tackle this challenge, collaboration is key - between educational institutions, industry stakeholders, and the government. Investing in comprehensive training programs, apprenticeships, and retraining initiatives can cultivate a new generation of skilled welders, fortifying the foundation of the manufacturing sector.
One such organisation driving progress is WorldSkills UK, an independent charity and member of WorldSkills, a global movement of over 80 countries supporting young people via competition-based training and assessments. WorldSkills UK, backed by education, industry and UK governments, is focussed on raising standards, championing future skills and empowering young people from all backgrounds. Its annual programme of national competitions plays a vital role in enabling students and apprentices to achieve excellence in their chosen career by testing their personal, technical and employability skills in competitive timed conditions. The 2023 WorldSkills UK National Competitions, comprising 51 skills including welding took place at colleges, independent training providers and universities across Greater Manchester and the winners were announced on 17 November.
The welding competition sponsored by leading global industrial gas company, Air Products, aimed at trainee/apprentice welders working and/or training in the welding industry at level 2-3 or higher level. The ten national finalists’ test pieces were marked to a set criterion based on BS EN ISO 5817.

The gold medal winner of the Welding Competition was Harry Pullen of Luminate Education Group.
Alison Smith, Marketing Manager UKI of Air Products commented “On behalf of Air Products, we offer our congratulations to Harry and all finalists on their achievements. We are proud that our partnership with WorldSkills UK allows us to play an active role in encouraging the next generation. Welding plays a critical role across UK industry and particularly in the energy transition”.
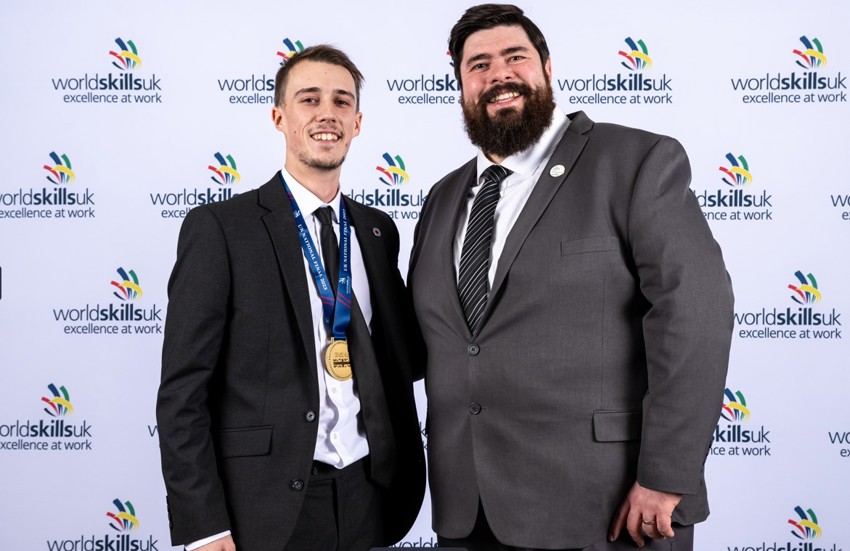
The welding skills shortage in the UK is not merely a hiccup; it's a critical juncture that demands attention and strategic intervention. Tackling the skills gap is not only the responsibility of educational institutions, industry stakeholders and the government, but also that of employers. Get this right, and the UK can safeguard its manufacturing future and ensure that the sparks of innovation continue to fly in its industrial landscape.
Follow the links for more information on Air Products and WorldSkills
Guest blog: exploring opportunities for hydrogen combustion engines
"We wouldn't need to pillage the environment for the rare metals for batteries, magnets, or catalisers". Batteries don't use rare...