Nuclear fusion occurs naturally in the core of the sun, releasing enormous amounts of radiant energy as mass is lost when hydrogen nuclei fuse together to form larger helium atoms. We observe this energy here on Earth as sunlight, despite being on average nearly 93 million miles away.
Demonstrating the feasibility of hydrogen fusion as a clean, safe and practically limitless source of energy has been the primary objective of over 50 years of international research efforts. At MIT the concept of a very high magnetic field approach to fusion has been the primary focus of research. At the MIT Plasma Science and Fusion Center (PSFC), experiment, leading-edge theory and numerical simulation are combined to identify and understand the science and technology that can make fusion energy available sooner.
The Advanced Divertor eXperiment (ADX) is a nuclear fusion experiment, and more specifically a tokamak, proposed by researchers at the PSFC to provide heat fluxes, densities and temperatures similar to what we expect to have in a fusion reactor, though with only short plasma discharges (see Figure 1).
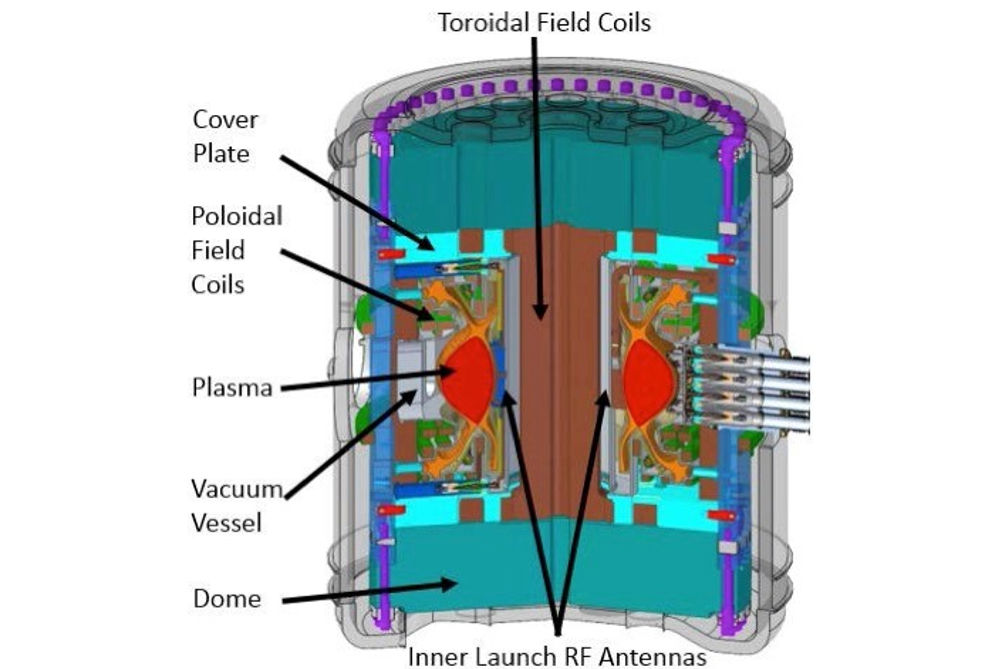
In a tokamak, temperatures in excess of 150 million degrees Celsius cause electrons to separate from nuclei, forming a fully-ionised superheated plasma from gaseous hydrogen fuel. The core plasma is contained within a toroidal or doughnut-shaped vacuum vessel and maintained at high pressure to produce a dense plasma with high likelihood of collision. External magnetic fields confine and control the plasma in a manner analogous to the intense gravitational fields at the sun’s core, thus producing nuclear fusion.
“Recent advances in high temperature superconductors could allow us to design a tokamak operating at higher magnetic fields, increasing the performance of the plasma to reactor levels,” explains Jeffrey Doody, a mechanical engineer at PSFC. “The research focus then switches from improving the performance of the plasma to the support systems in the tokamak.”
Using numerical simulation, Doody and his colleagues are designing the ADX structure to sustain reactor-level heat fluxes and magnetic fields, making it a suitable testbed for power exhaust systems and plasma-material interactions to support the development of next-stage fusion machines.
Surviving plasma distributions
The proposed design for the ADX vacuum vessel is innovative in that it is comprised of five separate axisymmetric shells, as shown in Figure 2, instead of a single cylinder. The modular design makes it possible to swap out magnetic coils and test different divertor configurations, where the divertor is a component that serves as the power exhaust system for removing fusion ashes from a tokamak. When ions escape confinement by the magnetic fields that control the plasma, the divertor collects and guides them out of the vessel.
The modular vessel must not only withstand the high heat fluxes and magnetic fields needed to produce nuclear fusion, but also survive plasma disruptions, which are another source of stress in the vacuum vessel shell generated when the plasma collapses.

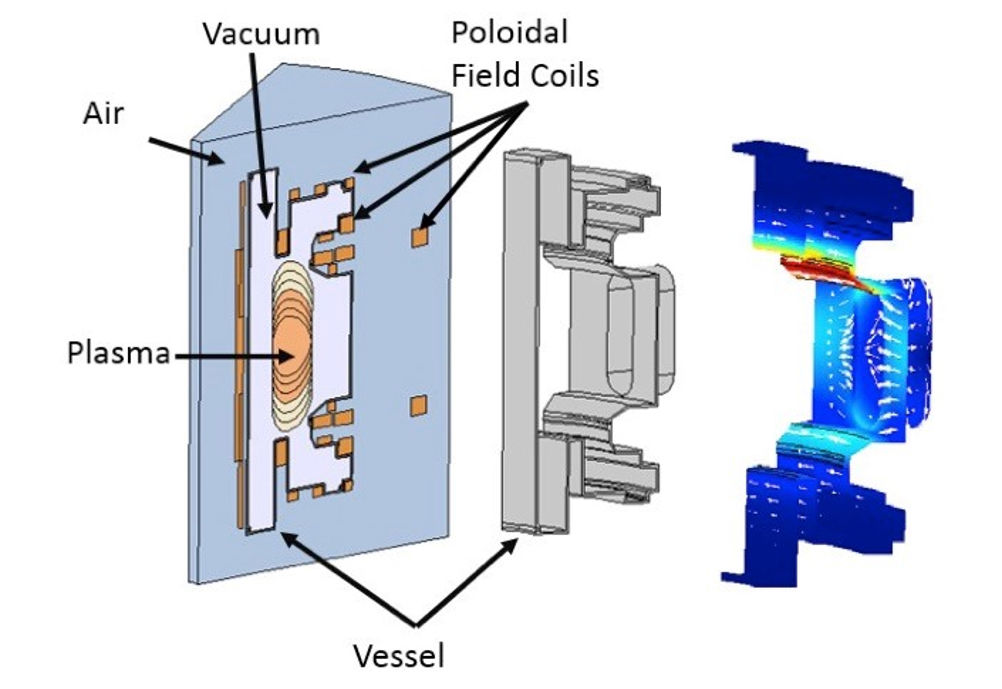
“To evaluate the proposed ADX vessel design, we perform numerical simulation in COMSOL Multiphysics® software to predict the magnetic fields, eddy currents and Lorentz forces resulting from a plasma disruption,” explains Doody. “The calculated loads are then applied to a separate structural model of the vessel in order to predict stress and displacement.” Figure 3 shows the geometry for a cyclic symmetry magnetic model of the ADX, including the vessel, plasma and poloidal magnetic coils, which are needed to hold the plasma in its equilibrium position.
A worst-case scenario exists for plasma disruptions in vertical displacement events (VDE), where the plasma drifts upward carrying 1.5 million amperes of current, stops moving after 10 milliseconds and loses all of its current in a single millisecond. Rapidly changing magnetic fields surrounding the disruptive plasma produce eddy currents in the vacuum vessel shell. Lorentz forces are exerted on the vessel when the eddy currents cross both the poloidal magnetic fields and the stronger toroidal magnetic fields of the tokamak that confine the plasma.
During a VDE, eddy currents are larger in magnitude because of how close the plasma gets to the vessel wall and VDE is therefore the test case of choice in the computational model of the ADX. Figure 3 shows the eddy current distribution calculated from the numerical model. A second model was developed to determine the Lorentz forces due to the toroidal magnetic fields of the tokamak, where only poloidal fields were included in the first model of the ADX.
Strengthening the ADX vacuum vessel
Plasma disruptions result in strong Lorentz forces that act on the walls of the ADX, particularly in the upper and lower pockets of the vacuum vessel during a VDE. In a structural model of the ADX vessel, shown in Figure 4, the top and bottom boundaries are attached to the vessel cover and cannot be displaced during simulation. Loads corresponding to the Lorentz force exerted on the vessel are applied to the relevant boundaries. In this test case, the Lorentz force was determined for a tokamak operating with a 1.5 million ampere plasma current and 6.5 Tesla toroidal field strength.
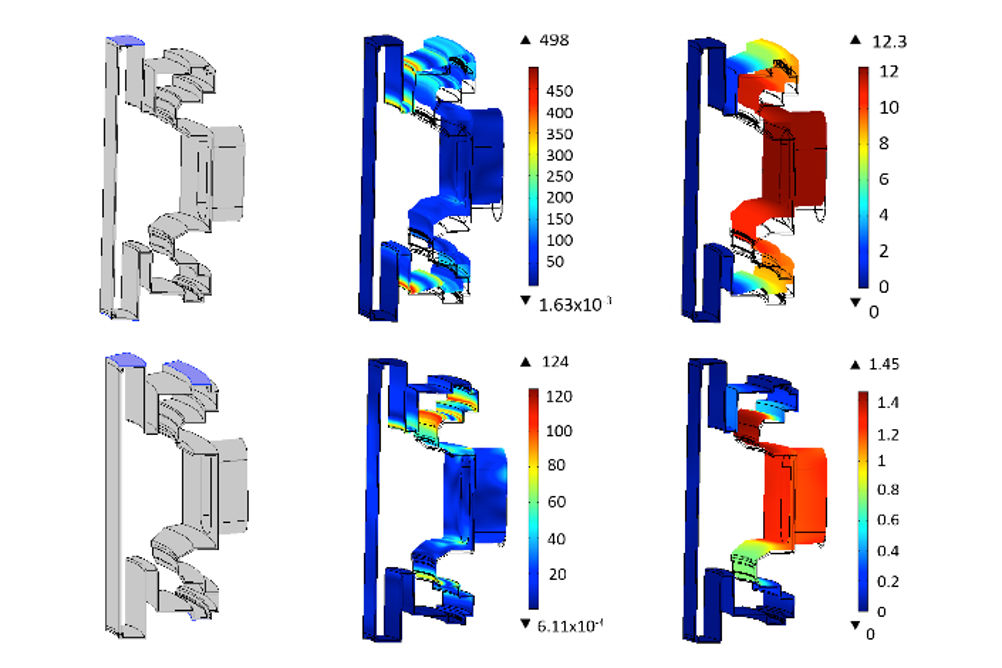
The modular vessel components are made from Inconel 625, a strong nickel-based alloy that is also highly resistive to current flow, keeping eddy currents to a minimum. The yield stress for the material is 460 MPa, however the design criteria for the ADX stipulates that the vessel walls should not experience stresses exceeding 306 MPa, which is two-thirds of the yield stress value.
Numerical simulation shows that, without any design modifications, the Lorentz force due to a VDE leads to large stresses in the vessel approaching the yield value and causing 1-centimetre deflections in the structure. To stabilise the vacuum vessel wall, a support block is added to immobilise an additional boundary as shown in the bottom row in Figure 4. Simulation results, obtained for the case with the support block in place, demonstrate significantly reduced stress and displacement of the vessel wall, indicating that the stabilised vacuum vessel can survive a plasma disruption and support ADX operation.
Next-stage nuclear fusion and beyond
Simulation-led design of the ADX will help ensure its safe, successful operation at PSFC, where it will become the newest fusion machine to serve as an R&D platform to test the divertor concepts required for a fusion reactor.
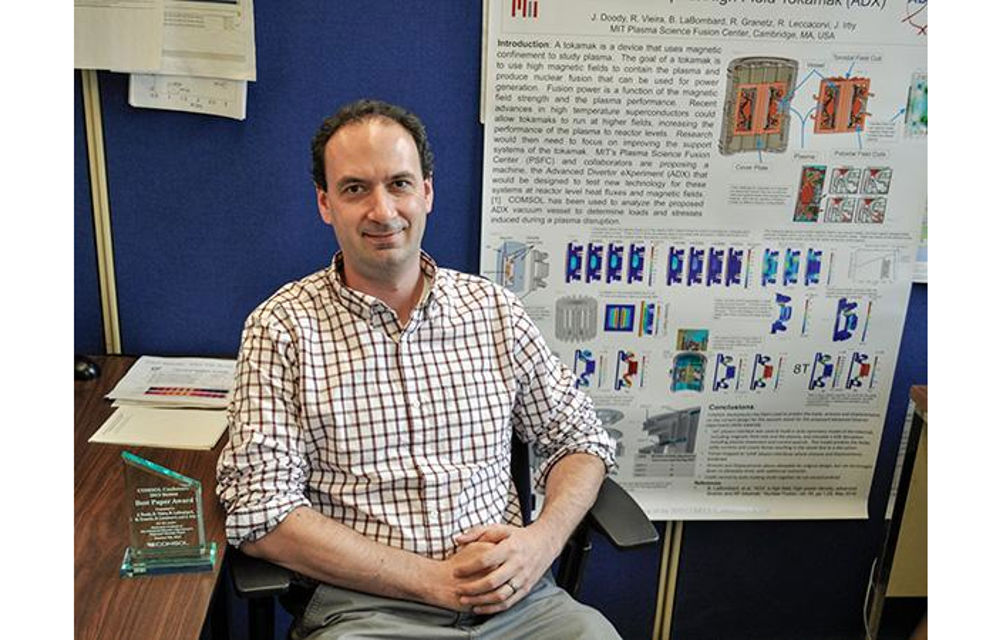
IET sounds warning on AI doll trend
I agree that we need to reduce cooling water demand for servers. And yes, generative AI consumes a large amount. But what about BitCoins? Their...