If your grandad was an engineering pioneer, having worked alongside legends like Frank Whittle in the earliest days of the jet age, it could be something of a mixed blessing, pedigree and inspiration battling against the long shadow of achievement.
“I certainly remember as a kid, you know, being younger than 10 and there being a bit of an aura around Grandpa Bob and some of his achievements with jet engines and then gas turbines,” Tim Woolmer, grandson of Bob Feilden, told The Engineer.
“I wish we’d been a bit closer in age gap, because I would have loved to have picked his brains an awful lot more. He was already well into his 80s by the time I was really getting interested in engineering, but there was enough crossover to have some good chats.”
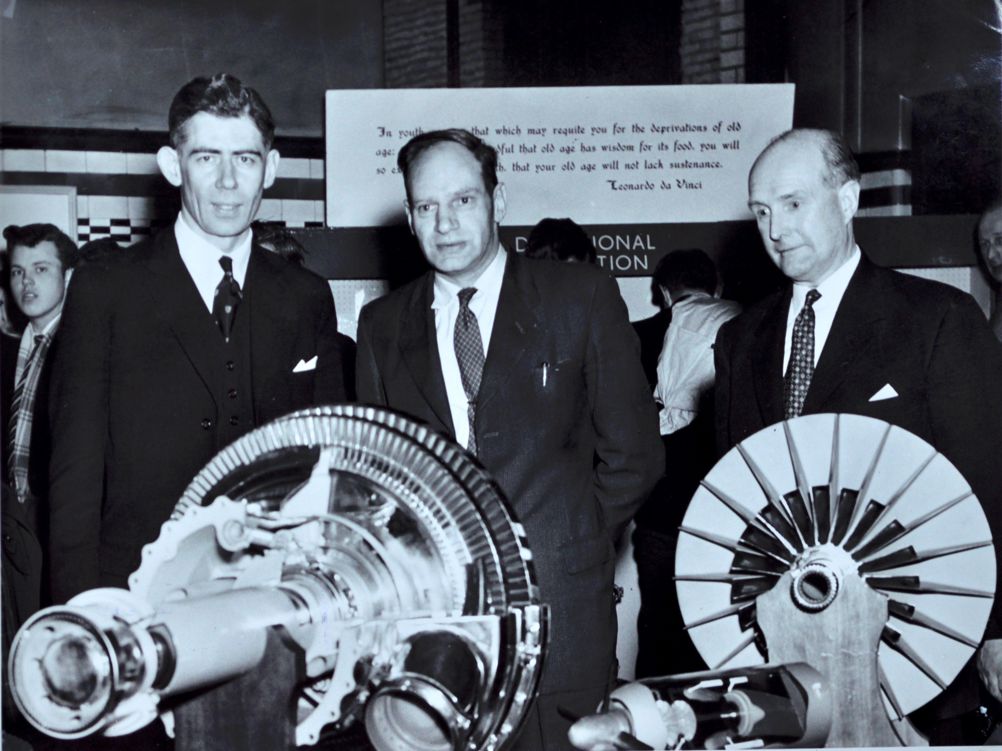
For Woolmer, his engineering heritage certainly seems more boon than burden. He founded automotive firm YASA in 2009 while still studying at Oxford. Ten years later, the company’s electric motors were chosen by Ferrari for the SF90 Stradale, the Italian marque’s first full production hybrid. In 2021, YASA was acquired by Mercedes-Benz, but not before Woolmer and colleagues spun out sister company Evolito, with the goal of adapting YASA’s cutting edge motor technology for the burgeoning electric aerospace market.
“My time split is about 85 per cent Mercedes/YASA and 15 per cent Evolito,” said Woolmer. “Evolito is kind of like a bit of hobby for me, if that makes sense, because I love aerospace. I’m not directly involved in the details of the engineering, but I’m quite involved from a strategy, high-level point of view and doing a lot of technology transfer as well.”
At the core of both companies is YASA’s proprietary axial flux technology. With an axial flux motor, the spinning rotor turns alongside the stator rather than inside it, creating a bigger radius which delivers more torque for the same power. YASA claims its motors are four times as powerful (in terms of Nm/L) as the current radial flux motors used in most of today’s EVs, as well as 50 per cent lighter and smaller.
In automotive, these sorts of numbers are damn impressive, as Ferrari and Mercedes would no doubt attest. But in aerospace, they have the potential to be truly revolutionary. The plan at Evolito is to build on YASA’s success, optimising the axial flux technology for the aerospace market.
“We can probably double if not treble the power density by using some aerospace materials whilst keeping the product at an acceptable cost,” said Woolmer. “We’re not making it non-mass-producible or putting in crazy materials. We’re getting that blend right. And that’s probably roughly a doubling or trebling of performance, which is pretty remarkable, because it’s a very high-power density product in automotive.
“In automotive, our products are about 15 kilowatts per kilogramme, which is about three times today’s Tesla numbers. In aerospace we think, hey, we can target 50. Why not go for a 50 kilowatt per kilogramme machine. Imagine something that’s weighing like four kilos that can knock out 200kW - that’s the goal that we’ve got for Evolito and we think we’ve got a very realistic chance of getting there.”
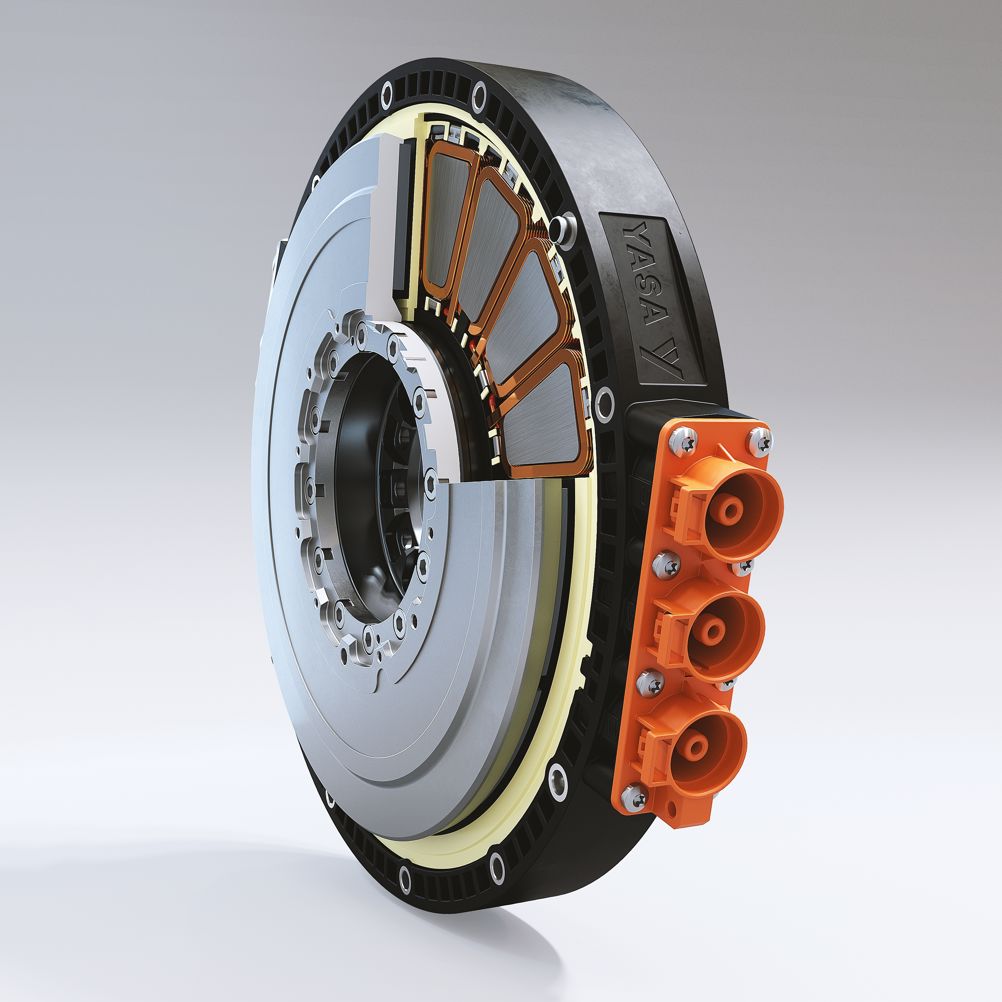
With such huge potential in the nascent eVTOL (electric vertical take off and landing) market, it’s a wonder it’s taken YASA so long to pivot towards aerospace. Woolmer says it was always on the radar, but the relative maturity of EVs versus eVTOLs meant that automotive naturally became the company’s bread and butter.
“We all said ‘hey, we really want to do aerospace’, but we’d got too much work to do in automotive and the team was growing such that any resource that was allocated for aerospace just got dragged into automotive essentially,” said Woolmer.
“I think had we not spun out the company, we probably still would have five people working on it and not made any progress. So I think that’s been the key lesson...if you’ve got a very stretched business and it’s trying to do R&D in a different sector, it’s very hard to do.”
Automotive commitments may have taken precedence over aerospace ambitions, but YASA has still found time to stretch its wings. The company provided the three electric motors that powered Spirit of Innovation to multiple world records as the fastest electric aircraft (555.9 km/h over 3km) and the fastest overall electric vehicle (623km/h) at the tail end of 2021.
The groundbreaking plane was developed in partnership with Rolls-Royce and battery startup Electroflight as part of the government backed ACCEL (Accelerating the Electrification of Flight) project. Evolito subsequently acquired Electroflight, essentially reuniting the powertrain partners from a project that smashed the existing record for electrically powered flight by 213 km/h - not a bad stat to have on your new business card.
“Obviously that programme has been an amazing project,” said Woolmer. “Electroflight did actually most of the engineering on the aeroplane. They did all the battery pack, all the structures, all the system integration. YASA’s involvement was to supply motors and inverters, but I’d say in terms of effort, engineering effort, I’d say it was 80 or 90 per cent Electroflight’s project.
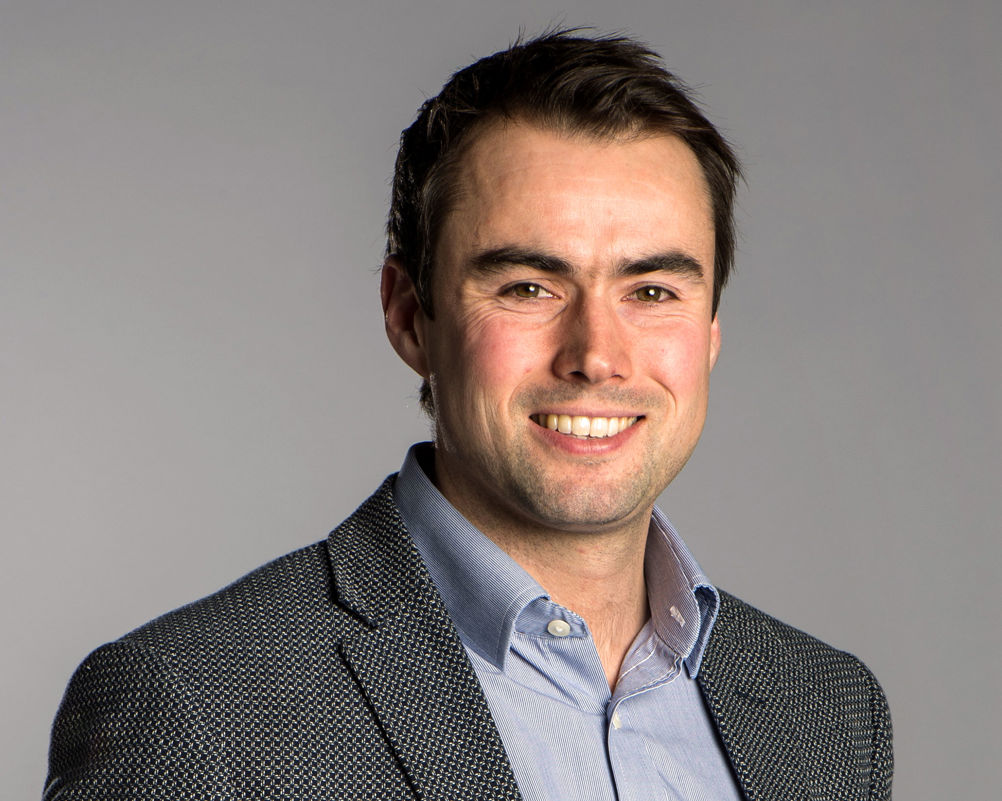
“So we found some phenomenal capability with Electroflight...they’ve got the energy and the power technology, the integration technology. We’ve got the propulsion technology, so it’s just a perfect marriage…it gives Evolito this wonderful option to sell full powertrains. Whether it’s VTOLs or fixed wing aircraft, we’re doing some really interesting system optimisation with them at the moment.”
Although most of the core technology around eVTOLs is well established, lightweighting remains a key issue. Evolito’s power dense motors not only deliver on this in their own right, they also have a cascading effect across the rest of the vehicle.
If you add weight to an electric motor, it generally has a compounding effect elsewhere, with weight added across a variety of other components. But this also works in reverse, with weight savings bringing compounded benefits. In automotive, this phenomenon tends to manifest in a ratio roundabout 1:1. In aerospace, the ratio can be much higher, with variance in weight magnified several times over.
“In VTOLs, that ratio goes up from one-to-one to somewhere between a three-, maybe in some cases up to an eight-to-one,” said Woolmer. “In other words, if we can demonstrate that we can save you 100 kilos on your VTOL powertrain, that will cascade around hundreds of kilos of saving on the whole craft. And what everyone is battling with in VTOLs is weight.”
There’s certainly no shortage of entrants in the eVTOL sector, but it’s a market that has largely overpromised and underdelivered so far. Videos of demonstrator flights are all over the internet. However, the electric air taxi services being muted for almost a decade have yet to materialise.
Several factors have contributed to this, not least certification and air traffic management concerns. The last thing anyone needs is aircraft dropping from the skies above crowded cities. While safety issues are often attributed with holding back the revolution, according to Woolmer, the bigger hurdle is scaling up to factory production.
“We saw this with electric cars,” he said. “You can make an electric car demonstrator quite easily, right? I mean it’s not actually that complex to get one vehicle on the road. It’s a bit more complex to get one VTOL in the sky, but it’s still not that complex, right? The hard bit is the scale up and that’s the bit that will be more expensive and take longer than the public realise.
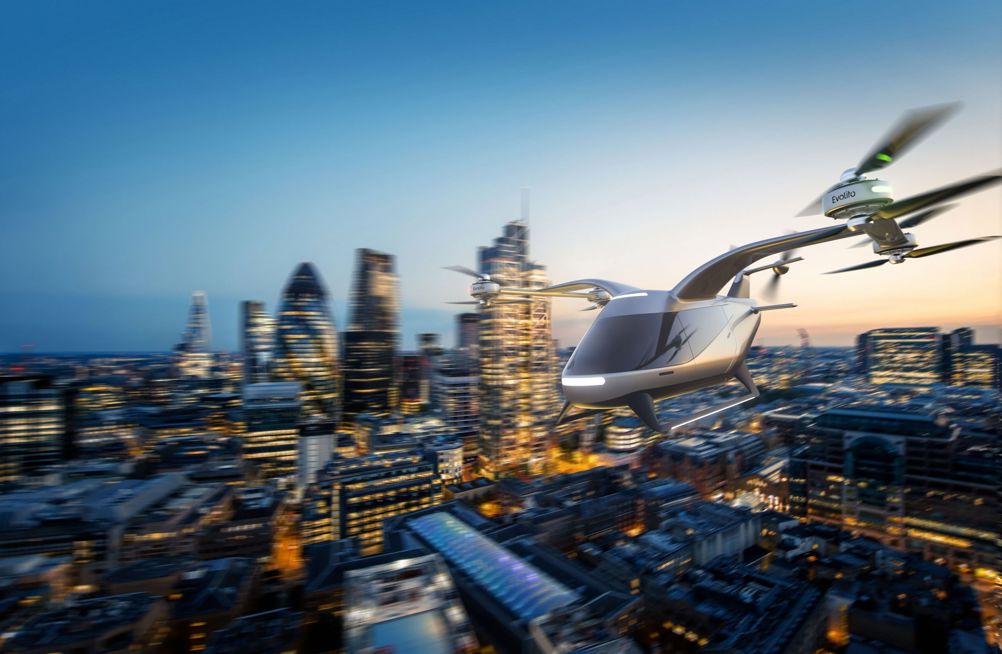
“The thing that takes time is developing all the technology that goes in that factory to make the parts consistently, all the information on a database, all the controls required, whether it’s automotive or aerospace. That could take five, six, seven, eight years - that’s the core IP of your company.”
But for Evolito, it has a sister company that’s been building out its manufacturing capacity for more than a decade and is now backed by one of the biggest names in motoring. This competitive advantage means the company can actually deliver big numbers of powertrains when the eVTOL goldrush finally gets underway. Picking winners from the crowded field of contenders may turn out to be the biggest challenge.
“The beauty of YASA’s situation is that we’ve already got factories that can do 10,000 units a year,” said Woolmer.
“In a sense there are too many opportunities, so it’s really about picking the right customers. The ones that you really believe are going to make it into production...we don’t want to work on 20 development projects, and none of them go into production. We’d rather work on two development projects and both of those go into production.”
Hard to know what Grandpa Bob and Frank Whittle would have made of it all. Probably be worth a listen, though.
McMurtry Spéirling defies gravity using fan downforce
Ground effect fans were banned from competitive motorsport from the end of the 1978 season following the introduction of Gordon Murray's Brabham...