Transitioning to a low carbon economy is an endeavour so vast and varied that it can sometimes boggle the mind when attempting to conceive of it in totality. Energy, transport, food, manufacturing, construction – individual areas, each with enormous challenges to overcome, each with different technologies and approaches that we hope someday will collectively enable a net zero future. However, there is an underlying principle in our approach to virtually all these sectors, one that we must fundamentally shift in order to ensure our continued survival.
The vast majority of our economic activity across the globe is linear, a ‘take, make, waste’ model where resources are turned into products or outputs that ultimately end up as landfill or pollution. A linear economy is not only damaging to the environment, it is also unsustainable over the long-term, with economic growth intrinsically tied to the depletion of finite resources. A circular economy seeks to close the loop on those resources by reusing and recycling energy and raw materials. In many ways, circular economy can be considered a blueprint for humanity’s future, a way to eliminate waste, protect the environment and develop a model for sustainable growth.
“It’s quite a natural progression to be starting to think about, you know, how you can keep your items or material inside a closed loop or a tighter loop,” Joshua Young, circular economy manager at PragmatIC, told The Engineer. Founded in 2010, the Cambridge-based firm has been making waves with its novel ultra-low-cost flexible electronics. PragmatIC’s technology – backed by several big names including UK chip giant Arm - can be embedded into virtually anything, cheaply transforming vast numbers of items from ‘dumb’ to ‘smart’ and enabling things like packaging to be tracked, collected and reused.

“It’s that thought process of thinking of packaging as an asset rather than waste,” said Young, “effectively creating a system which is underpinned by digital technologies - and of course PragmatIC technologies - to be able to track and identify items throughout whole life and through multiple uses.
“If you were to move 20 per cent of packaging to reusable, it’s a $10 billion opportunity. And so I suppose that’s a starting point.”
PragmatIC is currently involved in a variety of schemes to trial its technology in circular applications. At the forefront of these is TRACE, Technology-enabled Reusable Assets for a Circular Economy. Using low-cost PragmatIC NFC (Near Field Communication) chips, the project will see reusable containers given unique digital identities (UIDs) which will allow stakeholders right across the supply chain to track the journey of the packaging, from the primary manufacturers, to retailers, consumers, recycling companies, hopefully looping all the way back to re-use.
Funded by Innovate UK via the Smart Sustainable Plastic Packaging Grant, TRACE will initially focus on food and drink. Other parts of the FMCG (Fast Moving Consumer Goods) sector already have higher – though by no means high enough – levels of reuse. With food and drink, the sheer volume of single-use packaging is enormous, presenting both a huge challenge and opportunity.
“Even if you just look at beverage bottles as an example,” said Young. “I think in the UK we use 14 billion plastic bottles every single year. And so actually, if you’re able to move just one product category there to reusable packaging, you can imagine some of the kind of savings which you could have in comparison to single use and recycling.”
Other low hanging fruit includes, well, fruit, alongside vegetables, dry goods like rice and pasta, and the ‘grab and go’ segment where things like pasta pots and salad trays are bought and disposed of in their millions each week across the country, particularly at lunchtime. The decision to go with NFC rather than alternatives like RFID was a deliberate one to try and actively involve consumers in the programme. Virtually every smartphone today has NFC capability, which can be used to inform consumers about the benefits of TRACE, as well as highlighting recycling points and even facilitating deposit or reward schemes.
“We think that consumers are a critical part in the overall system and we need to enable them and provide them with the right information and to make it accessible to them to make them participate,” said Young. “At the end of the day, if a consumer doesn’t participate and return the packaging then actually it’s not going to be reused, is it? It may as well be single use.”
PragmatIC is working with recycling charity RECOUP to put together ‘reusablility by design’ guidelines that should help manufacturers, brands and retailers make the leap from recycle to reuse. According to Young, the aim is to come up with a uniform standard that can then be rolled out across the sector. “We think that’s going be really impactful for the industry to accelerate the transition towards reuse.”
The project, which kicked off in February of this year, also includes waste-mapping specialist Topolytics, alongside the University of Sheffield, the Advanced Manufacturing Research Centre (AMRC) and Ken Mills Engineering. The breadth of the collaboration is encouraging, but the list of partners is notable for its lack of major retailers. Young says that TRACE is in advanced talks with most of the large supermarkets and that several are expected to participate in the first open loop trials, due to start towards the end of 2022.
“It’s imminent and we’re working hard obviously to confirm those,” he said. “We’re certainly speaking to all of them, but confirming the trials and getting commitment, that’s what we’re focusing on right now.”
PragmatIC’s TRACE programme is a good example of what most people envision when they think about circular economy - the reuse and recycling of physical goods, things sorted into different coloured bins, intelligently managed to extend or repurpose their existence. Similarly, the waste associated with physical products at their end-of-life is visible all around us, from the single use plastics that wash into our rivers and seas, to the mountains of landfill we collectively produce across the planet.
What’s less visible – but no less damaging – is the waste inherent in our energy systems, from heat loss in inefficient homes to industrial heat lost to the atmosphere. Regarding the former, support for heat pumps and better insulation for UK homes has been largely ignored by government, despite what many consider an easy win for both the environment and consumers’ pockets. For industry, where the pinch of the energy crisis is also being keenly felt, one UK startup has developed a heat pump solution that it believes can help ease the sector’s woes.
Greensteam is a high temperature electric heat pump that takes waste heat from industrial processes and upgrades it to high-grade heat that can be reused on site. Futraheat, the London-based company behind the technology, claims Greensteam could allow some businesses to reduce their industrial energy consumption by up to 90 per cent. The firm has already developed a 300kW demonstrator capable of taking sub-100-degree waste steam and upgrading it to around 130 degrees Celsius. Off the back of that, it recently received £149,000 via the BEIS Industrial Fuel Switching competition to roll out two 500kW Greensteam pumps, with a focus on the pharmaceutical and food sectors.
“Up to 70 per cent of all industrial energy demand is for heat in sectors including pharmaceutical and food manufacturing,” explained Tom Taylor, Futraheat’s managing director. “This heat is commonly provided as low-pressure steam, and in many cases it is used once and then released to the atmosphere as a waste stream.
“Our ground-breaking Greensteam heat pump can recover much of this lost heat – as low as 70 degrees Centigrade – and boost it cost-effectively to the high temperatures that industrial customers require. This can deliver CO2 reductions of around 80-90 per cent, rising to 100 per cent if electricity from renewables is used.”

At the heart of Greensteam – and key to its efficiency – is Futraheat’s patented TurboClaw compressor. Created specifically with industry in mind, it operates without oil at a relatively low 20,000 RPM, compared with the 60,000 RPM you’d typically find in a comparable centrifugal compressor.
“When it comes down to the physics with TurboClaw, we’re able to bring the benefits of centrifugal compressors, but down to the kind of flow rates that typically you would use a positive displacement compressor at, so we can bring those benefits into that range,” said Taylor.
“That generally comes down to the fact that we can produce a like-for-like pressure ratio at a lower rotational speed, which basically makes the engineering lots simpler, makes it easier to design.”
This manufacturability should allow production to be ramped up quickly if the upcoming commercial trials are successful and the technology takes off. According to Futraheat, the opportunity is massive. Up to 20 per cent of industry’s heat requirements could be met by high temperature heat pumps, with widespread adoption in Europe alone reducing CO2 emissions by 80 million tonnes per year – a truly virtuous circle combining greater efficiency, lower bills and decreased emissions.
“The corporate world is really pushing this,” said Young. “Of course, there are international, national targets for net zero, but really it’s being driven in industry by the companies themselves because they’ve committed to shareholders that they’re going to achieve net zero not in 2050, but maybe 2030/2035. And of course, if you’re going to invest and change a lot of your plant, your facilities, your capabilities, then you’ve got to start now.”
Obviously, a more circular approach in both industrial heat management and food packaging has always been possible, with the impending urgency of the climate crisis simply acting as a powerful recent catalyst. Why reuse a PET bottle when virgin plastic is so cheap and readily available, or recapture heat when gas prices are rock bottom? But circumstances and attitudes can shift quickly, and the rapid change now demanded of us is forcing the adoption of practices we probably should have been embedding in our economy for the past several decades.
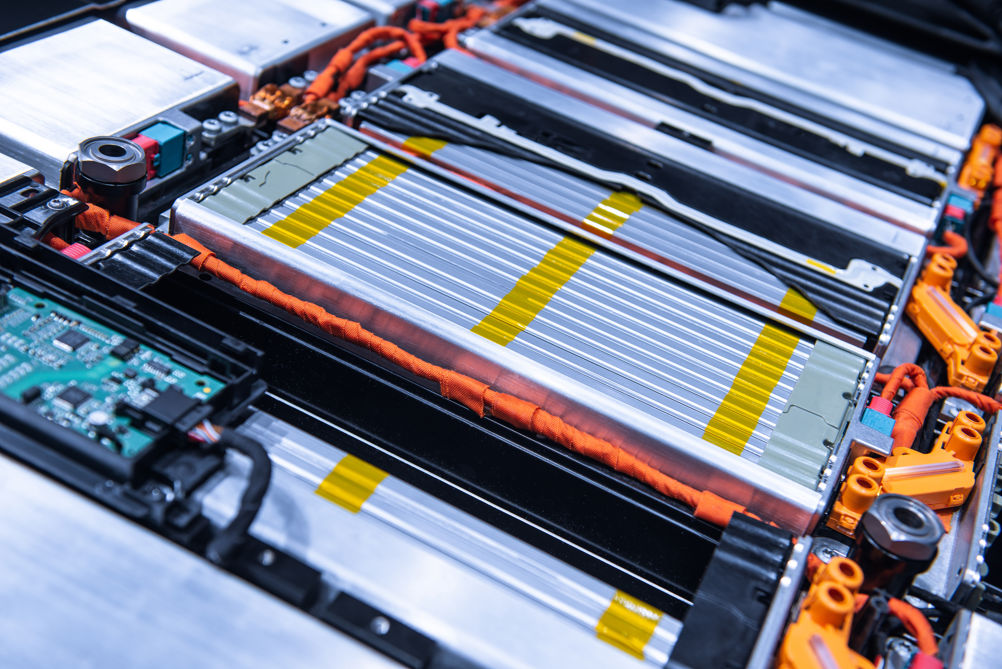
That same rapid path is also throwing up new challenges, new puzzles around incorporating circularity into the very technology required to help us decarbonise. Massive wind turbines made from composites coming to their end-of-life. Ageing photovoltaics that are increasingly inefficient compared with the latest materials. The debate around biomass and its circular credentials in our energy system. But perhaps the biggest environmental and circular challenge of this age is that of batteries.
Many first-generation EV batteries are now reaching end-of-life, posing a significant environmental challenge for a sector heralded as a major part of the climate solution. As more EVs get rolled out, the problem is only set to grow, compounded further by the grid-scale battery storage systems now popping up around the world. We need answers and we need them fast. Thankfully, a new Scandinavian project appears to have them.
Claimed as the largest battery recycling plant in Europe, Hydrovolt will recycle 12,000 tons of battery packs per year, or around 25,000 EV batteries. The company is a joint venture between Swedish battery manufacturer Northvolt and Norwegian aluminium giant Norsk Hydro. The plant, which opened in May 2022, is in the Norwegian city of Fredrikstad and has enough capacity to process the entire end-of-life battery market for Norway, one of the world’s most mature EV markets.
“What we do at Hydrovolt is that we collect batteries at the end-of-life and we bring them into the facility,” Emma Nehrenheim, chief environmental officer at Northvolt, told The Engineer. “We do the discharge and dismantling - basically just taking it into slightly smaller pieces so that they can fit into a normal crusher.
“Then we have a huge shredding/sorting process where we crush the batteries and we get the mixture of crushed foils, cans and this black mass. Then we have a sorting where we get copper, aluminium, plastics and black mass in different bins.”
The black mass Nehrenheim talks of is a compound containing nickel, manganese, cobalt and lithium, elements essential for the ongoing production of lithium-ion batteries, but which end up muddled together in a powder-like state following the initial shredding and sorting stages. Separating the black mass out into its component parts is one of the processes that allows up to 95 per cent of the EV battery material to be recycled.
“What we do is basically we dissolve everything in acid,” Nehrenheim continued. “And then we have some steps where we remove the impurities. And the impurities are basically anything that is not nickel, cobalt, manganese or lithium.”

Most of the recovered materials are fed back to Hydrovolt’s parent companies – aluminium to Norsk Hydro, black mass to Northvolt – with the copper sold on the market and the plastics recycled. Having established Europe’s first ever gigafactory in northern Sweden, Northvolt now has its sights set on incorporating as much circularity into its processes as possible, reducing its reliability on raw materials from an increasingly volatile global marketplace.
In November 2021, it produced its first cathode material using 100 per cent recycled nickel, manganese and cobalt. By the end of the decade, it plans for all Northvolt batteries to include 50 per cent recycled materials, a major leap forward from the highly linear way that battery manufacturing works today. There are plans for capacity to recycle 150,000 batteries per year by 2025 and 500,000 by 2030. This will be enabled by additional co-located recycling capabilities at Northvolt’s second and third gigafactories, sited in southern Sweden and northern Germany respectively, closer to the large population centres and OEMs where EV batteries are likely to accumulate at end-of-life.
“We have a very strong collaboration with our OEMs to get the material back,” said Nehrenheim. “The focus is to get industrial scale and to get a good balance between that and the distribution. So logistics versus scale, and we’re coming into a really good plan with that where we can manage to be effective and cost effective, but also safe when we dismantle this huge amount of batteries that needs to come back.”
This long-term strategic planning, combined with meaningful, immediate action, is exactly what’s required to transition our economic model from linear to circular. There are undoubtedly technological hurdles, but just as with the energy transition, the tools required are all within our grasp.
Perhaps the biggest barrier to embracing the circular model will be psychological rather than technological. Our entire civilisation has been built on the notion of disposable economy, the learned behaviour of waste passed on from generation to generation. Shifting those longstanding beliefs and habits is a daunting task, one that will require a revolution of minds more so than of manufacturing and materials.
Radio wave weapon knocks out drone swarms
I hope they have assessed how easy it is to shield a drone against the attack. Hopefully the shielding would add too much weight.