The concept of the circular economy - which aims to minimise waste and make more efficient use of resources by designing products to be reused, repaired, recycled and remanufactured - is now reshaping most areas of industry and transforming the way that products are designed and made.
But whilst the sustainability and efficiency benefits of a circular approach straddle every area of industry, the practicalities and challenges of deployment vary from sector to sector.
The Engineer asked a cross-sector group of experts from some of the UK’s leading engineering organisations how they’re facing up to the circularity challenge.
In this article we hear from Rolls-Royce Plc about its Revert Programme (a company-wide initiative aimed at recovering, recycling and reusing waste materials). We learn about the Warwick University-led CENTS (Circular Economy Network+ in Transportation Systems) programme, an EPSRC-funded research network for the sustainable transport community. We talk to the consultancy Buro Happold about innovative strategies for material reuse in the construction sector, and we see how industrial supplier Schneider Electric is using its technology to help its customers implement circular systems.
Meet the Experts:
- Charles Kinlock - Strategic Buyer, Materials, Rolls-Royce Plc
- Barbara Frei - Executive Vice President, Industrial Automation, Schneider Electric.
- Professor Kerry Kirwan - Head of the Sustainable Materials and Manufacturing Research Group within WMG
- Anna Woodeson - Director of Sustainability at Buro Happold

Why does your sector need to adopt circular economy principles?
Kerry Kirwan: The 20th Century was characterised by a massive global increase in all modes of transport, on land and water and in the air, for moving both passengers and freight. Whilst easy mobility has become a way of life for many, the machines (planes, automobiles, trains, ships) that enable this are both highly resource consuming and environmentally damaging in production, in use and at the end of their working lives. Over the years, great attention has been paid to increasing their energy efficiencies, but the same effort has not been put into optimising their resource efficiency.
The lack of embedded circularity within our transportation is very much a missed opportunity
The increased uses of rare earths and other more exotic materials in the drive towards electrification and hybrid vehicle platforms are amplifying environmental and materials security concerns even further today. The lack of embedded circularity within our transportation is very much a missed opportunity in terms of both the environment and the businesses involved in the sector themselves.
Barbara Frei: The Global Circularity Gap report for 2024 reveals a concerning trend: despite increasing material consumption, the global utilisation of secondary materials has dropped significantly from 9.1 per cent in 2018 to 7.2 per cent in 2023. This decline represents a missed opportunity. The potential of circularity is substantial, with estimates suggesting it could mitigate approximately 75 per cent and 60 per cent of CO2 emissions in the built environment and transportation sectors, respectively, by 2050.
For industry circularity represents a paradigm shift from the traditional linear model of “take-make-dispose” to a regenerative approach that emphasises the restoration and regeneration of products, materials and energy
Furthermore, it is projected to contribute to a potential 7 per cent increase in GDP by 2030. Therefore, the circular economy is not only environmentally beneficial but also a driver of economic growth. Various policies and incentives, such as the EU’s Circular Economy Action Plan and the US National Recycling Strategy, already provide a framework to support these efforts.
For industry circularity represents a paradigm shift from the traditional linear model of “take-make-dispose” to a regenerative approach that emphasises the restoration and regeneration of products, materials and energy. Its principles can reduce dependency on scarce resources and component suppliers, building adaptable and resilient supply chains.
Anna Woodeson: There is widespread acknowledgement that there is a serious problem. The construction industry accounts for approximately 50 per cent of material use and 62 per cent of waste in the UK. Setting aside carbon impact for a moment, we must also acknowledge the environmental devastation and social injustice caused by extractive practices linked to construction materials and a linear economy. Take copper, for instance. Its production utilises colossal amounts of energy - in excavating, grinding, and smelting - produces huge amounts of waste rock, damages the environment through water contamination, air pollution, habitat destruction and deforestation - and impacts the health of miners. It’s posing a fascinating challenge that we’re excited to meet.
Charles Kinlock: The most quoted definition for sustainability is: “the development that meets the needs of the present generation without compromising the ability of future generations to meet their own needs.” To achieve its long-term sustainability goals, the aerospace sector has adopted a more specific definition for sustainability in terms of three dimensions: techno-economic efficiency; environmental impact and social benefit.
The value of ‘recycling’ within the aerospace sector is further enhanced by increasing concerns regarding availability and security of supply of key resources. The UK government has identified a list of critical materials, including a number that are used in alloys for Rolls-Royce products.
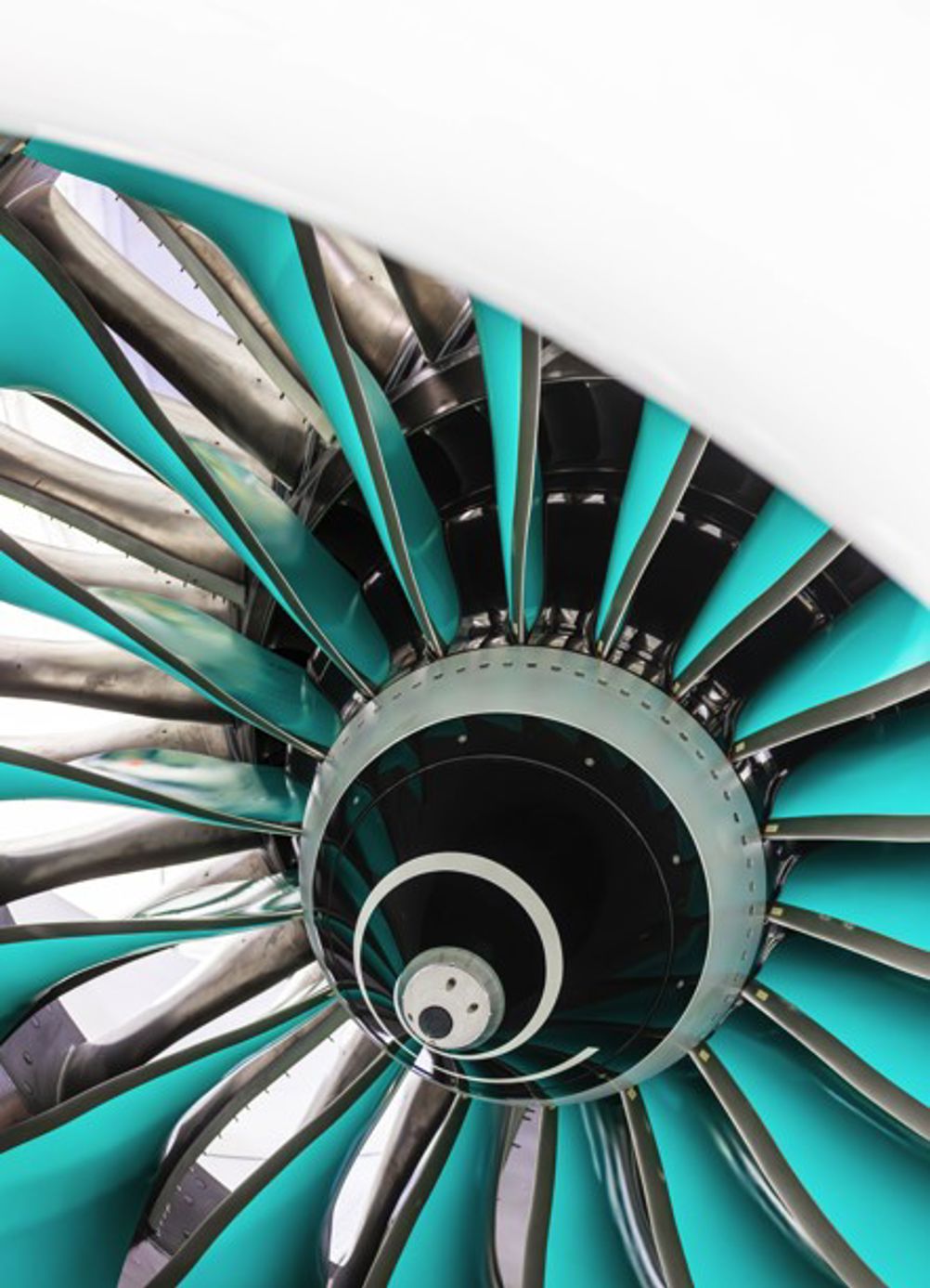
As we transform to become a high performing, resilient, competitive and growing business, how we manage the supply of critical materials is key to our resilience, in particular. We have mature methods for dealing with the resultant risks for price stability and availability of such critical materials. Over the past decades circular principles and models have been developed to deliver economic value, environmental benefits and to address security of material supply concerns.
Outline the potential benefits of embracing circular economy principles in your sector?
Kerry Kirwan: Although they may share a common origin in the raw materials used, the supply chains of transport sectors more or less operate in isolation. However, there are numerous potential benefits that could be realised if Circular Economy (CE) principles were applied across these supply chains. These include manufacturing economies of scale, recovery of energy intensive and/or technology metals, reuse/remanufacture of components, lower carbon materials substitutions, improved energy and material efficiency, materials security and provenance, and of course enhanced brand reputation. While CE thinking can change the transport system, the transport system can also enable or disable CE. By considering different transport systems as a collective, it is more likely that a cascading chain of materials and/or component supply could be realised – something that is historically very difficult within just a single sector.
Charles Kinlock: Reverting high value superalloys saves significant energy usage and reduces the CO2 emissions per tonne compared to the manufacture of alloys from virgin materials, dependent on the material [N.B Revert is the name of Rolls-Royce’s closed loop metals recycling programme]. There are also other environmental benefits, such as avoided water usage, avoided particulate emissions and avoided production of tailings/overburden. It improves our resilience at a time when supply chains are experiencing significant disruption.
The more stability we can bring to those supply chains, the smoother our delivery of products and parts are to our customers. This results in a greater availability of engines for our customers and subsequent revenues for us. In addition, recycling and reverting material in the Aerospace value chain facilitates discounted material price savings and positive cash-flow to the Rolls-Royce bottom line. The active management of Revert volumes is in addition to the value achieved from traditional recycling activities.
There is also a social benefit of Revert in creating employment. This requires a global network of suppliers to support a wide range of activities across Rolls-Royce manufacturing and maintenance, repair and overhaul sites.
Anna Woodeson: Current practices create employment and other economic benefits; therefore, any transition will need to create jobs and wealth. The good news is that the circular economy can also provide this, including 90,000 new jobs created between 2014 and 2019. Estimates of potential job creation within this area are now much higher as the opportunities unfold in a circular economy that uses more labour and fewer resources to increase the efficiency of economic activity. Indeed, WRAP estimates there could be an £82 billion boost to UK gross value added though the circular economy, albeit not just the construction sector.
With 42 per cent of carbon emissions controlled or influenced by the built environment, embracing the circular economy offers immediate carbon reductions from the initial build, further reductions throughout future maintenance cycles and adaptations, and then more at the end of the building’s life.
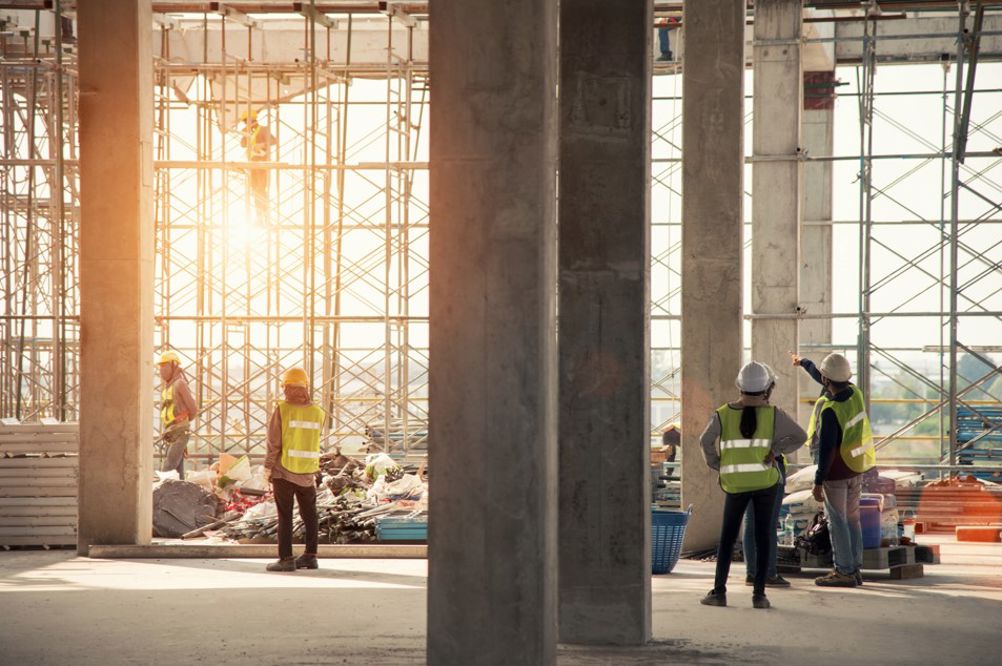
The opportunity to rethink design through a circular lens inevitably leads to prioritising the retention of existing buildings and structures but it also prompts a different approach to design and construction. A paired back, pragmatic approach where future adaptability is prioritised and buildings become easier to operate, maintain and adapt.
What are some of the key measures that can be taken to achieve this?
Kerry Kirwan: The first thing we found was that there was an overriding recognition that the current approaches to material usage was less than optimal – which was at least a good place to start – and that people were keen to talk and learn from each other (whether they were in direct competition or not).
The biggest common issues we found are the usual barriers to change – risk, cost, knowledge of alternatives to the current, skills, tradition etc., but not necessarily hard science or technology aspects. Unsurprisingly, given that our transport systems have developed over a long period of time, and are governed by multitudes of practical constraints including legislation and taxation, it is going to take a while to change things.
A major aim of CENTS [ The University of Warwick-led EPSRC-funded research network for the sustainable transport community] was to bring all the challenges to the table and then break them down into manageable ‘chunks’ where co-created research could yield small, but significant results that then enabled organisation to take bigger, bolder steps on the path to more circular practices – this has proved successful and the community’s work is ongoing and growing daily.
Charles Kinlock: Rolls-Royce has put in place some key measures to achieve success, such as engagement with all stakeholders to embed the importance of the benefit; a network of suppliers to manage the flow of material and to maximise yield and return of the alloy back to the melter for re-use; securing ownership of the scrap metal within its supply chain by enacting the Revert clause within our supplier contracts.
A key enabler is reliable and consistent data management to show where the alloys are being generated and the level of cleanliness and segregation being achieved. Rolls-Royce also works strategically with supplier partners on new developments to increase revert generation and with the academic field in novel research and development projects.
Anna Woodeson: Rehabilitation of the built-environment is not an easy fix – if it was, we’d have done it long ago. There are so many barriers to overcome including our tax system, procurement practices and, of course, our existing waste infrastructure.
Keeping 60+ million tonnes of construction waste produced in the UK in play each year requires a lot of space. It also requires more sorting and an infinitely more complex waste transportation network. It requires a major industrial transformation.
This requires planning. Whether provided by the private or public sector, storage, repurposing facilities, and material banks will need to be integrated into our towns and cities. Manufacturers will also need to become used to take back schemes and incorporating material reuse into their manufacturing processes. There are encouraging moves in this space, but major political and financial backing is required for circular economic principles to fulfil their potential in time to make a real difference.
Manufacturers will also need to become used to take back schemes and incorporating material reuse into their manufacturing processes.
Legislation including mandating pre-demolition material audits and establishing reuse targets will help galvanise our industry but is a per cent reuse ‘on site’ target the best method? We heard recently of one UK project exporting their construction waste abroad to turn into flooring, which was then reimported to achieve ‘on site’ targets. Clearly in this instance, the rules failed to achieve the intended outcome. However, clearly mandating escalating percentages of reuse in construction should be welcomed. In addition, we can mandate the use of material passports and construction approaches that facilitate maintenance and future adaptation. We can move away from buildings that cannot be disassembled, to less composite construction, less glue, and fewer wet trades on site.
The adoption of circular construction requires systems change. Take procurement as an example. Does the practice of design team innovation and the substantial risk transfer to contractors embedded within most contracts ensure we are all taking enough responsibility for delivering a circular construction industry?
On the fiscal side, a tax system that prioritises the retention of existing buildings would surely lead to a rebalancing of VAT between existing and new construction. In addition, reducing tax on labour relative to taxes on raw materials could help prioritise a circular approach.
A UK circular construction economy needs to be designed, planned, and delivered with the same care as the building projects it supports.
Can you give some examples of how your organisation is driving the deployment and adoption of circular principles?
Charles Kinlock: Rolls-Royce operates a collaborative metal recovery program globally with key material suppliers. The recovery of high value superalloys used in its metals value chain creates a virtuous circle. Return of alloys and elements that are no longer re-used can be reclaimed and incorporated back into the supply chain manufacturing of new components, thus substituting the use of virgin materials (i.e., rare metals and exotic alloys).
The Rolls-Royce Procurement team has deployed lifecycle management tools to map the end-to-end flow of its Revert activities to identify further opportunities. Today, Rolls-Royce returns superalloys from manufacturing, repair and end of life materials across its whole value chain. This cradle-to-grave approach is underpinned by a bespoke supplier network that has the capability to break down and recycle a significant amount of a whole engine. Rolls-Royce has also designed and developed its next generation superalloys to be more sustainable.
Anna Woodeson: While difficult, introducing circularity is possible. Buro Happold is helping drive the circular economy in so many exciting ways. We are creating the pre-redevelopment plans identifying reuse opportunities for a specific building or development. Our sustainability team are creating circular economy strategies for each development, also measuring reuse and its corresponding carbon impact, and then creating the material passports as the project progresses. Our structural teams are pushing innovative approaches to structural frame reuse. A recent example included jacking an existing structure to ensure the frame is retained but the required floor to ceiling height is achieved. Our façade teams are experts in the repurposing and retrofit of existing façade systems including historic retrofits, carrying out the necessary deep dive fabric investigations. Adopting a circular approach changes the way we solve problems. There is so much more to do! We’re looking forward to working in an industry that increasingly embraces the opportunities available with a circular economy.
Kerry Kirwan: CENTS is an EPSRC funded Network+ that initially convened many different types of transport stakeholders to focus on what the barriers to CE implementation in the sector were. It held several workshops, consultations and meetings where attendees brought their knowledge and experience to the table in a way that allowed difficult conversations to happen in a constructive manner. These multi stakeholder perspectives were captured into the CENTS Rich Picture which provided a common base from which researchers and industry could then work together with. CENTS then provided seed funding to different collaborations in order to identify synergies between different supply chains and to optimise certain practices, such as end of life recovery and recycling rates and energy and material efficiency. It also supported ‘forward looking’ thinking in terms of developing future designs, policy papers, business models and manufacturing approaches so that emergent transport systems can increase their circularity potential as we move forward.
Barbara Frei: We have embedded circular economy principles across multiple areas of our business. Like all programmes that reduce environmental footprints, circular transitions require a systematic approach: for us at Schneider Electric this involves designing products that are durable, repairable, and recyclable. We follow the principle of “design & innovate, use better, use longer, and use again.”
The ‘Design & innovate’ phase, affects product development and innovation and plays a pivotal role in maximizing value retention, influencing up to 80 per cent of a product’s lifecycle impact. At Schneider Electric, we regularly revitalize and redeploy our EcoDesign tools and training. These support teams like R&D deliver more value from extra reliability and longer life and develop new as-a-Service solutions.
Using better procurement strategies, we went from 7 per cent sustainable material content in 2021 to 32 per cent in 2024, with the aim of reaching 50 per cent in 2025.
The ‘Use better’ phase is about sourcing materials and manufacturing products as sustainably as possible, with minimal waste. For example, using better procurement strategies, we went from 7 per cent sustainable material content in 2021 to 32 per cent in 2024, with the aim of reaching 50 per cent in 2025. Similarly, we rose from 13 per cent to 63 per cent use of sustainable packaging in the same period, with the goal of reaching 100 per cent primary and secondary packaging by 2025, free from single-use plastic.
Beyond using recycled materials and renewable energy, smart factory operations - like connected machines, data and analytics - also contribute to circularity by creating new forms of efficiency and flexibility. For example, over four years, our Hyderabad plant reduced its energy consumption by 59 per cent, water consumption by 57 per cent, CO2 emissions by 61 per cent, while improving waste optimization by 64 per cent. It was recognized as a “Sustainability Lighthouse” by the World Economic Forum in 2023.
The ‘Use longer’ stage helps extend the lifespan of products to delay the need for new ones. It involves condition-based repair and digitally enabled maintenance and equipment modernization services.
Finally, the ‘Use again’ phase covers the recirculation of products, parts, and materials in the economy. That includes refurbishing and reselling assets that are reaching their end of use. Once a product is recollected at Schneider Electric, we evaluate whether to repair, reuse, refurbish, or recycle. We also include all relevant information when returning the product to the market, including performance. This is how we have avoided over 300,000 tons of primary resource consumption since 2017.
How are you working with others to help them embrace circular principles?
Barbara Frei: Collaboration is essential in advancing circularity, and at Schneider Electric we actively work with customers to integrate these principles into their operations. For instance, we recently partnered with GR3N in the plastics recycling sector. GR3N’s breakthrough new process addresses current hard to recycle PET waste while meeting virgin-like quality, effectively closing the loop for hard to recycle plastic. Schneider Electric incorporated its software-defined automation system and AI solutions to help scale these circular practices across the supply chain.
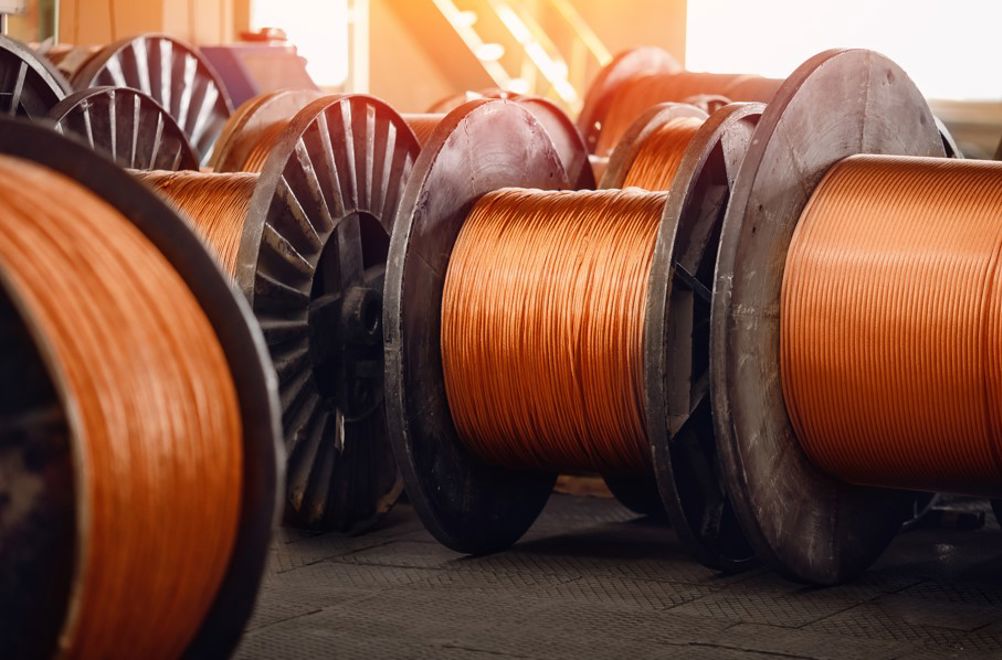
In mining, we are working with clients like Glencore to help transform its copper supply chain, embrace digitalization and automation to accelerate decarbonization efforts, build circular networks by using copper with high recycled content, and explore options for end-of-life take-back initiatives.
What’s more, across industry we are working to highlight the impact of industrial water use and how with our technologies we can help customers to better manage their water consumption and adopt circular of water reuse systems. São Paulo’s Aquapolo uses Schneider Electric’s solutions to optimize water recycling, showcasing how digital tools can foster circular water economies. By leveraging automation, data analytics, and AI, we help our partners build more resilient, efficient, and sustainable operations that contribute to long-term resource security.
McMurtry Spéirling defies gravity using fan downforce
Ground effect fans were banned from competitive motorsport from the end of the 1978 season following the introduction of Gordon Murray's Brabham...