Carbon fibre is becoming increasingly important in the automotive sector because of its high strength and low weight. However, its price confines its use to premium vehicles. Researchers from Washington State University now claim to have found a way to reduce its cost while also making use of a material that is currently discarded as waste.
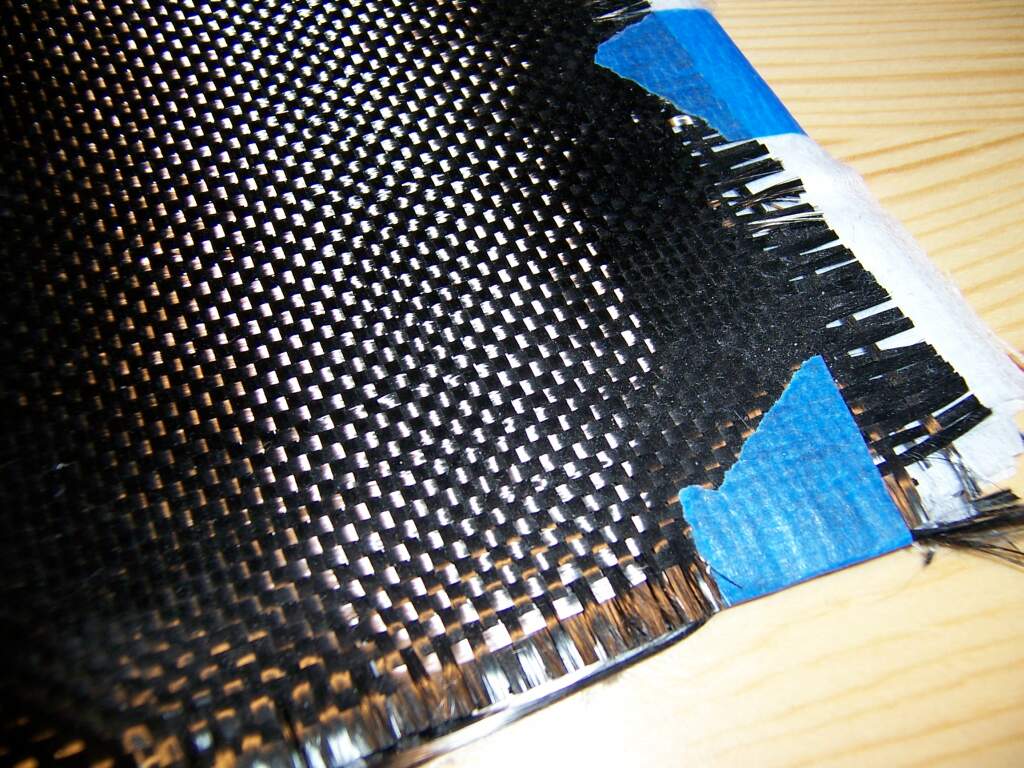
Lignin is the natural polymer that helps give wood its strength. A complex, fibrous structure of phenolic groups, it occurs in the cell walls of woody plants, making them rigid, But many industrial process that use wood or other tough plants as a raw material — notably papermaking and ethanol production in biorefineries — use only the cellulose content of the material, leaving lignin behind as a waste.
Currently, much of the waste lignin is burned to produce steam for biorefineries, or is simply sent to landfills. But researching ways to make better use of this waste stream, Birgitte Ahring and colleagues decided to look at using lignin a raw material for carbon fibre.
Burning lignin is not efficient, Ahring said. "Finding better ways to use leftover lignin is really the driver here. We want to use biorefinery waste to create value,” Ahring said at this week’s American Chemical Society meeting in Washington, DC. ‘We want to use a low-value product to create a high-value product, which will make biorefineries sustainable."
Previous efforts to used lignin for this purpose have not been a success because the resulting resulting carbon fibre has been too weak. Ahring’s team decided top try using lignin as a component in a carbon fibre precursor rather than the sole source of carbon.
Currently, most carbon fibre is made using polyacrylonitrile (PAN) as a precursor, PAN is strong, but expensive and non-renewable, explained Ahring’s colleague Jinxue Jiang. "PAN can contribute about half of the total cost of making carbon fibre," he said. "We wanted to combine the high strength of PAN with the low cost of the lignin to produce an automobile-grade carbon fibre."
The solution depends on a process called melt-spinning, which allowed the team to prepare precursor fibres containing up to 50 per cent lignin. You elevate the temperature of the polymer blend until it melts, so it can flow," Jiang said. "Then, you spin these polymer melts until the fibre forms."
Analysing the structural and mechanical properties of the resulting carbon fibre with nuclear magnetic resonance spectroscopy, calorimetry and electron microscopy, they found that adding 20-30 per cent lignin to the PAN did not compromise the fibres’ strength, and that they would be suitable for use in automotive applications in internal parts, castings and tyre frames. Non-structural components for aerospace might also be possible, they added.
The next stage of the research is to evaluate the fibres’ strength in components that could be tested in real-world automotive settings. "If we can manage to get a fibre that can be used in the automobile industry, we will be in a good position to make biorefineries more economically viable, so they can sell what they usually would discard or burn," Ahring said. "And the products would be more sustainable and less expensive."
Comment: Hydrogen requires a long-term mindset
Hydrogen does have and will have its uses. There are always "nay sayers" but these should not be confused with those raising issues that...