Joseph Bazalgette’s London sewers may be the greatest engineering feat of the Victorian age. Comprising almost 900km of tunnels lined with 318 million bricks, the system took just six years to build, during which time seven million cubic metres of earth was scraped out of the city’s underbelly and the River Thames was contained within permanent embankments, creating the landscape of modern London. The sewers diverted the city’s sewage, via huge, elaborate pumping stations in north-east and south-east London, to treatment works and out into the estuary, well downstream of most of the population. In building this system, Bazalgette immeasurably improved public health and the atmosphere of London, banishing the ‘great stinks’ from raw sewage flushed into the river and averting the risk of cholera epidemics, which had plagued the city for centuries.
Part of Bazalgette’s genius was in specifying the capacity of the sewer system. In the late 1860s, when the project began, London was at the tail-end of a population boom, with two million inhabitants. Bazalgette insisted on building enough sewers to cope with four million. But today, London has eight million people, and Bazalgette’s system can’t cope any more. Increasingly frequent overflow events, where untreated sewage spews into the Thames, are damaging the river’s ecosystem and leading to public health concerns. To counter this, a new system is being planned that will see a cavernous tunnel bored under the river, keeping the capital clean and healthy into the 22nd century.
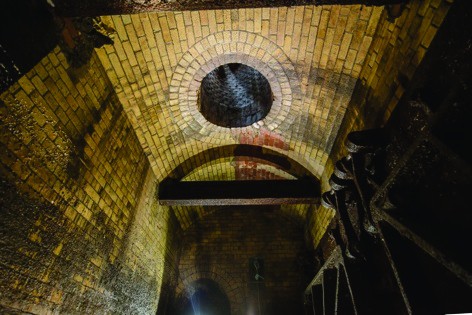
The Thames Tideway Tunnel, which is currently in the consultation stage awaiting a decision from government in the autumn, is planned to run from Acton in the west to Abbey Mills in the east; a 25km route, mostly following the line of the river. ‘Bazalgette had fantastic foresight; the problem is absolutely an issue of capacity and nothing to do with the condition of the Victorian sewers,’ the head of the Tideway Tunnel project, Phil Stride, told The Engineer.
Despite Stride’s assertion, there are other factors at work here, chiefly the design of Bazalgette’s system and the way London has developed since the 1860s. The sewers constitute a combined sewerage system; that’s to say, they carry both sewage — the waste from toilets, plugholes and drains — and rainwater in the same pipes. If rain swells the volume of liquid in the sewers that run under the city’s streets beyond their capacity, they overflow into purpose-built outflow pipes and discharge into the river.
Increasing population, and therefore more sewage, is one reason this happens more often now than it did in Bazalgette’s age. Another is the gradual concreting-over of open space. The rise of the motor car (and lack of space in the suburbs for garages) means that people have increasingly sacrificed their front gardens for off-road parking, and the rainwater that would have soaked away into flower beds now runs off into the gutter and to the sewer. Industrial and commercial development has also added to the problem, with open space — particularly on the edges of the city — taken up by industrial estates, supermarkets and shopping centres, invariably with large car parks, which also can’t absorb water.
As a result, a system that was designed in 1868 to overflow only when the rainfall level exceeded 6mm/hr, it now discharges into the Thames with as little as 2mm of rain. ‘There are discharges into the tidal Thames about once a week on average,’ Stride said, referring to the portion of the river below Teddington Lock. ‘In total we see about 39 million tonnes of sewage discharged into the river in an average year. In 2012, which is the last year we have complete figures for, there was about 53 million tonnes.’
And once it’s in the river, it’s bad news. In Bazalgette’s day, the river was in such a dire state that nothing lived in it; the occasional overflow wasn’t really a problem once the bulk of the sewage had been taken out of the way. But with the 20th century clean-up of the river — since privatisation in 1989 alone, Thames Water has spent £3bn on water treatment works in the Thames Valley above Teddington — the river now supports a lot of marine life, with 125 species of fish. When sewage overflows, it soaks up dissolved oxygen and the fish asphyxiate. And in the tidal Thames, ‘plugs’ of sewage get washed up and down the river; in summer, it can take three months for waste to make its way down river from Teddington to the estuary at Southend. Moreover, Stride explained, it means that the water quality in the estuary is often below the standard stipulated by EU directives.
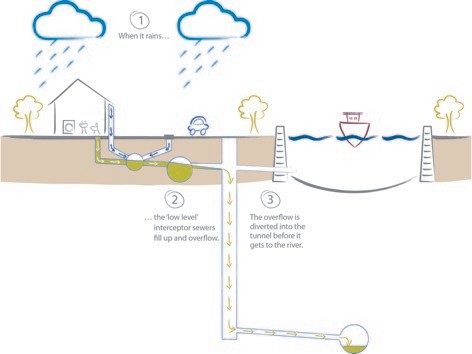
Hence the Thames Tideway Tunnel. At £4.1bn it will be the largest privately funded infrastructure project in Europe, and by far the largest project Thames Water has undertaken since privatisation (the next largest, at £625m, is the Lee Tunnel, which is nearing the end of construction. Connecting Abbey Mills with Beckton, it will prevent overflows from London’s largest combined sewerage outflow (CSO) at Abbey Mills, which is responsible for 40 per cent of the sewage outflow into the river all on its own).
The Tideway Tunnel will run from 35m underground at Acton to 75m at Beckton, a drop of 1m for every 790m. This is enough of a gradient to ensure the tunnel is self-cleaning — the current will sweep solids along with it, preventing faecal matter from festering and conditions becoming septic. It is also below the level of the existing CSO tunnels, and will be connected to them by vertical shafts which will intercept overflows from the shallower Bazalgette sewers and carry them down into the deeper tunnel. Its diameter will vary from 6.2m to 7.5m along its length.
”We’re making a system with a design life of 120–150 years — just like Bazalgette did, we’re designing a long-term solutionPhil Stride, head of Tideway Tunnel project
The tunnel will be accompanied by extensions to five water treatment works, mostly east of London, to handle the increased sewage flows; but the tunnel is by far the most challenging part of the project. Intercepting 34 CSOs, it goes through 14 London boroughs and will require 24 separate construction sites, 21 of which will be large — three drive sites where tunnel-boring machines (TBM) will be launched, two reception sites where the TBMs will be recovered, and 17 sites to intercept the discharge points. Attentive readers will notice that 3+2+17 is 22, not 21 — one of the reception sites is also an intercept point.
Starting in Ealing, the tunnel will meet the Thames at Hounslow and proceed eastward under the river as far as Limehouse, where it will follow the Limehouse Cut canal north-eastwards away from the river to Abbey Mills. The sewage will then flow into the Lea Tunnel to the expanded Beckton treatment works. Even at its narrowest, the tunnel will be big enough to hold three double-decker buses side by side; its total volume will be 1.5 million cubic metres. ‘We go under 43 other tunnels and over two, both of which are coincidentally owned by Thames Water, but we only go under 1,301 buildings, most of which are between Ealing and Hounslow,’ Stride said. ‘However, we need to buy a lot of land because of the construction sites, and liaise with a lot of stakeholders including local residents. It’s a complex project in many ways.’
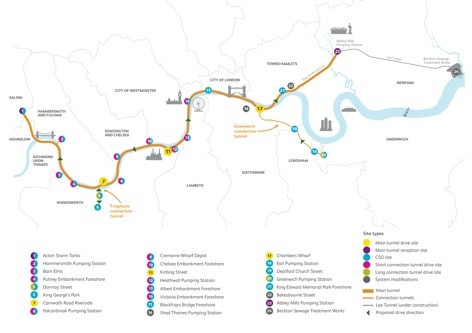
The geology doesn’t help. The tunnel will go through clay in the west, mixed sands and gravels (technically, Lambeth beds and Thanet sands) in the central region and chalk in the east, each of which requiring a different type of TBM. The latter two regions are fissured rock through which water can pass, so at 65m underground the workface will be under 6 bar of water pressure. ‘That affects the type of TBM we use, so the workforce aren’t exposed to those pressures,’ Stride added.
The intercept shafts, especially at the eastern end, are some of the deepest in the world. These shafts are being sunk using advanced diaphragm wall techniques, where the excavation site is surrounded by a concrete wall to prevent water getting in. The wall starts out as a circular trench, which is kept filled with a slurry to stop it from collapsing; the trench is then filled with concrete from the bottom up to displace the slurry. Once the diaphragm wall has set, the material within the circle can be excavated. ‘Maintaining the verticality when you’re lowering concrete panels 70m below the ground is quite a challenge, and we’re proud of the tolerances we’ve achieved,’ Stride said.
The complexities of handling large volumes of liquid moving at speed are another factor in the engineering design. ‘If you take the discharge at Blackfriars Bridge as an example, you’re dropping the order of 50m3 of water per second — that’s 50 tonnes — into a shaft 15m wide and 65m deep. That’s the weight of 36 average cars every second, the height of a 20-storey building. So the key technique is to create a vortex and spin the flow; otherwise you’ll have a huge amount of energy being dissipated at the floor of the shaft. But you can’t create a vortex 15m across. So you build a smaller tube at the edge of the shaft and spin the water into that.’
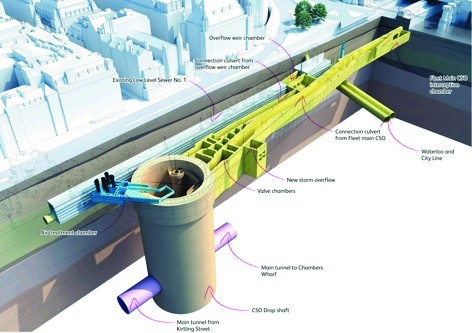
Such a large volume of water has enough momentum to overcome the slope of the main tunnel and flow uphill, so it’s vital to make sure that there’s no air entrained in the water in the tunnel. Stride said: ‘That mass of water can act like a ram and compress any air pockets like a spring, and when that pressurised air expands, it can fire liquid back up shafts, propel manhole covers into the air and even crack road surfaces. So you have air valves on the top of points where water enters the tunnel to release that pressure harmlessly back into the intercept shaft.’
The tunnel has to be ventilated to prevent the sewage from festering, so air blowers will be installed. Even so, the conditions will be aggressive. ‘We have to use high-quality concrete, because if we get septic conditions at any point we will have hydrogen sulphide gas, and that combines with water to make sulphuric acid, which attacks cement. We’re making a system with a design life of 120–150 years — just like Bazalgette did, we’re designing a long-term solution, and that means quality materials.’
The tunnelling techniques used will be similar to those of Crossrail, although it will use much less sprayed concrete tunnel lining, which characterises the building of Crossrail’s stations. Only some of the points where interceptor shafts meet the main tunnel will require sprayed concrete; the rest will use precast slabs emplaced by the TBMs as they bore through the rock.
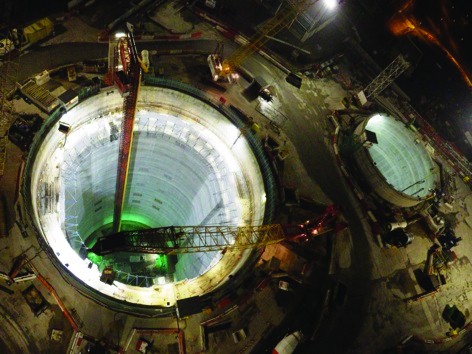
There has been opposition to the Tideway Tunnel, centring around the cost and the disruption that the 24-hour, seven-days-a-week works sites will cause for the decade needed to complete the project. Some opposition groups have called for sustainable urban drainage (SuDS) schemes to be used instead: these involve green roofs that can absorb water and reduce run-off; permeable surfaces that water can soak into; wetlands; and other features to prevent rainwater getting into the sewers. ‘For new build, that’s the right thing to do; it’ll help future-proof the tunnel,’ Stride said. ‘And if we’d been more careful about developing the city; if we’d built rainwater storage into out-of-town car parks, we wouldn’t have the level of problem we have now.’
But implementing SuDS instead of building the tunnel can’t be the answer, he insists. ‘The tunnel will handle 1.5 million cubic metres, even though it should only fill to capacity about seven times per year; it also acts as storage, and we can pump the full capacity out in 48 hours. You’d have to deal with that volume whatever you did, and you’d need an area of parkland 40 times the size of Hyde Park to handle half of it. It’s by no means impossible to dig up all the car parks and resurface them with permeable materials, install water butts for every building, put on green roofs and so on, but we estimate it’d cost £13bn and take 40 years, and cause the most enormous disruption across London. The Tideway Tunnel is the best and most cost-effective way of dealing with the problem in a reasonably short timescale and achieve the water quality the EU demands,’ Stride claimed.
The project plans to put measures in place to reduce disruption. Ventilation pipes, which will ‘exhale’ air as the tunnel fills, will be fitted with activated charcoal granule beds to remove odorous compounds before they reach the air. And the construction sites, which Stride concedes will inevitably cause disruption, will be arranged to minimise this.
Radio wave weapon knocks out drone swarms
Probably. A radio-controlled drone cannot be completely shielded to RF, else you´d lose the ability to control it. The fibre optical cable removes...