The deep-tech company has developed a novel laser-based approach to Nuclear fusion that can produce CO2-free, clean, safe electricity.
Nuclear fusion is seen as a possible visionary solution to the energy problems of the future - clean and comparatively low-risk. Small atomic nuclei are fused at extreme temperatures and pressures instead of being split as in the reactors of conventional nuclear power plants. A similar process takes place in stars and therefore also in the sun. This generates an enormous amount of energy - without releasing CO2. The idea of using nuclear fusion to generate large amounts of energy in a climate-neutral way is considered a dream of mankind. However, nuclear fusion is technically extremely demanding and its realisation requires not only immense investment but also ambitious research and development. Marvel Fusion GmbH, a Munich-based start-up, is pursuing this dream - with the aim of building the first commercially viable nuclear fusion power plant. The deep-tech company has developed a novel laser-based approach that can produce CO2-free, clean, safe electricity. The research for the prototype is entering the decisive phase with the planned construction of a technology demonstrator in Colorado. The world's first customised laser system for research into commercial nuclear fusion is to be built there on the campus of Colorado State University. Meanwhile, basic research is being carried out in Munich and Bucharest. Up to 20 IDS cameras are used simultaneously to monitor and control the experiments in the high-vacuum chambers there.
"The cameras allow us to precisely monitor the experiments for researching and developing laser-based fusion." - Caya Momm, Marvel Fusion.
A pressure range of 10^-4 pascals prevails in the high-vacuum chambers in which the experiments are carried out. This extremely low pressure is far below the atmospheric pressure of around 10^5 and requires special vacuum pumps with pump-down times of up to 8 hours. Efficient execution of the experiments is therefore crucial. "The cameras thus play a crucial role, as they enable us to observe the experiments and control the measuring devices," adds Caya Momm (Purchasing).
The choice fell on a model from the GigE uEye LE camera family. A specially developed protective housing around the cameras ensures that they can withstand the extreme conditions and strong electromagnetic pulses that can occur during fusion experiments. This so-called EMP camera box protects the camera electronics from the high energy discharge. "This design guarantees us optimum functionality and reliability," confirms Kyle Kenney (Lab Engineer).
Alignment of the measuring devices in the vacuum chamber
But what exactly do the cameras see?
During the experiments, some cameras are positioned in such a way that they check the mirror reflections and the alignment of the laser. Further cameras inside the vacuum chamber monitor the arrangement of our superstructure. “This is necessary because we control the motorised assembly in the chamber from the outside. The IDS cameras control measuring devices, detectors, sensors and mirrors," says Kyle Kenney, outlining the use of up to 20 IDS cameras per laser experiment. The main aspects of camera use are correspondingly diverse:
- Alignment of the optics: Cameras ensure the correct positioning of the mirrors.
- Collision avoidance: Overview cameras in the chamber ensure real-time monitoring to avoid collisions with the motorised superstructure.
- Microscopic focus: Another set of cameras focusses precisely on the target of our lasers and thus enables exact laser target acquisition.
- Synchronisation with the laser pulse: The cameras must be synchronised with the laser pulses to ensure accurate and error-free data.
The entire range of tasks is fulfilled by a single camera model: Marvel Fusion opted for the single-board GigE camera UI-5241LE and S-Mount.
"Our space-saving project camera is high-resolution, fast and small enough to solve all these tasks," explains Markus Schickner, Area Sales Manager at IDS. With its compact dimensions of 45 x 45 millimetres, the GigE uEye LE is perfect for customised embedded projects like this one.
It can be precisely integrated into the EMP housing, and the GigE interface also allows cable lengths of up to 100 metres. The camera model is also recommended due to the 1/1.8" CMOS sensor from e2v, which delivers a resolution of 1.3 megapixels (1280 x 1024) at a frame rate of 50 fps. Special features such as triggers for synchronisation with the laser pulse and the price were also decisive factors in the choice of model. This is because the uEye LE is reduced to the essentials and therefore affordable. Nevertheless, the multiple integrated model here is so versatile that different special cameras are not required for different demands. This greatly simplifies the handling of the up to 20 cameras involved in the experiment.
"The cameras are designed to work efficiently in our laser experiments," says Caya Momm, confirming the versatility of the cameras. "They also enable direct and continuous live transmission of the laser experiments. This partially eliminates the need to enter the vacuum chamber," she adds. The safety aspect is ensured by a robust sealing of the camera box, which prevents particles from escaping and effectively safeguards the integrity of the vacuum chamber against contamination.
The captured image information is further processed using the open source software framework Tango Controls, into which the IDS cameras can be quickly and easily integrated via the GigE Vision standard interface. Tango Controls enables the control and monitoring of devices in distributed systems and has been specially developed for scientific facilities and laboratories that require complex device integration and control such as these. The IDS cameras, as well as every other device integrated into the system, can thus be controlled individually via the network.
At the same time, Tango supports event-based communication, allowing real-time reactions and adjustments to the experimental set-up and the vision system as soon as these become necessary during the course of the experiment. The live images supplied by the cameras are immediately processed and delivered with the help of Tango Controls. "The results were very satisfactory, as the position of the laser was localised precisely. Image processing allows us to precisely define or realign the position of the optics with linear drives," reports Oscar Juina (Electrical Engineer).
Checking the laser system
Outlook
"Specially designed cameras with EMP housings of this quality are typically hard to find and very expensive," emphasises Caya Momm, buyer at Marvel Fusion. "The adaptability and availability of the IDS cameras are valuable to us. As we are currently focussing on time-limited research experiments, the quantities required are still small. However, this could change in the future with regard to the planned scaling up to larger fusion experiments and for future fusion power plants." According to the company, the world's most powerful short- pulse laser system is to be built in Colorado by 2026, the first commercial power plants are to be built by the mid-2030s and the company hopes to be able to make a major contribution to the energy supply by 2045.
The advances in laser fusion and its potential as an innovative energy source are of great importance. They have the potential to significantly reduce the carbon footprint of the global energy supply.
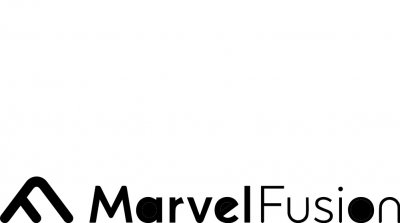
Image rights: Marvel Fusion GmbH
Client
Founded in 2019 and based in Munich, Marvel Fusion is a technology pioneer in the field of safe, clean and reliable energy generation. With the aim of solving one of humanity's biggest problems, the deep tech company is developing an entirely new type of fusion energy technology that dramatically increases the probability of fusion and builds on recent advances in laser and nanoscience.
Camera
uEye LE - the cost-effective, space-saving project camera
Verwendetes Modell: UI-5241LE-MB
Camera family: uEye LE
About IDS Imaging Development Systems GmbH
IDS Imaging Development Systems GmbH is a leading manufacturer of industrial cameras and pioneer in industrial image processing. The owner-managed company develops modular concepts of powerful and versatile USB, GigE and 3D camera as well as models with Artificial Intelligence (AI). The almost unlimited range of applications covers multiple non-industrial and industrial sectors of equipment, plant and mechanical engineering. The AI image processing platform IDS NXT is extremely versatile and opens up new areas of application where classic rule-based image processing reaches its limits. With visionpier, IDS operates an online marketplace that brings together suppliers of ready-made image processing solutions and interested end customers in a targeted manner.
Since its foundation in 1997 as a two-man company, IDS has developed into an independent, ISO and environmentally certified family business with around 350 employees. The headquarters in Obersulm, Germany, is both a development and production site. With branches and representative offices in the USA, Japan, South Korea, the UK, France and the Netherlands, the technology company is also globally represented.
Radio wave weapon knocks out drone swarms
I hope they have assessed how easy it is to shield a drone against the attack. Hopefully the shielding would add too much weight.