This article is aimed at providing an overview of surface finish options for CNC machined metal parts and helping you select the right finishes for your applications.
Just-out-of-CNC machined metal parts naturally have visible tool marks, sharp edges and burrs. Apart from decreasing the aesthetic value, they may also have inaccurate dimensions and tolerances. In order to deliver a properly finished part, surface finish treatments are strongly recommended both in CNC machining. These post processing operations not only improve the strength of the material but also impart anti-corrosive properties and improve surface roughness.
Heat treatments and surface finishes
The two most common post-processing operations used in the CNC machining manufacturing process are heat treatments (annealing, case hardening) and surface treatments (bead blasting, powder coating…). Applying the right surface finishes help improve surface roughness as well as the aesthetic and functional properties of the CNC machined parts.
Heat treatment finishing options for CNC machining
The heat treatment operation improves the physical and mechanical properties of the metal by carefully heating and cooling the metal. The general properties like strength, hardness, ductility, malleability, formability and elasticity can be increased or decreased by this procedure. The operations related to heat treatments are as follows.
Annealing
The annealing process involves the heating of a metal to or near the temperature at which recrystallisation begins without change in the stresses. After heating, the metal should be cooled to room temperature in the oven or put in the sand. This slow cooling of metal increases elasticity in the metal by reducing its hardness, thereby improving the cold working capacity of the metal.
It is generally used for steel alloys, but it can also be used for copper, aluminium and brass.
Tempering
Tempering is a heat treatment method that is mainly dedicated to reducing the amount of hardness of metals. It involves heating the metal to a temperature below the critical point. The temperature is adjusted depending on the amount of hardness that needs to be reduced and it varies depending on the metal type as well.
In general, low temperatures reduce brittleness while keeping most of the hardness intact. Higher temperatures, on the other hand, reduce hardness and increase elasticity and plasticity but reduce some yield and tensile strength.
Gradual heating is recommended to avoid the steel being cracked. The metal is then held at this temperature for a fixed period. Steel alloys are prominently tempered for enhanced properties.
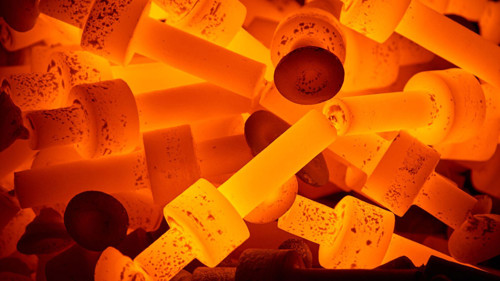
Case hardening
Case-hardening or carburising is a heat treatment process which includes hardening the surface of metal while allowing the metal underneath to remain soft. As the name implies, carburising is inducting carbon or nitrogen into low-carbon alloys at elevated temperatures so that the hardenability increases.
This surface finish can be applied to the part before or after the CNC machining process.
Through hardening
Through hardening differs from case hardening where, instead of just the surface, the whole alloy is made to have relatively similar hardenability. This can be achieved by introducing carbon into the alloy matrix and quenching it repeatedly in brine or in water. Oil quenching can also be used.
CNC surface finish options at Xometry
The operations related to surface finishes are as follows.
Bead blasting
Bead blasting involves spraying a pressurised stream of tiny beads of media, plastic or glass beads, from a nozzle onto the surface of the part. This removes the burrs and imperfections, leaving a smooth finish. In addition, the end product resembles a uniform matte finish.
Bead blasting is done in a closed chamber. Blasting with glass beads is more common for CNC machined parts. Since the surface is matte, it is ideal as a preliminary surface finish treatment for painting and dying. Bead blasting before anodising is also an ideal surface preparation, creating a non-reflective surface.
The recommended part size is 6-600 mm in both height and width. Smaller parts are hard to hold and tough to produce an even surface.
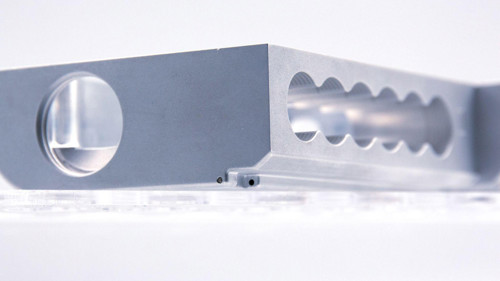
Electroless nickel plating
Electroless nickel or nickel phosphorus plating involves the deposition of an even layer of nickel-phosphorus alloy on the top surface of the solid substrate, like aluminium or steel. The substrate is dipped into a water solution containing nickel salts and phosphorus-reducing agents.
Unlike electroplating, this procedure plates the substrate uniformly while the former suffers from uneven current density and resistance of the substrate.
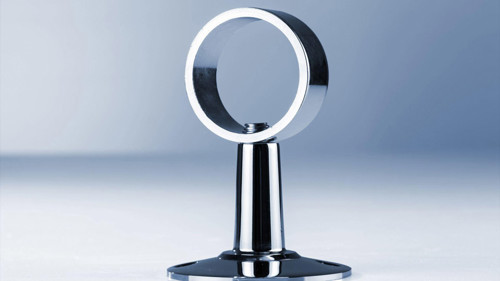
Powder coating
The powder coating process involves free-flowing dry powder which is coated on a substrate. Unlike the normal liquid paint which utilises evaporating solvent, powder coating is applied electrostatically and cured under heat or UV light. The powder can be of thermoplastic or a thermoset polymer.
The finish is usually tougher and even compared to conventional coats. Metals like aluminium and steel can be efficiently coated with polymer powders.
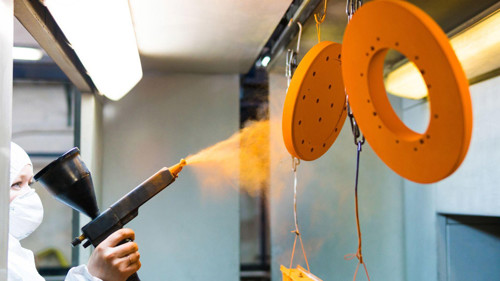
Electropolishing
Electropolishing is the exact opposite of electroplating. In the latter, the substrate is a cathode and the sacrificial anode imparts its ions to the cathode. Here, it is reversed where the substrate is an anode and its ions travel towards the cathode.
In this process, the micro peaks and valleys are levelled out. It is a very good technique for deburring and reducing the average surface roughness.
Passivation
Passivation is a process primarily involving stainless steel which mainly comprises iron, chromium and nickel. The anti-corrosion properties of stainless steel are provided by chromium in the alloy as it naturally produces a layer of chromium oxide on the surface while the free iron facilitates corrosion.
Passivation involves the immersion of stainless steel in an acid bath (e.g. Nitric acid) which dissolves free iron and improves the strength of chromium oxide, thereby countering corrosion.
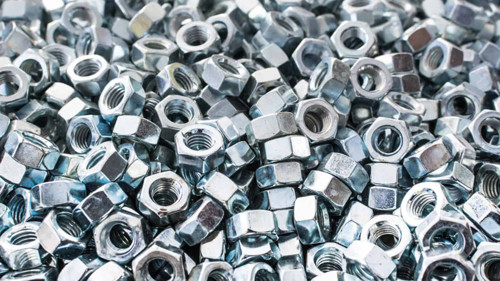
Anodising
Anodising is similar to passivation as it improves the thickness of the oxide layer thereby making the metal surface corrosion resistant. It is highly common for aluminium in CNC machining. It differs from passivation where instead of just dipping in acid, an electrolytic process is involved. Hence it is also called electrolytic passivation.
In anodising, aluminium alloy is dipped in a sulphuric acid electrolyte and used as an anode. When a cathode (inert material like stainless steel, nickel, carbon etc) is placed and electricity is passed, oxygen flows to the anode and reacts forming an anodic oxide. This anodic oxide mostly contains aluminium oxide which protects against corrosion.
The electrolytes are usually:
Anodising also imparts a coarse and grainy surface finish to the metal. It also facilitates the trapping of dye in the oxide layer, thereby giving a near-permanent colour.
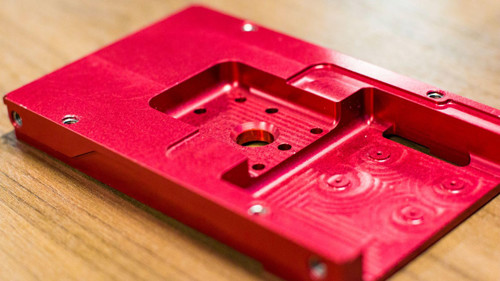
Zinc coating / Galvanising
Galvanising is mainly associated with steel. Also known as hot-dip galvanising is a process of immersing steel in a bath of molten zinc, thereby coating the steel with multiple layers of zinc-iron alloy and zinc metal.
It is because the zinc chemically reacts with ferrous content in the steel and diffuses the coating perpendicular to the surface creating a uniform thick layer along the surface.
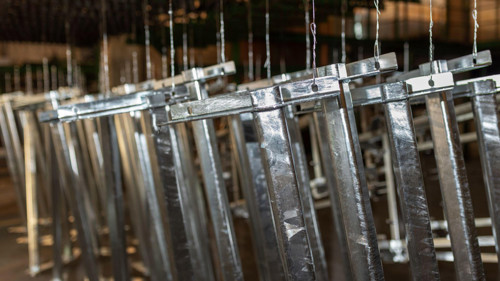
Surface finishes for CNC machining available at Xometry
The table below sums up the various surface finish options you can choose to obtain the desired surface finish and surface texture.
Source CNC machined parts with finishes at Xometry
Surface finish is a very important operation for the CNC machining manufacturing process. Heat treatment improves the overall properties of the metal whereas surface finishes mostly make the metal resist corrosion.
Xometry offers CNC machining services (CNC turning and CNC milling machining processes) throughout Europe and our experienced team is always ready to help you. Upload your files to Xometry Instant Quoting Engine and get a quote in a matter of seconds for your CNC machining projects.
Taking steps toward reindustrialisation
While I agree with Jim and the article that there is much amiss with Britain's manufacturing policy, I think that they are missing the...