Sometimes I feel like Bill Murray in the excellent 90’s film Groundhog Day when asked to debate industry and the ‘skills gap’.
It has been one of the most heated discussions for manufacturers for more than a decade, yet thousands of conversations and promises have yet to come up with a consistent solution that delivers what we all want.
So what do we all want? If you ask management teams at the coalface they’ll say a workforce that has the skills to help them grow and be competitive and training courses/apprenticeships that ensure staff deliver a tangible benefit to the bottom line.
Training providers - on the whole - will agree with this, but they’d also echo the need for Government to provide more support for businesses to take training seriously. An interesting melting pot of wants and desires.
Stripping away all the agendas, I see the answer to the million-pound-question as quite simply…an employer-led approach.
Sounds simple? It can be. However, it needs everyone pulling in the same direction and signing up to give their all to finally bridging the ‘skills gap’. This means training providers being prepared to listen to companies about what they want and how they want it delivered, this means firms being prepared to invest money and time in the bigger picture and it involves all political parties creating the right environment for training to thrive.
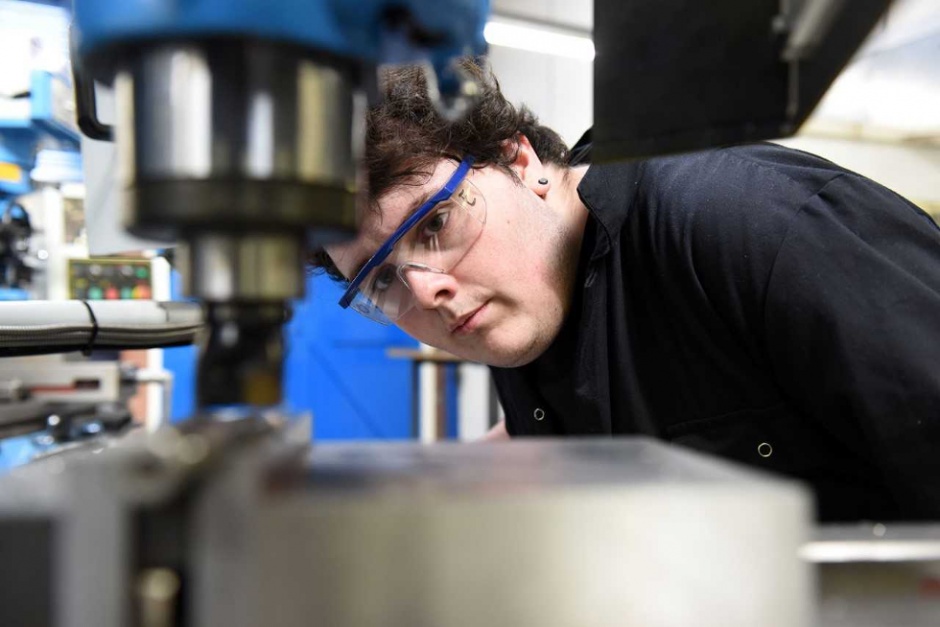
I’m not saying In-Comm Training has nailed it completely yet, but we have adopted this approach and we are seeing some very encouraging results.
The launch of our two Marches Centre of Manufacturing & Technology (MCMT) academies in Bridgnorth and Shrewsbury are great examples. We have teamed up with Classic Motor Cars, Grainger & Worrall and Salop Design and Engineering to create two dedicated learning spaces that are now delivering over 130 trailblazer apprenticeship opportunities for young people in Shropshire.
Every course has been developed in partnership with employers whilst still meeting the national criteria. They get young people that are fully-trained and the engineers of the future get access to £4m of technology, the best industry experts and a guaranteed job at the end of it.
This is an approach we have taken and applied to our headquarters in Aldridge. Here we have engaged with Hyfore to establish an Academy equipped with £3m of CNC machinery, fluid power control, metrology, wire EDM and a new press and tooling line.
We can’t have a supply chain without the right skills
The rapid evolution of industry is another factor that the training sector is having to come to terms with.
A lot of providers have failed to get to grips with the change to the Trailblazer apprenticeship standards and this is holding back delivery of the new qualifications and causing unnecessary confusion within industry.
You’ve also got transitions to quality standards, issues caused by ‘diesel gate’ and the white elephant in every boardroom across the UK and Europe…Brexit.
That little concoction is enough to get any management team looking nervously at its workforce and where it should take its skills training going forward. The clever ones will be making sure their people remain their biggest asset.
We also have a whole raft of new technologies sweeping into engineering and manufacturing. Battery power and vehicle electrification is a major topic in the automotive sector, whilst the use of data and the Internet of Things (IoT) has gone from being buzzwords to being integral parts of the business plan.
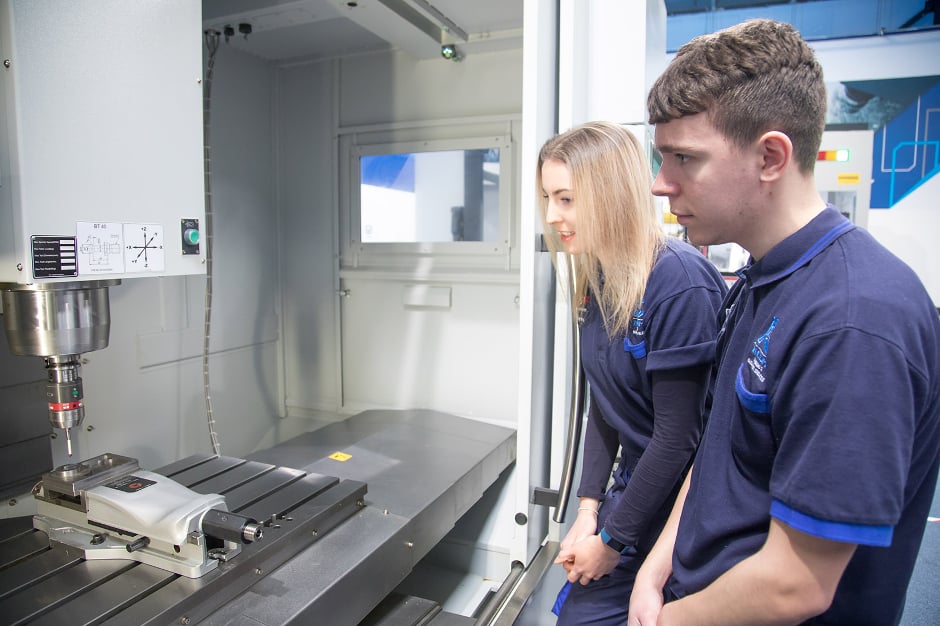
Training has to reflect this. We can’t lead the world in these new technologies if we don’t have the supply chain to support the OEMs and we can’t have a supply chain without the right skills at their disposal.
Our role will be to develop courses that reflect what a future engineer and manufacturing specialist will look like and we’ll need to tap into the knowledge of employers to make this happen.
Going back to the original point, we’re all in this together and the sooner we share best practice and responsibility, the faster we will bridge the ‘skills gap’. We need to engage the disengaged and companies should be actively encouraged to monitor their supply chain and to take up relevant development opportunities.
That’s the long-term vision. In the meantime, let’s all shout about what a great career engineering and manufacturing can be so we can start changing preconceptions and getting young people excited with industry. There’s no time like the present.
McMurtry Spéirling defies gravity using fan downforce
Ground effect fans were banned from competitive motorsport from the end of the 1978 season following the introduction of Gordon Murray's Brabham...