As the world seeks to meet ambitious targets for renewable energy generation, offshore wind turbines of increasing size are being installed in greater numbers. From Dogger Bank in the UK to Greater Changua in Taiwan and the emergence of floating wind, the scale of these developments is increasing at a rapid rate. This presents new challenges not only for installation out at sea, but also how thousands of large, heavy components can be transported, handled and manoeuvred on land.
Think ahead to avoid problems later
First, let’s consider how offshore wind projects are planned, as active involvement of heavy lifting specialists at the FEED stage can often be crucial to finding the smartest and most efficient engineered solutions to a range of logistical problems that might be more time-consuming and expensive to solve later.
Related content
This might include conducting logistical studies or port audits to identify critical factors such as maximum ground bearing pressures, local tides and quay depths at a specific facility. These will also ensure that best equipment is identified to complete the job in hand, and/or how it might be adapted to best fit specific project demands, factoring in any import restrictions that might affect schedule.
With the growth in the number of offshore wind projects, it will become increasingly challenging to find suitable ports capable, not only of providing the space required to store components, but also with sufficient ground strength to withstand lifting and transport operations. This is of particular concern for floating offshore wind projects, whose massive foundations may be as large as 100m in width and weigh up to 16,000t. It also impacts the handling of other components, such as general marshalling activities for jackets, monopiles and transition pieces.
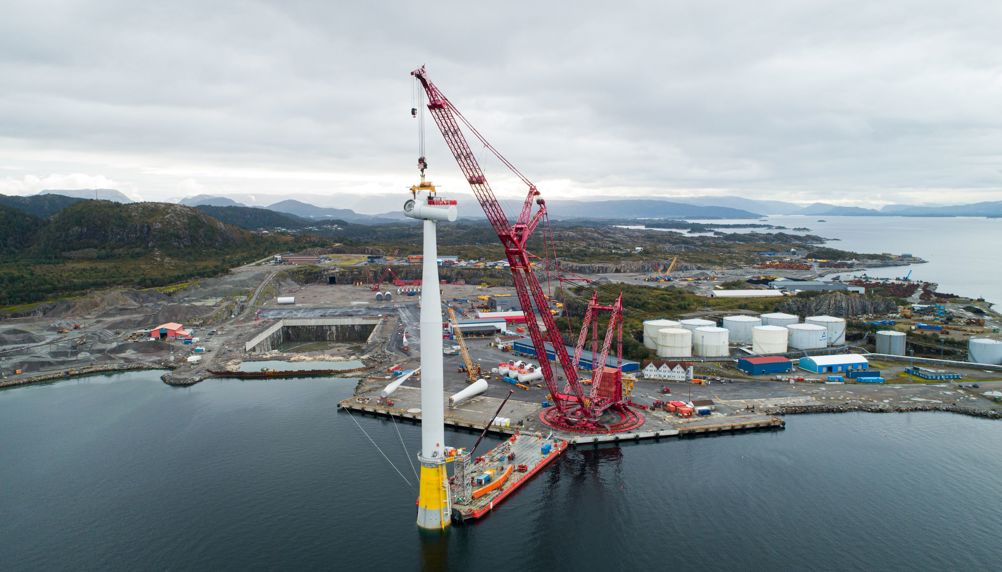
These are issues that are key to efficient execution of the heavy lift package, and so are best considered at the design stage, where techniques and equipment can be adapted to deliver a smarter and more efficient solution.
Cost-effective upgrades
One answer to the predicted shortage of suitable port facilities is to look at upgrading them. However, owners will typically require a reliable pipeline of projects, and a guaranteed prospect of significant returns before they consider investing in the extensive work required. As a result, project-based upgrades that can deliver the required capabilities using operational rather than capital expenditure are likely to be preferred.
A good example of this in action was Mammoet’s work in a joint venture with Giant for the Formosa 1 wind farm in Taiwan, which offered a successful and replicable format for other major offshore projects.
The JV created a marshalling yard at the port of Taichung with the required ground bearing pressure of 10t/m2 to facilitate the handling of large-scale components. Built away from the main port, this new yard was typhoon-protected to mitigate against local weather conditions. Monopiles and transition pieces were transported from Germany to Taiwan and stored using this additional space until they were needed for load-out – avoiding the need for the port to use operational space for less profitable storage.
Floating wind creates new challenges
As more floating wind farms are installed to benefit from higher wind speeds in deeper waters, so the industry must find ways to standardize logistics at commercial scale – ideally avoiding scarce and potentially costly crane vessels. We have seen this first-hand on the Hywind Tampen project, the world’s largest floating wind farm.
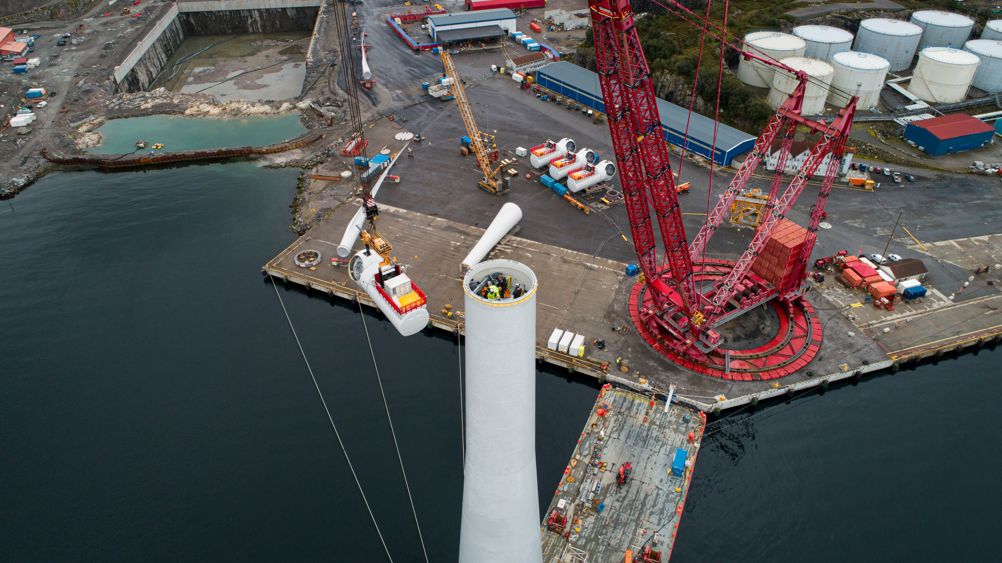
A critical challenge was the work involved in assembling the entire 8.6 MW turbines – including tower sections, nacelles and blades - onto huge 107m floating foundations that lie mainly underwater. A spacer barge was needed to ensure adequate clearance between the base of the foundation and the seabed, which in turn meant that turbine components would need to be lifted from a distance of around 143m.
This demanded a crane with a huge outreach, leading to the use of the PTC200-DS, which has a proven track record for big offshore wind projects such as the Greater Changhua development in Taiwan and Seagreen Offshore Wind Farm in Scotland. The crane was also modified to allow for operation even in strong winds – meaning that there would be fewer potential stoppages due to the weather.
Such challenges will be common as more floating wind projects start, meaning there will be increasing demand for large-scale equipment that handle challenges such as lifting component weights in the thousands of tonnes and doing so over long outreaches.
Adapting to operate efficiently
Although fixed bottom offshore wind is becoming a relatively mature industry in terms of how projects are delivered, the growth in the scale and number of developments means there are still challenges to be overcome. For example, in making sure we have enough suitable ports to meet demand, and how to handle and store XXL foundations without incurring extra civil costs. Furthermore, the rise of floating wind will create an ever-wider range of new logistical problems to solve.
Ultimately, many of the key engineering challenges are focussed on heavy lifting and transportation – making it key that specialists are engaged early in the design stage to develop flexible, efficient methodologies that suit each project’s specific needs.
Remco Zandstra is Commercial Manager at Mammoet
Comment: Hybridisation is a new era for aerospace
Reduced weight & simplification of the combustion engine operating , If hybrid cars are anything to go by. Further weight reduction might be...