It’s clear by now that additive manufacturing (AM) technologies will have huge influence on future manufacturing because they enable mass customisation and the production of complex geometries with reduced material waste.
Despite its transformative potential, additive manufacturing has faced several barriers that have slowed the pace of more widespread adoption. Perhaps the most significant of these factors has been fundamental quality and process repeatability issues. For industrial use, there are inherent complexities to AM technologies that often lead to inconsistencies, deviations and defects in the final printed objects.
But innovation in the world of AM continues, and one such area of invention comes with the development of compensated mesh techniques – a computational approach applied in the preprocessing stage to correct anticipated geometrical deviations using simulated or real-world data – or even both when it comes to the most cutting-edge processes.
The power of prediction: Achieving high dimensional tolerance in AM
Compensated mesh techniques provide a way to anticipate the inconsistencies inherent in AM processes, adjust the design geometry accordingly and thus create a more accurate final product.
Advancements in compensated mesh technologies are fostering AM adoption by reducing errors and increasing the reliability of printed products. It’s a solution that allows for a higher degree of precision in the production of highly demanding applications where even minor inconsistencies can have major consequences. With the use of advanced simulation algorithms in the design phase, the printing process becomes increasingly more accurate and efficient because you can pre-empt as many issues as possible in the digital world before a single part is printed.
For example, in metal additive manufacturing, tools need to be designed to predict and compensate for distortion, compute residual stress and analyse temperature distribution throughout the printing process due to the high energy input of the laser beam. Further processing steps such as heat treatment, cutting, hot isostatic pressing (HIP) and machining processes should be included in the analysis for a holistic view and a reliable result. For metal binder jetting processes, it is necessary to predict changes during the sintering process and compensate for significant shrinkage, while In direct energy deposition, it is critical to analyse the coupled thermal-mechanical response within the process and investigate phase transformations during cooling for a proper end result.

This sort of simulation-based compensation approach is common in larger OEMs and AM bureaus, where the initial mesh of the target geometry is corrected with respect to virtually simulated distortions. This reduces the need for trial-and-error cycles drastically, and alone can lead to production of parts reaching 80-90% tolerance depending on the part design.
AM process improvement : putting quality data to work
When simulation isn’t feasible, or it’s time to scale up production metrology-based compensation comes into its own. This requires the printing of parts followed by real-world measurement of the deviations, typically using a 3D laser or structured light scanner. Here, software advances have again made a huge difference to AM workflow productivity and accessibility. The user can compensate the nominal part geometry based on the measured deviations. This compensation strategy be applied alone when the distortion level of the component is very low.
However, for typical large aerospace and defence components that combine tight dimensional requirements, large build costs and important distortion levels, a hybrid compensation approach is the most efficient and economical solution. Combining the power of simulation-based and scan-based compensation, we have found that manufacturers can quickly attain 98-100% tolerance, where most parts are built “second time right”.
This hybrid approach begins with virtually compensating the initial mesh through simulation followed by building the part in reality. The part is then scanned to measure deviations to fine-tune the simulation-compensated mesh to build a part that is both scan- and simulation-compensated that has close to zero deviations.
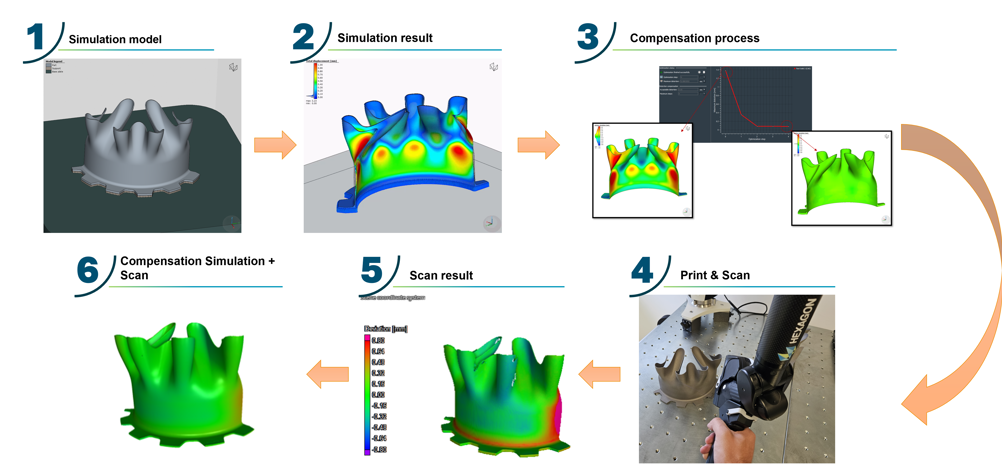
The dimensional accuracy of the final printed part is of course paramount, but the tangential benefits of implementing compensated mesh techniques are also tangible. The minimising of trial-and-error print cycles delivers significant savings in development time and material wastage with both ROI and sustainability benefits, while reduced post-processing and finishing of these green parts offers further time and cost savings.
This requires the teams to connect their people, processes and data across design engineering, production and quality disciplines. But as simulation, measurement technologies and metrology software have matured the insights are now readily available – as are open industry cloud platforms to connect the workflows – making the journey to repeatable additive manufacturing quality achievable for every manufacturer.
McMurtry Spéirling defies gravity using fan downforce
What a fun demonstration. I wonder if they were brave enough to be in the car when it was first turned over. Racing fan cars would be an interesting...