The potential of tidal energy is huge. Seventy per cent of the earth’s surface is ocean and sea and, if we could harness that energy, it would provide 150 per cent of the world’s energy needs.
Related content
A recent report found that tidal stream energy could provide more than 6GW of energy to the UK grid by 2050. This may be small compared to the potential of offshore wind but, in contrast to wave, solar and wind, tidal energy is entirely predictable, so could provide a significant baseline power source for our future electricity grid.
It also has the potential to contribute over £40bn Gross Value Added (GVA) to the UK economy, including tens of thousands of new jobs, primarily in neglected coastal communities.
The UK government has been doing its part: the Contracts for Difference (CfD) Allocation Round 4 will support the deployment of over 40MW of tidal stream energy from 2025-27. A similar pathway has allowed offshore wind to achieve cost reduction and commercial viability: the challenge for tidal stream is to demonstrate a credible cost reduction pathway to enable 100s of MWs to GWs to be installed on 2030-40 timelines.
Harnessing tidal has so far proven difficult and expensive, particularly from an engineering point of view. The sea is a difficult environment for engineering – corrosive, difficult to access, sometimes dangerous, and expensive. Tidal stream turbines are designed to operate for 25 or more years, while fixed on the seabed or attached to a floating platform or vessel.
There has been significant progress in tidal turbine technology in recent years. The largest tidal device currently is the 2MW Orbital Marine Power’s O2 device in Orkney, with the largest array being Meygen in the Pentland Firth (6MW from 4 x 1.5MW devices). These machines have been silently producing more than 50GW/h of electricity over the last few years.
One of the neglected areas of the technology, however, has been the design and testing of tidal turbine blades. These are manufactured from fibre-reinforced polymers - the same materials used to build wind turbine blades. But, compared to wind turbines, tidal blades are much shorter, more like an aircraft wing to design, and there’s a lack of data on how to design and test them, especially in fatigue. This means that tidal blade designers lack the data and the confidence to increase the blade lengths, which limits the turbine power needed to make tidal energy more cost-effective.
All that is about to change. The EU Horizon Europe MAXBlade project, which started in January 2023 – led by TechnipFMC, including Orbital Marine Power, Marasoft, TECNALIA, University of Edinburgh, EMEC, Laborelec and the European Composites Industry Association - plans to increase the length of the largest tidal blade from 10 to 13 metres, resulting in a 70 per cent increase in the area the blade can sweep. The MAXBlade team believes this will have the single biggest effect on bringing down the Levelised Cost of Electricity from tidal energy.
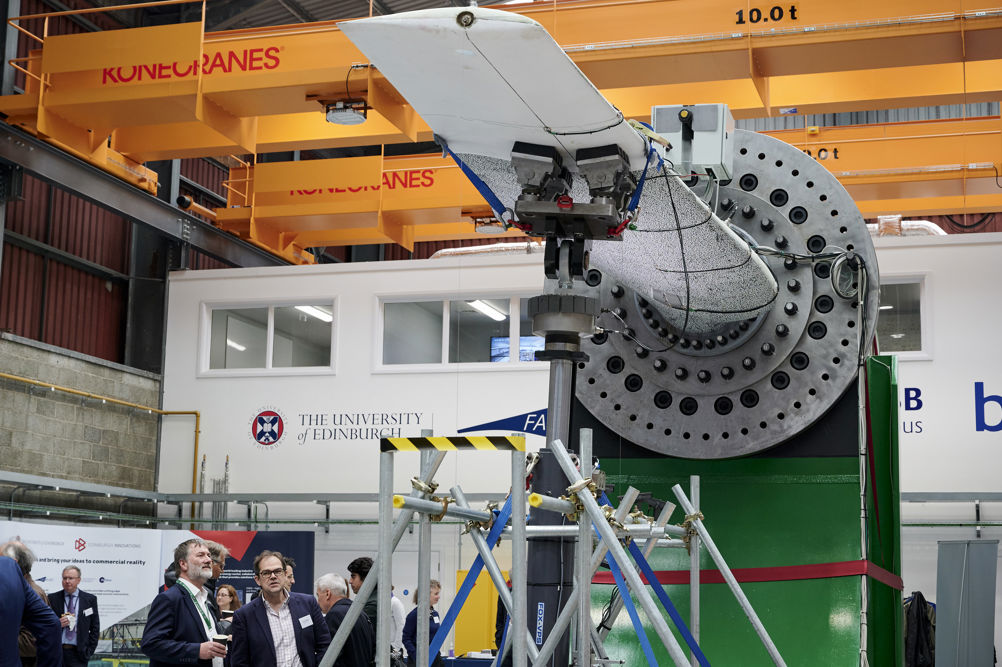
Furthermore, the new blade will be tested on site at the world’s only dedicated tidal blade fatigue testing centre - the University of Edinburgh’s FastBlade facility – at Rosyth in Fife, Scotland, built in partnership with Babcock International Group.
FastBlade uses the regenerative hydraulics system developed by University of Edinburgh spinout Artemis Intelligent Power. The Digital Displacement Hydraulics® system means that energy is stored in the motors of the pumps, rather than wasted in heat, with Artemis winning the MacRobert prize in 2015. This helps to solve the problem of the higher resonant frequency of shorter tidal blades, which has previously made hydraulic testing very expensive.
The team is well positioned. From Salter’s Duck - the first commercial wave energy device – to our FloWave wave and tidal test tank, the University of Edinburgh’s School of Engineering has long been a locus of expertise in marine renewables, now working with the best in the industry.
We also bring expertise in materials and aim to make tidal blades more sustainable than the current epoxy resin of wind turbine blades. MAXBlade will develop routes for composite blade material recycling at the end of life through novel in-situ polymerised thermoplastic composites.
Lastly, MAXBlade is part of the Arrol Gibb Innovation Campus at Rosyth which, as well as being open for the business of large-scale manufacturing, is also upskilling local people to play a full part in the economy of the future.
MAXBlade is part of a world-leading wave of opportunity for Scotland and the UK in the design, manufacture and even export of tidal energy technology. You can read more about the project here.
Prof Conchúr Ó Brádaigh is Head of School and Chair of Materials Engineering at the University of Edinburgh
Water Sector Talent Exodus Could Cripple The Sector
Maybe if things are essential for the running of a country and we want to pay a fair price we should be running these utilities on a not for profit...