Industry forecasts for the total value of the global construction industry predict it will rise by 85 per cent to $15.5 trillion by 2030*. Despite this rosy outlook, construction firms are currently being impacted by several megatrends, each of which presents major challenges for the industry.
First, existing labour shortages – both skilled and unskilled - look set to get much worse. In research carried out for ABB in 2021, 9 out of 10 construction businesses predicted a skills crisis by 2030.
Second, the pressure to improve sustainability and support a circular economy will mean overhauling every aspect of the construction process, as well as producing buildings that are much more energy efficient throughout their lifetimes.
Third, people are increasingly looking for housing solutions that can be easily customised to meet their needs, in much the same way as vehicles and many consumer goods already are. This has only really been possible in individual, high-end projects before now, but mass customisation is the goal.
Most construction businesses already recognise that robotic automation will play a key role in meeting all these challenges. More than 80 per cent of them say they are looking to introduce or increase their use of robotics and automation in the next ten years. Robots are expected to make a growing contribution in a range of areas, such as the fabrication of modular homes and building components offsite, for example, as well as robotic welding and materials handling onsite.
Transformative technology
The widespread deployment of robotic 3D printing technology promises to be especially game-changing. It’s relatively early days, but robots have already been used to 3D print buildings in concrete on site, including a two-story admin building in Dubai and Europe’s first legally habitable 3D-printed house in the Netherlands.
3D concrete printing enables complex shapes to be produced in situ. It reduces energy consumption compared to conventional manufacturing - in which materials and /or structures must be prefabricated – as well as reducing waste. In addition to typically being faster and cheaper, 3D printing offers more freedom in terms of shape and form and makes it easier to incorporate functional elements into the overall structure from the start. This added freedom means that buildings can often be made stronger without the need to increase structural density, reducing the total amount of material and the weight in the final structure.
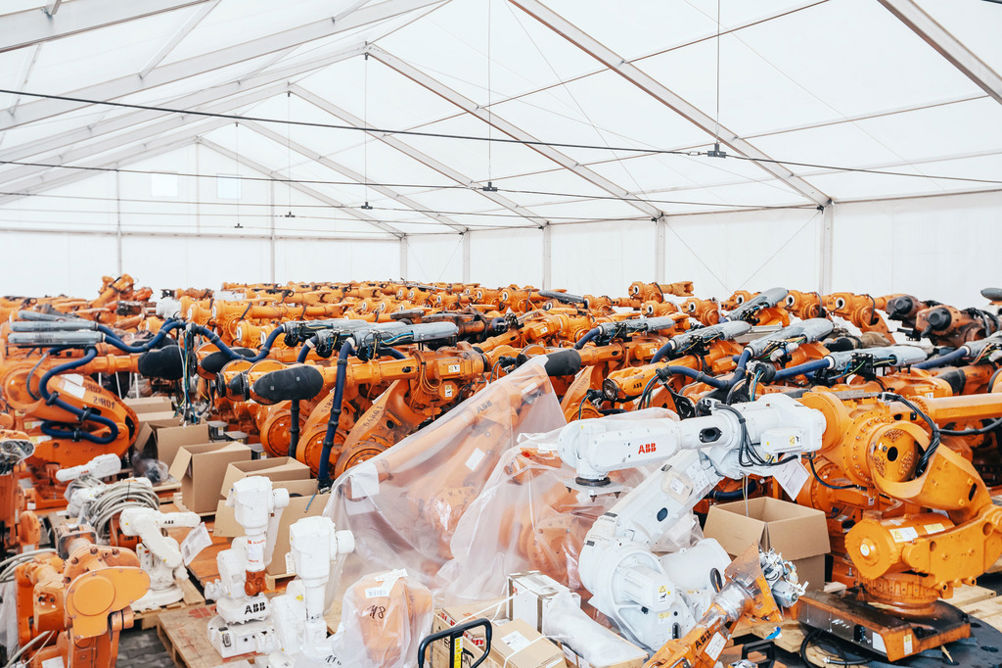
Looking beyond standard concrete, 3D printing can also increase circularity and sustainability by reusing potentially harmful or environmentally unfriendly by-products from other industries as building materials. Fly ash and slag from the coal and steel industries, glass and plastic are all possible candidates. Where recycled glass is available, for instance, it can be used as a substitute for construction sand in cement mixes.
Taken together, the sustainability advantages of 3D printing and the wider improvements in health and safety that robotic automation typically delivers will enhance the reputation of construction companies as responsible actors and good employers.
Demonstrating design excellence
Even before construction begins, 3D printing can already be useful at the design stage, where architects rely on proof-of-concept models to demonstrate the viability and effectiveness of different shapes, surfaces and facades before moving to full construction. This ability to demonstrate alternative methods of design and construction is proving to be a major asset for architectural practices when advocating new approaches to building companies. For example, Zaha Hadid Architects (ZHA) is globally renowned for designing large-scale, curvaceous masterpieces and the firm has embraced the use of 3D printing to help translate its ideas into physical structures.
Building robust solutions
While the importance of using robots off-site as part of a modular construction approach should not be underestimated, the full potential of 3D robotic printing will only be realised if robots can be reliably deployed onsite. Compared to the consistent and controllable environments that can be achieved in offsite manufacturing facilities, building sites present a number of challenges for the design and application of robots. These include rough, uneven surfaces, as well as obstacles and moving hazards in the form of people and other machinery. Even the weather poses a potential risk.
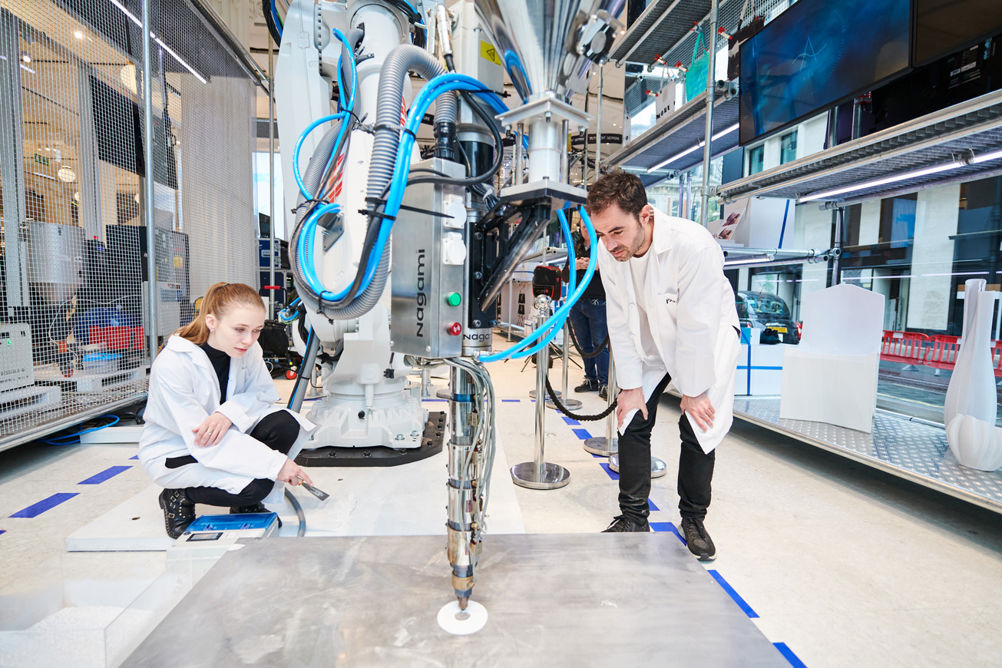
To counter this, robot manufacturers, research institutions and specialist systems integrators are all working together to develop robust solutions using features such as all-terrain caterpillar tracks, collaborative laser scanners and other technologies that will promote the safe, reliable deployment of robots more widely on building sites.
As the need to embrace robotic automation becomes greater, it will provide growing incentives to find new solutions and drive greater innovation throughout the construction industry.
For more information about how robotic automation is transforming the construction industry, visit https://new.abb.com/products/robotics/industries/transforming-the-future-of-construction.
*The Global Construction 2030 report (link)
Julian Ware is UK & Ireland Sales Manager for ABB Robotics
McMurtry Spéirling defies gravity using fan downforce
Ground effect fans were banned from competitive motorsport from the end of the 1978 season following the introduction of Gordon Murray's Brabham...