According to the team, it has established a low-cost and scalable carbon ink formulation capable of unlocking the potential for perovskite solar cells to be manufactured at scale.
Using slot die coating in a roll-to-roll (R2R) process, academics from the university’s SPECIFIC Innovation and Knowledge Centre have established a way to create ‘fully printable’ perovskite photovoltaics (PV), a term the team say is ‘often used but, until now, incorrect’.
Researchers searched for an alternative to the gold electrode that is typically applied using an expensive and slow evaporation process after the device has been printed.
Dr David Beynon, senior research officer at SPECIFIC, said: "The key was identifying the right solvent mix, one which dries as a film without dissolving the underlying layer.
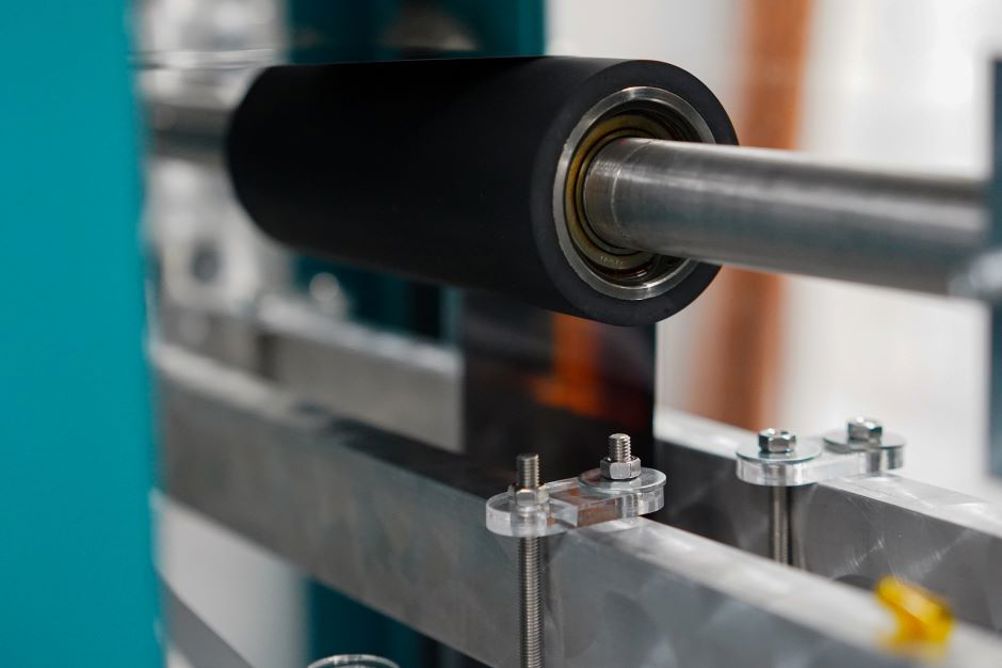
"X-ray diffraction analysis showed carbon electrode ink is capable of this when formulated with an orthogonal solvent system.
"This innovative layer can be applied continuously and compatibly with the underlying layers at a low temperature and high speed."
Photovoltaic research lead, Professor Trystan Watson, said that perovskite solar cells show great promise in the drive towards cleaner energy.
“The ability to produce a fully working device entirely in-line makes high-volume manufacturing easier and more economical and is a big step towards their commercialisation,” Watson commented.
Related content
“It unlocks the idea of a manufacturing process where a solar ink is added one end and a solar cell emerges from the other."
The devices with carbon electrodes provided a similar photovoltaic performance to the conventional evaporated gold electrodes, the team said, as part of a small-scale device on a rigid glass substrate with power conversion efficiencies (PCE) of 13-14 per cent and the additional benefits of outperforming at higher temperatures and having better long-term stability.
They confirmed that the new fully R2R coated device, which was printed onto a 20-metre-long flexible substrate, produced a stabilised power conversion efficiency of 10.8 per cent.
The method, published in Advanced Materials, has been designed and made, analysed in detail and improved by the team over four years. It has been funded by the Welsh government’s European Regional Development Fund and the Engineering and Physical Sciences Research Council (EPSRC) through SPECIFIC and the Application Targeted and Integrated Photovoltaics (ATIP) Programme Grant.
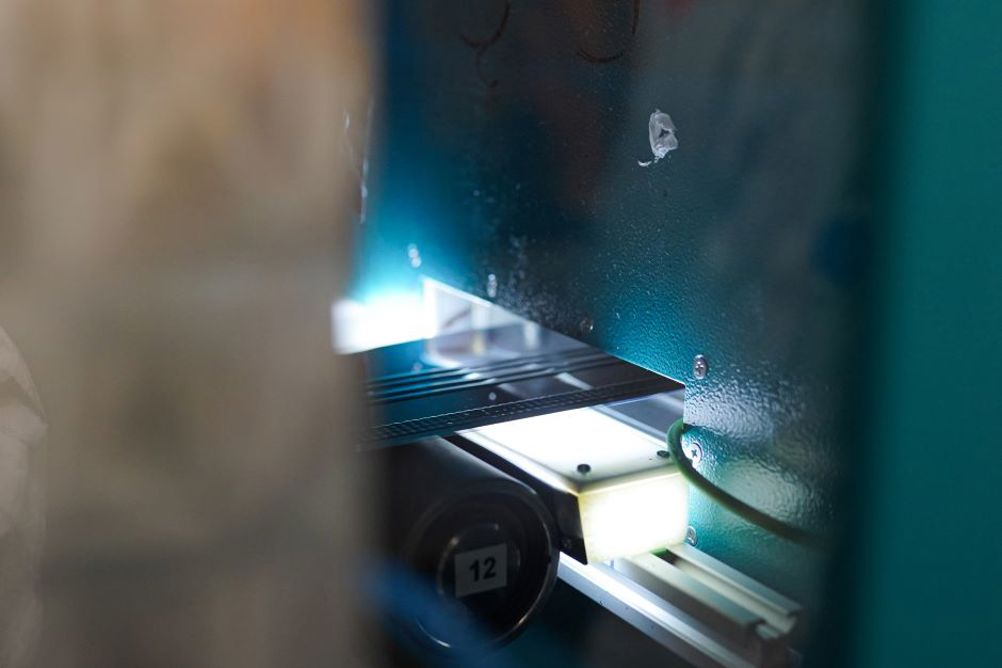
Professor Watson said the next challenge is to prove the method, adding that the team needs to work on making something that ‘really looks like a solar panel’.
“We can then install them on buildings and understand how close we are to delivering on the promise of UK based manufacturing of green renewables,” Watson said.
Guest blog: exploring opportunities for hydrogen combustion engines
"We wouldn't need to pillage the environment for the rare metals for batteries, magnets, or catalisers". Batteries don't use rare...