Using machine learning and visual recognition, the robot can be taught to make assembly decisions based on the components put in front of it.
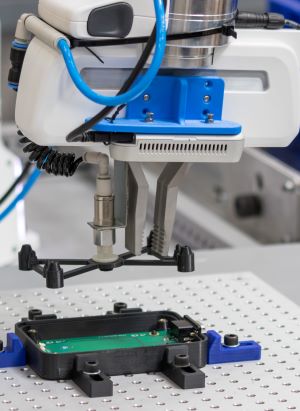
A demonstrator developed at Coventry-based MTC mimics a typical electronic assembly using multiple components and can show manufacturers how robotics can be used to create a low cost, reactive assembly system.
Most industrial automation technology is programmed to do a specific job and changing the process can require major investment in fixturing and reprogramming. The MTC system is trained to recognise components and assembly variables and find solutions in its database. According to MTC, it combines a robot operating system with a collaborative robot and low-cost vision sensors.
In a statement, MTC senior research engineer Mark Robson said, "Giving robots the decision-making capability of a human operator can dramatically improve their productivity and flexibility in variable conditions. Our demonstrator project shows how machine learning can be applied to achieve this.
Robotic hand gets to grips with assembly line jobs
"This work has shown that deep learning-based vision can provide robots with a robust ability to find and work with objects. The MTC has demonstrated methods to overcome the challenges in translating this ability into the physical domain of robotics which will enable the use of other machine-learning algorithms in industrial solutions."
In trials the MTC's system is said to have returned a 99 per cent successful detection rate and demonstrated that it was possible to swap the input tray and change the component mix with little effect on performance.
The MTC's chief automation officer, Mike Wilson, said, "We now have a blueprint for developing and implementing intelligent vision systems to industrial problems in an effective way, opening up potential applications in human-robot collaboration. We have eliminated the need for part fixtures as this system can adapt to new layouts without reprogramming. Completely traceable decision-making allows errors to be addressed quickly and effectively, and the system can be trained to apply to any new assembly process."
McMurtry Spéirling defies gravity using fan downforce
What a fun demonstration. I wonder if they were brave enough to be in the car when it was first turned over. Racing fan cars would be an interesting...