Maximising CO2 emissions reduction from hybrid-electric aircraft
Study looks at best combinations of fossil fuel and battery propulsion, and life-cycle analysis, to optimise environmental benefit
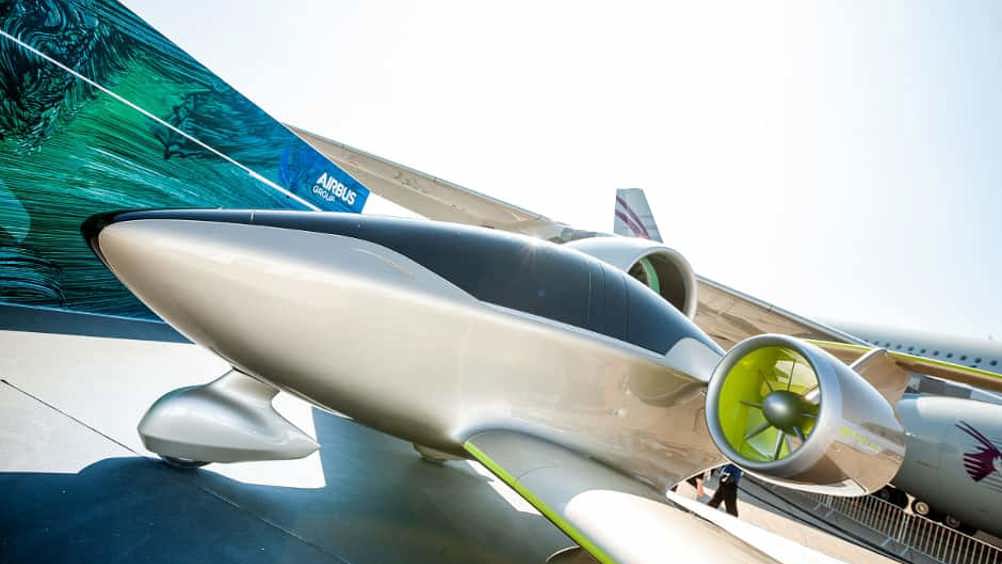
The benefits of hybrid power trains are hotly debated, not least within The Engineer's comment section. While electric propulsion obviously cuts emissions of propulsion systems in use – that is to say on the road for hybrid vehicles and in the sky for aircraft – the emissions associated with battery charging might or might not outweigh these benefits, depending on who you ask.
While most attention has focused on land vehicles, because the technology exists and is commercially viable today, development of hybrid fossil fuel and electrically-powered aircraft is continuing rapidly even though no commercial hybrid yet exists. With the energy demands of flight so much greater than those of ground transport, the question of whether there is any environmental benefit is even more difficult to answer.
Aerospace engineers from the University of Illinois have attempted to investigate the matter, and their results appear in a paper in the Journal of Aircraft. According to co-author Philip Ansell, the aspect of the subject that has not been studied is the carbon impact associated with recharging the batteries. "You can get a fuel burn reduction, but if the cleanliness of the electrical grid that's being used to charge the battery system is not included, you're missing a significant part of the carbon emissions total," he said.
Register now to continue reading
Thanks for visiting The Engineer. You’ve now reached your monthly limit of news stories. Register for free to unlock unlimited access to all of our news coverage, as well as premium content including opinion, in-depth features and special reports.
Benefits of registering
-
In-depth insights and coverage of key emerging trends
-
Unrestricted access to special reports throughout the year
-
Daily technology news delivered straight to your inbox
Water Sector Talent Exodus Could Cripple The Sector
Maybe if things are essential for the running of a country and we want to pay a fair price we should be running these utilities on a not for profit...