The project, in which the EPSRC is funding the UK’s involvement, is expected to push the boundaries of knowledge of the behaviour of liquid metals.
Liquid metal cooled reactors have been investigated for marine propulsion, but not for power generation, and have not been produced commercially.
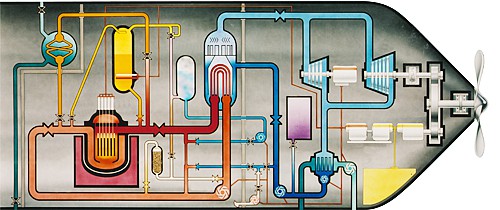
Their advantages are the excellent heat transfer properties of liquid metals, which allows the reactor core to be more compact. Liquid metals can be heated to temperatures of hundreds of degrees centigrade without the need for pressurisation as in a water reactor, which makes them safer to operate. The higher operating temperature boosts the overall thermodynamic efficiency of the plant.
Dr Andrea Cioncolini, associate professor of thermal hydraulics in the university’s Mechanical, Aerospace and Civil Engineering department, said liquid metal cooled reactors would be smaller and simpler to make, so that numerous small reactors could be built instead of large bespoke units. Small modular reactors could have long-life prefabricated cores that could run for several years before being replaced.
The alternatives for UK nuclear
Small nuclear reactor researchers eye up alternatives to traditional technology
However, little is known about the behaviour of liquid lead and in particular the erosion and corrosion of materials exposed to it at high temperatures. Investigation is made more difficult by the fact that lead is not transparent.
The test set up will consist of a cylindrical vessel of about 15l capacity, which will have test samples arranged around the wall. It will be filled with liquid lead and a variable speed impeller in the centre will generate a flow of the metal at up to 700oC, causing erosion.
Corrosion products could build up on the samples, or in stronger flows they could be removed and deposited elsewhere. “Ideally you want to produce as little corrosion as possible, and then you want to know where it will be deposited,” Cioncolini said.
Manchester’s role, starting in January, will be to undertake computational fluid dynamics simulations, first to inform the design of the apparatus and then to help interpret and analyse the results.
Cioncolini said that because of the difficulty of taking measurements in liquid lead, the experimental measurements would too “coarse” to gain a full understanding, “so the CFD provides additional details on the flow development and the thermal field that you cannot measure directly.”
The other partners in the project are Pittsburgh University, which will build and run the experimental facility; Argonne National Laboratory, which has developed ultrasound techniques to “see” through liquid metals; Los Alamos National Laboratory and ENEA, the Italian national agency for new technologies, which both have experience in operating test rigs with liquid lead. Westinghouse Electric is the industry partner and US involvement is funded by the US Department of Energy.
Radio wave weapon knocks out drone swarms
Probably. A radio-controlled drone cannot be completely shielded to RF, else you´d lose the ability to control it. The fibre optical cable removes...