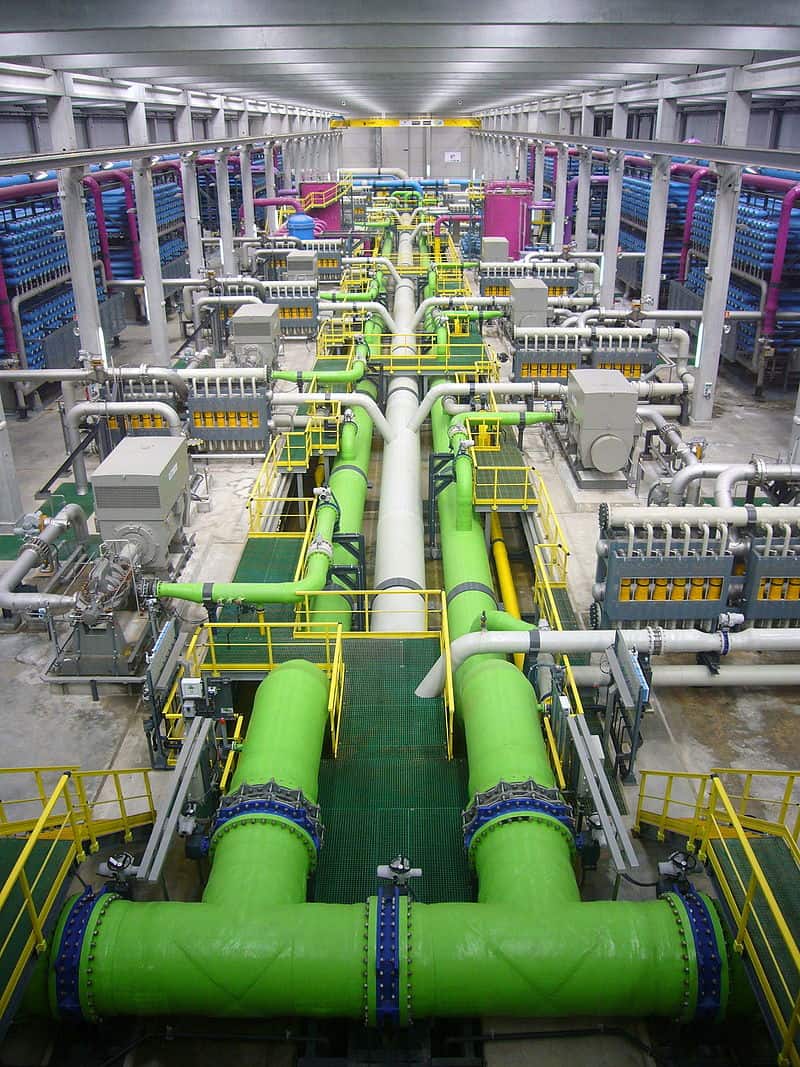
More efficient separation technologies, such as in the reverse osmosis process that makes seawater drinkable, could be the result of introducing 3-D printing into membrane manufacture, according to researchers from the University of Bath.
Although membranes may not immediately spring to mind as industrially important, the separation processes that they enable are estimated to account for 40 to 70% of all industry capital and operating costs.
Moreover, they are key to separation and purification of industrial gases, fine chemicals and as indicated above, fresh water: these processes account for some 15% of all energy used globally. Improving membrane efficiency could therefore have a very large effect on carbon emissions and the efficiency of energy usage.
Darrell Patterson and colleagues from the Department of Chemical Engineering at Bath looked at the possibilities of 3-D printing for making tailored membranes; although Patterson admits that currently, the costs are too high to produce large-scale quantities of membranes to compete with current methods, he was interested to see what the possibilities and challenges of technology might be.
In a paper in the Journal of Membrane Science, Patterson explained that current technologies such as phase inversion and sintering can only make membranes that are flat or tubular/hollow fibre, which limits their precision in certain applications. Using 3-D printing, however, would bring new design freedom that would not only be able to make membranes of different shapes and geometries, it would also allow "unprecedented control over membrane architecture" at the level of the shape, arrangement and geometry of the membrane pores. "
"Additionally, almost uniquely it allows both the micro- and macro-structure of the membrane to be designed and fabricated in one go, allowing membrane module fabrication to be controlled in a single machine/process from membrane material through to membrane module, giving the unprecedented combined and integrated design possibilities for improving both the membrane separation at both the materials and process architecture levels,” he added.
In the water industry, for example, membranes with pores and surface shapes that enhance micro-mixing and shear flow across the surface could help to prevent the membrane from becoming clogged, a problem which leads to downtime and usage of energy to clean equipment. The paper looked at a variety of different 3-D printing processes currently in use or development for industrial applications including photopolymerisation of liquids and solid deposition processes using powders, extrusion and lamination.
McMurtry Spéirling defies gravity using fan downforce
Ground effect fans were banned from competitive motorsport from the end of the 1978 season following the introduction of Gordon Murray's Brabham...