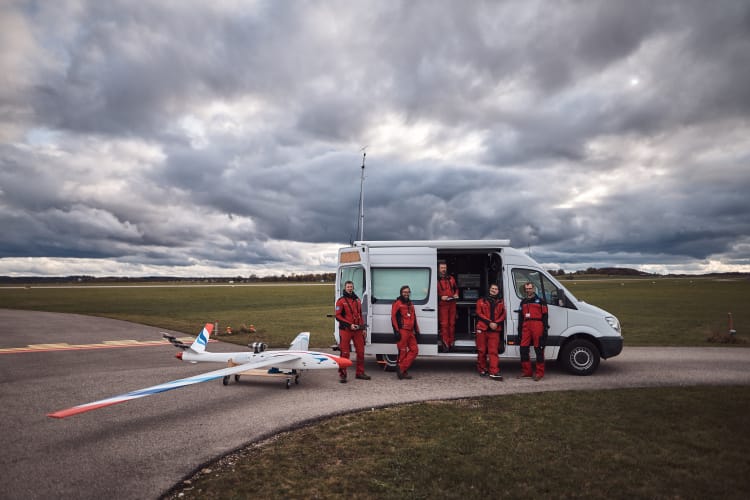
Researchers from the Technological University of Munich (TUM) and the German Aerospace Centre, DLR, led the test flights from an airfield in Oberpfaffenhofen. The tests involved two aircraft, both equipped with wings which are wider in span and lighter than conventional wings. The researchers believe that such wings could make aircraft more fuel-efficient, therefore reducing cost and carbon dioxide emissions.
A European project known as FLEXOP (flutter-free flight envelope expansion for economical performance improvement) aims to develop wider and lighter wings which are not affected by the aerodynamic phenomenon known as flutter.
Anybody who has flown in a commercial aircraft will be familiar with this: it’s the up-and-down motion of the tips of the wings relative to the aircraft fuselage in flight, and it is caused by aerodynamic drag and wind gusts, and it reduces the fuel efficiency of aircraft. Lighter weight wings tend to be more affected by flutter, but would reduce fuel usage. One solution to flutter is to develop aeroelastic wings, which are -seemingly paradoxically - capable of more movement in flight than conventional, more rigid, wing constructions.
______________________________________________________________________
Further reading
- New 3D bat wing model could inspire next generation aircraft
- The evolution of the aircraft wing
- The wing master: Bombardier’s award-winning aerodynamic production
______________________________________________________________________
One of the two test aircraft had a seven-metre wingspan and used carbon fibre in the wing construction. The fibres were aligned so that if the wing was bent by the force of the air, it would also twist to minimise the force upon it. The other wing takes a different approach. When flutter occurs, the outermost flaps of the wing control surfaces are deployed to act as dampers. "The integrated active flap controls developed at DLR significantly increase the possibilities for a much lighter design," says Gertjan Looye from the DLR Institute of System Dynamics and Control in Oberpfaffenhofen. A third wing design in the project, developed by the Computer and Automation Research Institute of the Hungarian Academy of Sciences (MTA SZTAKI), is to be tested at a later date because of its complexity.
Such wings could save 7 per cent of fuel on a typical flight, or enable aircraft to carry 20 per cent more freight for the same amount of fuel as a current aircraft, the researchers claim. The team also plans to test aeroelastic wings for passenger aircraft. The project’s commercial partner is Airbus, and academic partners include Bristol University.
Breaking the 15MW Barrier with Next-Gen Wind Turbines
An 820 ft diameter windmill has a circumference of just over half a mile. Thus at 10 RPM, the tip speed is 310 mph. I presume this acts as a speed...