Eurocopter demonstrates emergency electric motor
Eurocopter has incorporated an electric motor into one of its AS350 helicopters to demonstrate the system as an emergency auxiliary power source.
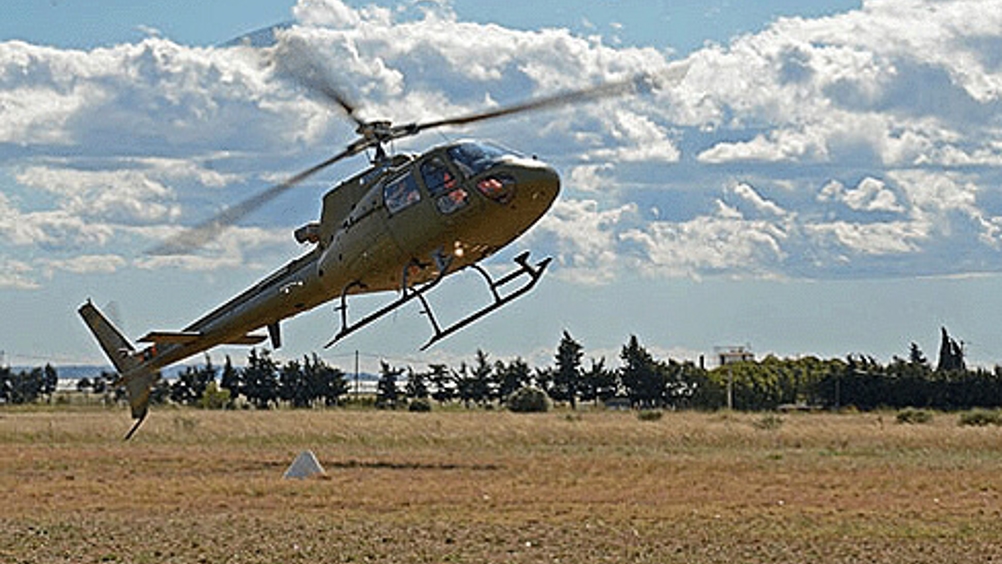
The centrally placed electric motor activates during an auto-rotation landing, which is performed by helicopter pilots in the event of a failure in the main turbo shaft engine.
In such an event, the electric motor, which is powered by a lithium-ion polymer battery, provides power to the rotor, allowing a pilot to control the helicopter during a descent.
‘The electric back-up system aims at easing the pilot’s work and reducing stress. I believe it will lead to even less fatalities, as well as less damages to the helicopter in case of engine failure in flight,’ said Jean-Michel Billig, Eurocopter’s executive vice-president of R&D.
‘It is all about improving safety by reducing the pilot’s stress and workload during an auto-rotation manoeuvre.
‘Integrating a system that included an engine, a converter and a battery into a helicopter, which already had a very complex system in terms of physical and technological characteristics, was very challenging,’ added Billig.
Register now to continue reading
Thanks for visiting The Engineer. You’ve now reached your monthly limit of news stories. Register for free to unlock unlimited access to all of our news coverage, as well as premium content including opinion, in-depth features and special reports.
Benefits of registering
-
In-depth insights and coverage of key emerging trends
-
Unrestricted access to special reports throughout the year
-
Daily technology news delivered straight to your inbox
Water Sector Talent Exodus Could Cripple The Sector
Maybe if things are essential for the running of a country and we want to pay a fair price we should be running these utilities on a not for profit...