The shape of 3D printed engineering components is often compared to bones, especially those of birds. Researchers from Purdue University have found that the internal structure of bone could also give an important clue to how to make additively-produced structures including buildings longer lasting.
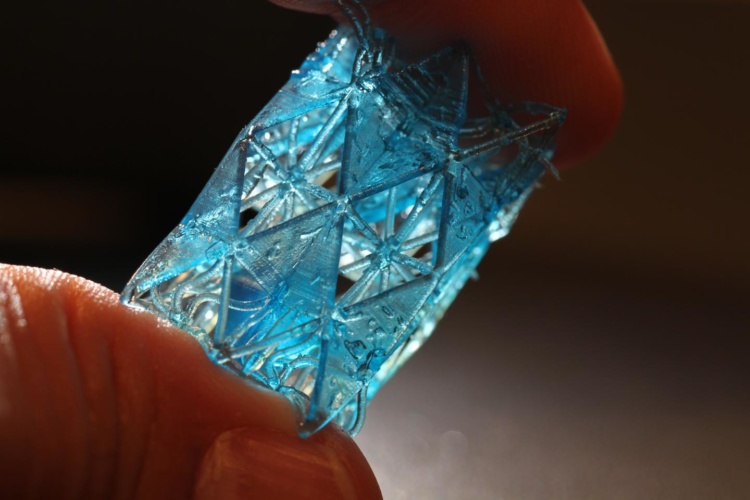
Purdue University photo/Pablo Zavattieri
Bones, like buildings, are supported by beams and struts. A spongy structure called trabeculae forms an interconnected network of vertical plate-like columns and horizontal rod-like struts which add stability to the material from the inside. The denser the trabeculae, the more resilient the bone. Disease and age can reduce the density.
_____________________________________________________________________
Related reading
- Engineering a response to Nepalese earthquakes
- Beetle inspired 3D printed cement could lead to disaster proof buildings
- Home comforts: MIT team develops system to 3D print buildings
_____________________________________________________________________
In a paper in the Proceedings of the National Academy of Sciences, Pablo Zavatierri of Purdue’s Lyles School of Civil Engineering, who worked with colleagues from Cornell and Case Western Universities, reports that it is the horizontal struts which increase the fatigue life of the bone, while the seemingly more substantial columns contribute more to strength and stiffness. Fatigue life is crucial to the longevity of the structure, as Christopher Hernandez, a member of the team from Cornell, explained: "When people age, they lose these horizontal struts first, increasing the likelihood that the bone will break from multiple cyclic loads.”
Improving fatigue resilience is important to the design of 3D-printed buildings, which have to withstand repeated vibration and the effects of natural disasters such as earthquakes. Zavatierri’s lab has been designing 3D-printed polymers with internal architectures similar to trabeculae. "When we ran simulations of the bone microstructure under cyclic loading, we were able to see that the strains would get concentrated in these horizontal struts, and by increasing the thickness of these horizontal struts, we were able to mitigate some of the observed strains," said Adwait Trikanad, a co-author on this work and civil engineering PhD student at Purdue. Thickening the strut structures did not significantly increase the weight of the polymer, the team added.
"Bone is a building. It has these columns that carry most of the load and beams connecting the columns. We can learn from these materials to create more robust 3D-printed materials for buildings and other structures," said Zavattieri.
The researchers believe that applying this discovery to the internal structure of printed cement, as used in printed buildings which are quicker to build than conventional structures, could increase their resilience and lifetime without needing to increase the overall amount of material used in the building. "When something is lightweight, we can use less of it," Zavattieri said. "To create a stronger material without making it heavier would mean 3D-printed structures could be built in place and then transported. These insights on human bone could be an enabler for bringing more architected materials into the construction industry."
See more in this video:
IET sounds warning on AI doll trend
I agree that we need to reduce cooling water demand for servers. And yes, generative AI consumes a large amount. But what about BitCoins? Their...