Automatic gear
At Automatica 2006, production and automation professionals can find out how the latest developments in the field of 'co-operating robots' can maximise effficiency.
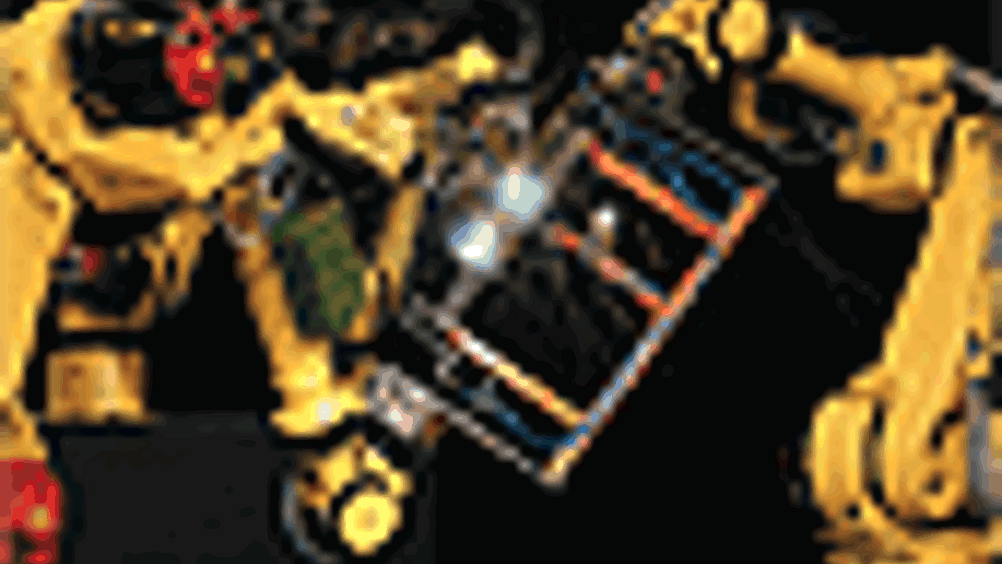
Multi-robot systems provide the manufacturing industry with great flexibility, and the leading manufacturers have a range of solutions on offer.
At
, being held in Munich from 16-19 May, production and automation professionals can find out all about the latest developments in the field of 'co-operating robots' — those linked to work in synchrony — from companies such as ABB Motoman and Fanuc.
Manufacturers have developed many software and control functions for this concept. Multi-robot systems are the focus of much interest, because flexibility in terms of working hours and production processes is essential for the manufacturing industry. Such systems bring additional benefits to a range of sectors, because co-operating robots working together not only complete a task faster, but can also be used singly for other functions.
multiple robot systems are nothing new, having operated efficiently in a range of situations from small assembly cells to large spot welding production lines in the automotive sector for 35 years. What is new is the use of intelligent control to reduce tooling costs, cut set-up times and minimise time-to-market.
Register now to continue reading
Thanks for visiting The Engineer. You’ve now reached your monthly limit of news stories. Register for free to unlock unlimited access to all of our news coverage, as well as premium content including opinion, in-depth features and special reports.
Benefits of registering
-
In-depth insights and coverage of key emerging trends
-
Unrestricted access to special reports throughout the year
-
Daily technology news delivered straight to your inbox
Water Sector Talent Exodus Could Cripple The Sector
Maybe if things are essential for the running of a country and we want to pay a fair price we should be running these utilities on a not for profit...