The material was developed by scientists from Sandia National Laboratories, in collaboration with Ames National Laboratory, Iowa State University and Bruker Corp. Consisting of 42 per cent aluminium, 25 per cent titanium, 13 per cent niobium, 8 per cent zirconium, 8 per cent molybdenum and 4 per cent tantalum, the multi-principal element alloy (MPEA) was found to be stronger at 800°C than many other high-performance alloys, including those currently used in turbines. These properties would enable turbines to operate at greater efficiency, generating more electricity and releasing less waste heat.
Related content
According to the researchers, density functional theory calculations revealed a thermodynamic explanation for the observed temperature-independent hardness, with the Laser Engineered Net Shaping additive manufacturing process also believed to be a factor. The work is published in Applied Materials Today.
“We’re showing that this material can access previously unobtainable combinations of high strength, low weight and high-temperature resiliency,” said Sandia National Laboratories scientist Andrew Kustas. “We think part of the reason we achieved this is because of the additive manufacturing approach.”
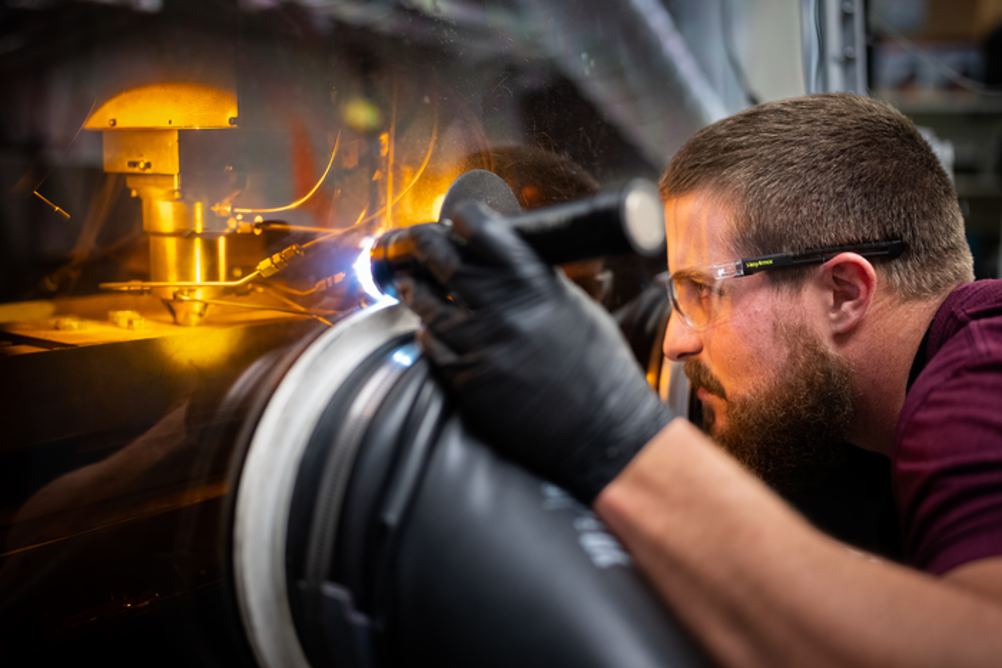
Power plant turbines are not the only potential application for the new alloy. According to Ames Lab scientist Nic Argibay, the researchers are partnering with industry to explore how alloys like this could be used in the automotive industry, while aerospace is another potential target.
“Electronic structure theory led by Ames Lab was able to provide an understanding of the atomic origins of these useful properties, and we are now in the process of optimising this new class of alloys to address manufacturing and scalability challenges,” Argibay said.
The team is also interested in exploring whether advanced computer modelling techniques could help researchers discover other potential high-performance, additively manufactured superalloys.
“These are extremely complex mixtures,” said Sandia scientist Michael Chandross, an expert in atomic-scale computer modelling who was not directly involved in the study. “All these metals interact at the microscopic — even the atomic — level, and it’s those interactions that really determine how strong a metal is, how malleable it is, what its melting point will be and so forth. Our model takes a lot of the guesswork out of metallurgy because it can calculate all that and enable us to predict the performance of a new material before we fabricate it.”
Radio wave weapon knocks out drone swarms
Probably. A radio-controlled drone cannot be completely shielded to RF, else you´d lose the ability to control it. The fibre optical cable removes...