History teaches that the Industrial Revolution began in England in the mid-18th century. While that era of sooty foundries and mills is long past, manufacturing remains essential — and challenging. One promising way to meet modern industrial challenges is by using additive manufacturing (AM) processes, such as powder bed fusion and other emerging techniques. To fulfill its promise of rapid, precise and customisable production, AM demands more than just a retooling of factory equipment; it also calls for new approaches to factory operation and management.
That is why Britain’s Manufacturing Technology Centre (MTC) has enhanced its in-house metal powder bed fusion AM facility with a simulation model and app to help factory staff make informed decisions about its operation. The app, built using the Application Builder in the COMSOL Multiphysics® software, shows the potential for pairing a full-scale AM factory with a so-called “digital twin” of itself.
"The model helps predict how heat and humidity inside a powder bed fusion factory may affect product quality and worker safety," says Adam Holloway, a technology manager within the MTC's modelling team. "When combined with data feeds from our facility, the app helps us integrate predictive modelling into day-to-day decision-making." The MTC project demonstrates the benefits of placing simulation directly into the hands of today's industrial workforce and shows how simulation could help shape the future of manufacturing.
Additive Manufacturing for Aerospace with DRAMA
To help modern British factories keep pace with the world, the MTC promotes high-value manufacturing throughout the United Kingdom. The MTC is based in the historic English industrial city of Coventry (Figure 1), but its focus is solely on the future. That is why the team has committed significant human and technical resources to its National Centre for Additive Manufacturing (NCAM).
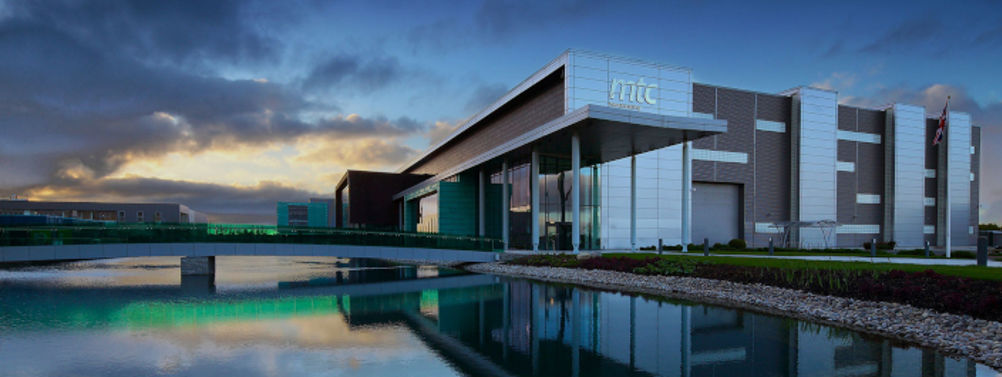
“Adopting AM is not just about installing new equipment. Our clients are also seeking help with implementing the digital infrastructure that supports AM factory operations,” says Holloway. “Along with enterprise software and data connectivity, we’re exploring how to embed simulation within their systems as well.”
The NCAM's Digital Reconfigurable Additive Manufacturing for Aerospace (DRAMA) project provides a valuable venue for this exploration. Developed in concert with numerous manufacturers, the DRAMA initiative includes the new powder bed fusion AM facility mentioned previously. With that mini factory as DRAMA’s stage, Holloway and his fellow simulation specialists play important roles in making its production of AM aerospace components a success.
Making Soft Material Add Up to Solid Objects
What makes a manufacturing process “additive”, and why are so many industries exploring AM methods? In the broadest sense, an additive process is one where objects are created by adding material layer by layer, rather than removing it or molding it. A reductive or subtractive process for producing a part may, for example, begin with a solid block of metal that is then cut, drilled and ground into shape. An additive method for making the same part, by contrast, begins with empty space! Loose or soft material is then added to that space (under carefully controlled conditions) until it forms the desired shape. That pliable material must then be solidified into a durable finished part.
Different materials demand different methods for generating and solidifying additive forms. For example, common 3D printers sold to consumers produce objects by unspooling warm, plastic filament, which bonds to itself and becomes harder as it cools. By contrast, the metal powder bed fusion process begins with, as its name suggests, a powdered metal which is then melted by applied heat and re-solidified when it cools. A part produced via the metal powder bed fusion process can be seen in Figure 2.
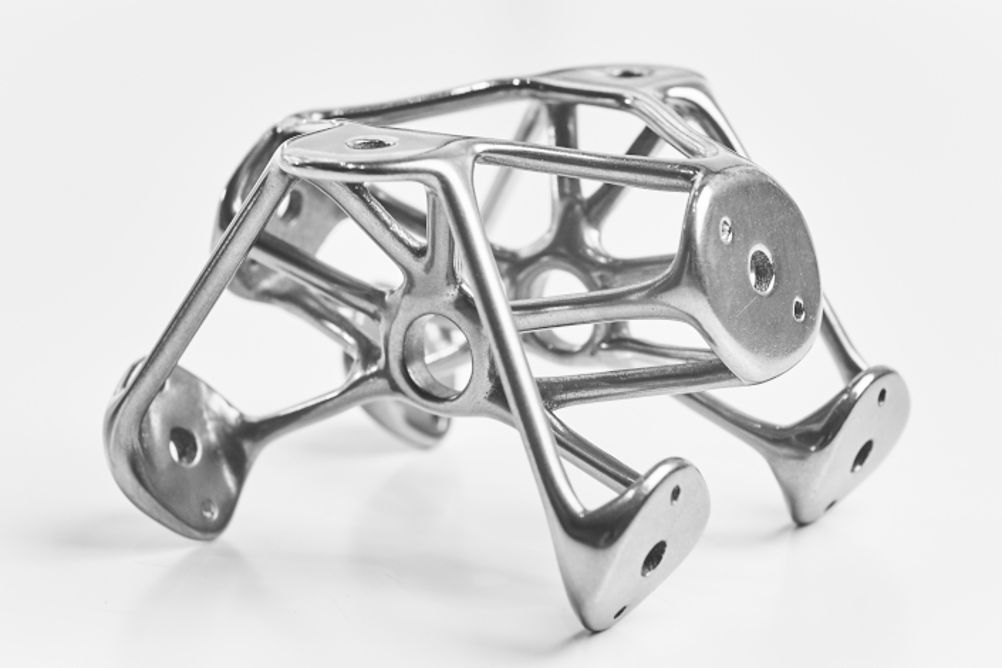
How Heat and Humidity Affect Metal Powder Bed Fusion
“The market opportunities for AM methods have been understood for a long time, but there have been many obstacles to large-scale adoption,” Holloway says. “Some of these obstacles can be overcome during the design phase of products and AM facilities. Other issues, such as the impact of environmental conditions on AM production, must be addressed while the facility is operating.”
For instance, maintaining careful control of heat and humidity is an essential task for the DRAMA team. “The metal powder used for the powder bed fusion process (Figure 3) is highly sensitive to external conditions," says Holloway. "This means it can begin to oxidize and pick up ambient moisture even while it sits in storage, and those processes will continue as it moves through the facility. Exposure to heat and moisture will change how it flows, how it melts, how it picks up an electric charge and how it solidifies,” he says. “All of these factors can affect the resulting quality of the parts you’re producing.”
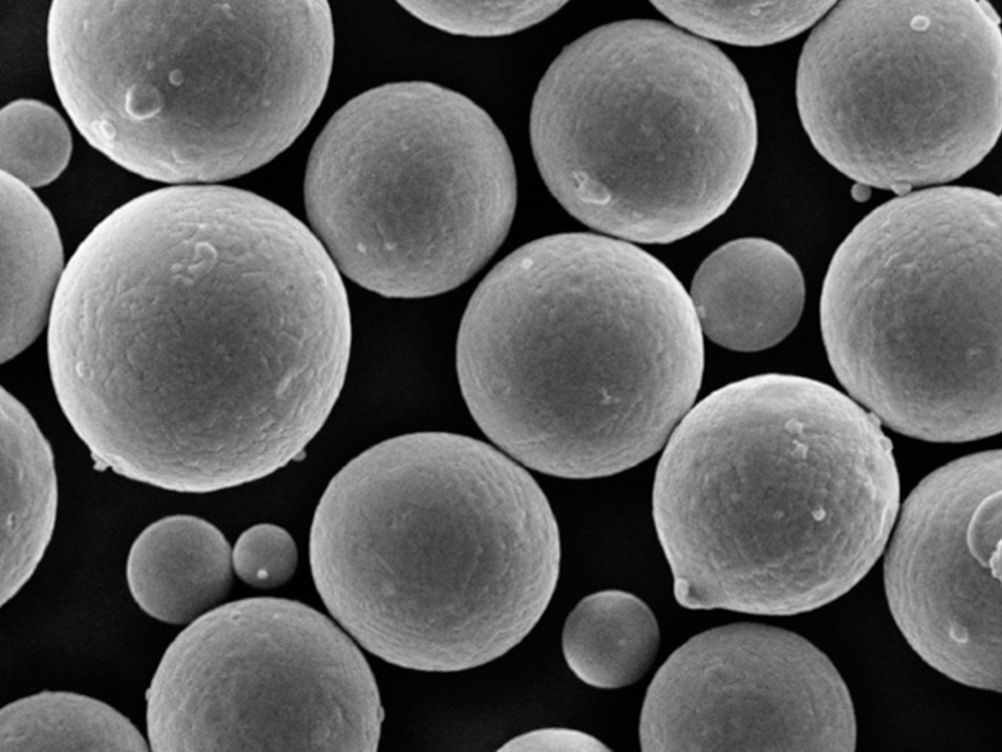
Careless handling of powdered metal is not just a threat to product quality. It can threaten the health and safety of workers as well. “The metal powder used for AM processes is flammable and toxic, and as it dries out, it becomes even more flammable,” Holloway says. “We need to continuously measure and manage humidity levels, as well as how loose powder propagates throughout the facility.”
To maintain proper atmospheric conditions, a manufacturer could augment its factory's ventilation with a full climate control system, but that could be prohibitively expensive. The NCAM estimated that it would cost nearly half a million English pounds to add climate control to its relatively modest facility. But what if they could adequately manage heat and humidity without adding such a complicated system?
Responsive Process Management with Multiphysics Modelling
Perhaps using multiphysics simulation for careful process management could provide a cost-effective alternative. “As part of the DRAMA program, we created a model of our facility using the computational fluid dynamics (CFD) capabilities of the COMSOL® software. Our model (Figure 4) uses the finite element method to solve partial differential equations describing heat transfer and fluid flow across the air domain in our facility,” says Holloway. “This enabled us to study how environmental conditions would be affected by multiple variables, from the weather outside, to the number of machines operating, to the way machines were positioned inside the shop. A model that accounts for those variables helps factory staff adjust ventilation and production schedules to optimise conditions,” he explains.
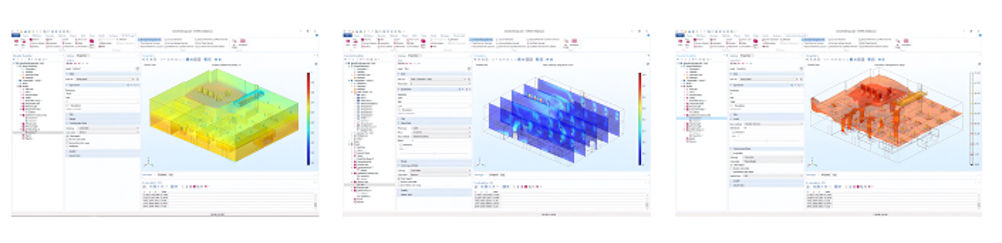
A Simulation App that Empowers Factory Staff
The DRAMA team made their model more accessible by building a simulation app of it with the Application Builder in COMSOL Multiphysics (Figure 5). “We’re trying to present the findings of some very complex calculations in a simple-to-understand way," Holloway explains. "By creating an app from our model, we can empower staff to run predictive simulations on laptops during their daily shifts."

The app user can define relevant boundary conditions for the beginning of a factory shift and then make ongoing adjustments. Over the course of a shift, heat and humidity levels will inevitably fluctuate. Perhaps factory staff should alter the production schedule to maintain part quality, or maybe they just need to open doors and windows to improve ventilation. Users can change settings in the app to test the possible effects of actions like these.
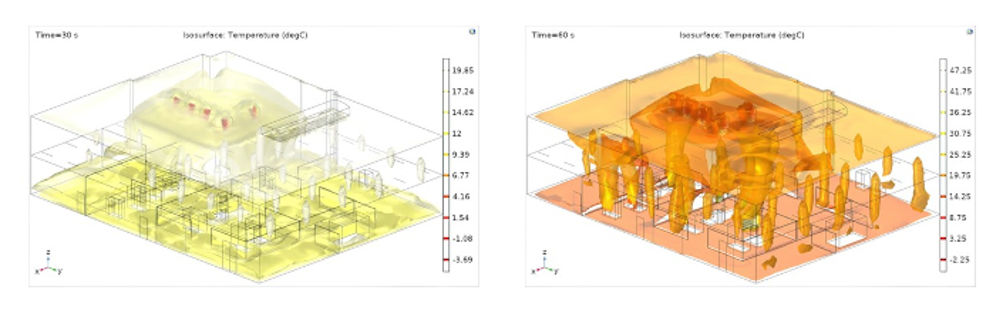
For example, Figure 6 presents isothermal surface plots that show the effect that opening the AM machines’ build chambers has on air temperature, while Figure 7 shows how airflow is affected by opening the facility doors.
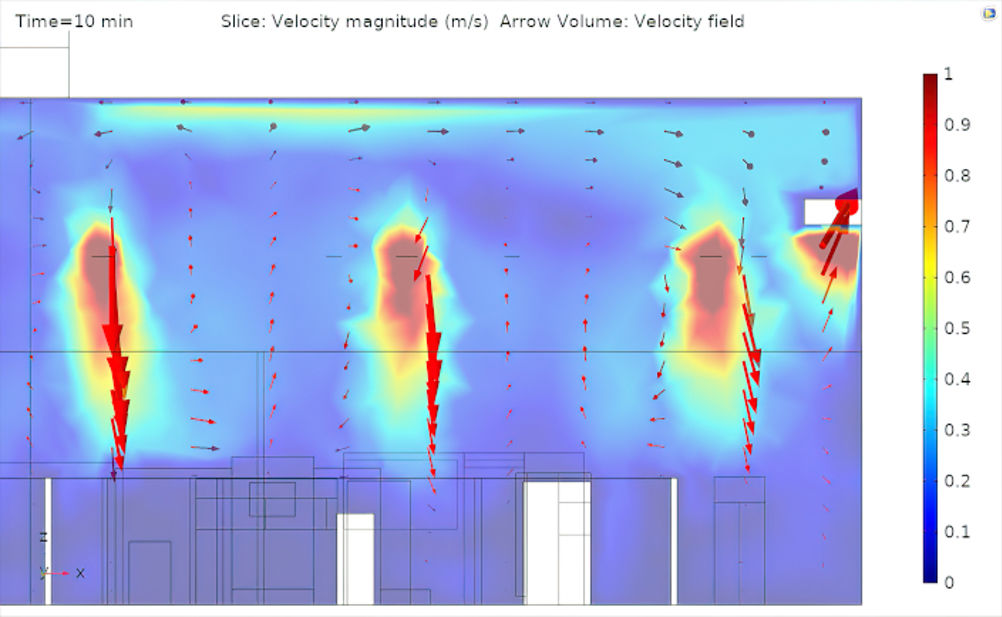
A Step Toward a “Factory-Level Digital Twin”
While the current app is an important step forward, it does still require workers to manually input relevant data. Looking ahead, the DRAMA team envisions something more integral, and therefore, more powerful: a “digital twin” for its AM facility. A digital twin, as described by Ed Fontes in a 2019 post on the COMSOL Blog is “a dynamic, continuously updated representation of a real physical product, device, or process.” It is important to note that even the most detailed model of a system is not necessarily its digital twin.
“To make our factory environment model a digital twin, we'd first provide it with ongoing live data from the actual factory," Holloway explains. "Once our factory model was running in the background, it could adjust its forecasts in response to its data feeds and suggesting specific actions based on those forecasts.”
“We want to integrate our predictive model into a feedback loop that includes the actual factory and its staff. The goal is to have a holistic system that responds to current factory conditions, uses simulation to make predictions about future conditions and seamlessly makes self-optimising adjustments based on those predictions," Holloway says. "Then we could truly say we've built a digital twin for our factory.”
Simulation at Work on the Factory Floor
As an intermediate step toward building a full factory-level digital twin, the DRAMA simulation app has already proven its worth. "Our manufacturing partners may already see how modelling can help with planning an AM facility but not really understand how it can help with operation," Holloway says. "We're showing the value of enabling a line worker to open up the app, enter in a few readings or import sensor data and then quickly get a meaningful forecast of how a batch of powder will behave that day.”
Beyond its practical insights for manufacturers, the overall project may offer a broader lesson as well: By pairing its production line with a dynamic simulation model, the DRAMA project has made the entire operation safer, more productive and more efficient. The DRAMA team has achieved this by deploying the model where it can do the most good — into the hands of the people working on the factory floor.
McMurtry Spéirling defies gravity using fan downforce
Ground effect fans were banned from competitive motorsport from the end of the 1978 season following the introduction of Gordon Murray's Brabham...