The automotive industry is currently undergoing one of the biggest overhauls in its history. Not since the Ford Model T and the dawn of mass production has such a shift been felt, with electrification compelling manufacturers to rethink vehicle architectures, supply chains and plant operations. But the sector’s rapid evolution has inevitably brought challenges, not least around the testing requirements for the avalanche of new vehicles coming to market.
Thankfully, a concurrent and equally rapid transformation has been happening in digital engineering. Advances in design software, digital twins and simulation have seen increasing volumes of work transferred to the virtual realm, where lines of code can be tweaked and tested ad infinitum before physical products are manifested. Where though, you may ask, does this gospel of digitalisation leave the driver? In the haze of ones and zeros, how can carmakers ensure that driver experience remains holy?
At its UK HQ in Nuneaton, HORIBA MIRA believes it has found the answer. The company has invested over £4m in its Driving Simulator Centre, a facility designed to speed up testing, reduce development costs and, crucially, maintain the vital link between automotive design and driver experience.
“We have this attribute-led approach,” Tom Lee, HORIBA MIRA senior manager, Vehicle Attributes, told The Engineer in Nuneaton.
“So that’s really developing a vehicle that the end user wants to drive…we want to ensure that as we develop these vehicles, we’re doing it with that end user in mind and developing a vehicle around their needs.”
In years gone by, the heavy lifting of vehicle development would take place on MIRA’s famous proving ground, a sprawling network of circuits and surfaces set across the 850 acres of its Warwickshire technology park. Comprised of 25 different segments to test all aspects of vehicle performance, a trip around the entire proving ground would cover more than 100km.
Speaking with engineers at MIRA, it’s clear that the proving ground is very much still the epicentre of operations, as well as a point of pride for the company. But digitalisation has presented a new opportunity, epitomised by MIRA’s shift towards more front-end engineering to complement its physical testing capabilities.
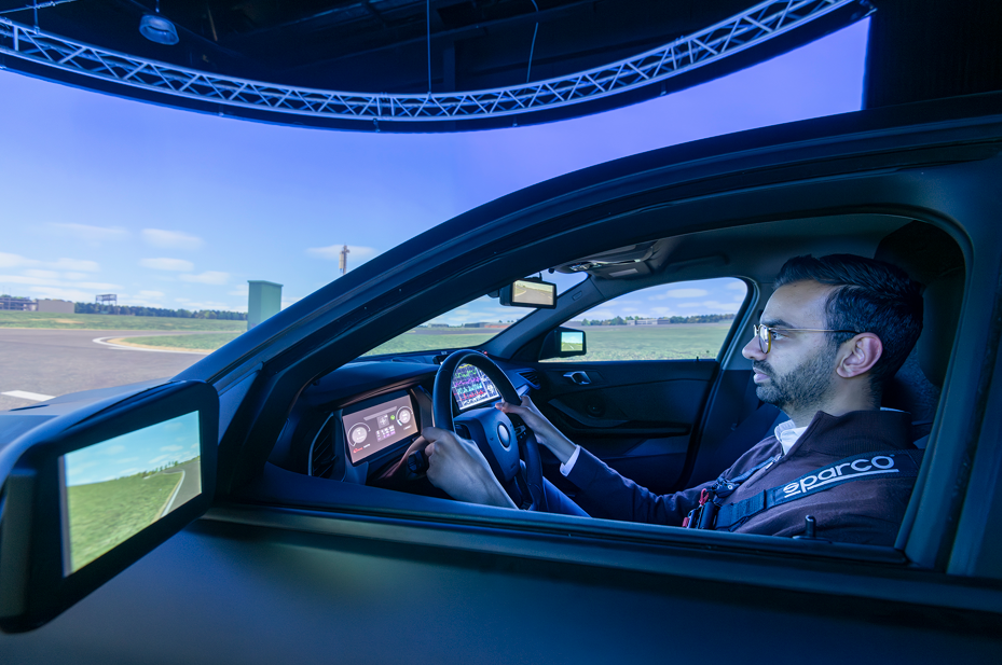
“We’ve been doing this for over 25 years now,” said Lee. “We’ve had the proving ground for a long time, but actually, engineering is one of the core parts of our business now.
“Around about 50 per cent of what we do is pure engineering consultancy and working with customers to develop their vehicles for them. The other 50 per cent is doing the test services, so people using our facilities.”
The Driving Simulator Centre is now a cornerstone of that engineering consultancy. The jewel in the crown at the new facility is a recently installed VI-grade DiM250 Dynamic Simulator - the first of its kind in the UK. The DiM250’s motion platform uses nine actuators instead of the more conventional six, with precise vehicle movement mapped to a huge 120Hz wraparound projection screen.
Strapping into the simulator feels about as close to the real thing as you can get. The authenticity extends to the individual attributes of each vehicle programmed into the simulator, allowing accurate driver-in-the-loop feedback at the earliest stages of development.
“What we’re doing with simulation, what we’re doing on the proving ground and test rigs, it’s all being brought together into the simulator here,” Lee explained.
“And that starts right from the offset. So when we’re working on a development programme, we’ll have the initial engagement with our customer and they’ll have a marketing brief of what they’re trying to achieve. Traditionally, you’d set those targets based on some benchmark data and that’d be it for the rest of the programme. But now what we can do is actually build what we call a ‘parametric model’. We build a model that represents those targets, and we can drive it in the simulator. So right from the early stage in that programme, we’re able to understand what that vehicle will feel like.”
For initial engineering and design concepts, there is a flexibility to play around with geometry and mass distribution, the big picture stuff that has significant effects on vehicle handling. As designs become more settled, the engineering gets more granular. Smaller tweaks to things like damp settings or roll bar stiffness can then be factored into simulation, with the driver able to feed back on these more subtle adjustments and how they affect the feel of the car.
“And of course, we can do it much quicker in here (with the simulator),” said Lee. “We can make changes in here within a few minutes compared to the proving ground that can take a few hours…so we can do a lot more in here, in a much more compressed time frame, much earlier on in the programme.”
It’s hard to put an exact figure on how much development time can be saved with this type of advanced simulation. However, MIRA believes it is significant, potentially cutting the overall number of physical prototypes across the development cycle.
Reducing the need for physical vehicle testing and prototypes not only has time savings, it also cuts associated carbon emissions. MIRA estimates that one developed vehicle model using the VI-grade simulator could avoid as much as 14,000 tonnes of carbon dioxide equivalent (CO2e). Considering the glut of new vehicle architectures coming to market on the back of the EV wave, the upside for OEMs is obvious.
“All these different things, different technology going into vehicles, we’re having to harness that in quite a rapid change,” said Lee. “And so when we’re looking at our engineering process, traditionally, how do we move through it, we’re having to look at it a bit differently. Because the engineering effort is increasing massively…so we’re having to look at different solutions to how we can basically encompass all of those challenges into the engineering development process.”
According to Lee, doing more digitally also helps de-risk vehicle programmes, which invariably come with multimillion-pound price tags. Finding out physical prototypes don’t perform as expected on the proving ground can be a costly business, both in time and money. Simulation allows for virtually infinite numbers of test scenarios to be run, with learnings implemented at the earliest stages of development.
Vehicle attributes in the simulator can be tweaked from the control room. Image: HORIBA MIRA
“By doing far more in the digital domain, we can run far more test scenarios than we normally would,” said Lee, “and we’re making decisions much earlier, before we’ve had to commit to tooling, or parts, or manufacturing, that kind of thing.
“If we tried to do all of this in the traditional ways of engineering, it would take forever.”
In terms of the development cycle, the advantages for both carmakers and MIRA’s own engineers are clear. Perhaps the ultimate success of the simulator won’t be felt for a few years, however, when drivers will actually get to reap the benefits of having their experience placed at the forefront of vehicle development, right from the get-go.
For all their benefits, EVs are often accused of lacking the visceral connection associated with combustion vehicles, the roar of the engine replaced by the more clinical whirr of electric motors. According to MIRA, the next stage of EV design will seek to tap into those more primal automotive desires, with a greater focus on handling and feel. But getting it right on the road means first getting it right on the drawing board, with simulation a vital link between the two.
“We’re moving into putting much more of our engineering effort into simulation,” said Lee. “And we need to keep the driver, the end user, in the loop.”
Amen to that.
More from The Engineer
IET sounds warning on AI doll trend
I agree that we need to reduce cooling water demand for servers. And yes, generative AI consumes a large amount. But what about BitCoins? Their...