Data last year from UK car sector trade body the SMMT showed that battery electric vehicles made up more than one in five newly registered cars.
As demand grows, the UK must adapt, and this includes everything from accelerating charging infrastructure through to sourcing critical minerals needed for battery production.
Hoping to be part of the solution is Green Lithium, which plans to open the country’s first large-scale lithium refinery at PD Ports in Teesside. Construction is planned for 2024 and, once operational, the facility aims to produce 50,000 tonnes of battery-grade lithium hydroxide each year – enough for over 1 million EVs per annum.
CEO Sean Sargent joined the company in January 2021 after many years in the maritime and nuclear sectors. He began his career as a maritime civil engineer working on the design of ports and harbours. Working on Devonport’s submarine facilities led him to the nuclear industry, where he’s spent most of his 32-year career. After taking on various roles in the nuclear sector at Jacobs and Magnox, the pandemic hit in 2020 and, like many others, Sargent’s career took a change of course.
“I was confined to home and started doing a bit of soul searching about where I could add the most value,” Sargent told The Engineer. “The energy transition is something that plays very deeply in my mind … There was a bit of serendipity when an old colleague of mine who knew about Green Lithium contacted me for a chat.”
This coincided, he explained with a decision by Green Lithium to shift its focus away from looking at exploring UK sources. “They realised there were no great lithium ore resources [in the UK] … instead they changed the model to concentrate on the midstream, which is a real bottleneck in the industry, and at that point they knew they needed some programme delivery expertise.”
The firm's mission is to enable the energy transition through the electrification of transport, predominantly EVs, by refining battery-grade lithium salts for EV batteries. But it doesn’t stop there, Sargent emphasised – he believes that the potential of batteries’ role in the energy transition beyond the EV market is underestimated.
“Lithium-ion batteries are used in grid storage and domestic storage as well, and to some extent, I don’t think the full impact that batteries are going to have on the energy transition is fully understood,” he said. “Even if you look at the numbers and believe everything the forecasters say, I think it’s the tip of the iceberg. I think it’s going to be huge, and if you look at the complicated supply chain required to enable the production of all those cells and batteries, it just doesn’t exist today. There’s a part of it that exists in China, but China’s sitting on the largest and fastest growing EV market in the world.”
With concerns around socio-political tensions, he added that he doesn’t believe the UK can rely on these Chinese markets to deliver what the UK and Europe needs to fulfil its 2050 obligations through electrification of transport. And whilst he believes the EV market is well understood, he predicts that the growth will be ‘slower but bigger’ than projected.
“As soon as you realise that batteries on a large scale are viable and affordable, suddenly grid storage using lithium-ion batteries or other forms of battery storage become a serious contender. The way to buffer the storage from wind and solar, I think, is very likely to be large-scale grid storage batteries. Whereas previously people thought it was incredible and there was no way you could make enough materials, the EV market is going to unlock that.”
As it stands, forecasters are projecting Europe will need around 800,000 tonnes of battery-grade lithium per annum by 2030. Currently, none is made locally and whilst Green Lithium has ambitious plans, its projected 50,000 tonnes per annum still makes up less than seven per cent of that demand. The UK has a mountain to climb, Sargent stressed.
It’s a revolution, and our job is to lead from the front and make people realise the importance of this revolution, because without it you can almost guarantee that the 2050 commitments won’t be achieved
“What we’re seeing is government is very focused on it,” he said. “We’ve enjoyed some great governmental support through the Automotive Transformation Fund, which is providing access to grants for every step of the way. But it is interesting, I think, particularly to see how countries like the UK are going to secure the critical minerals. For us, that’s the most important part.”
Accessing and importing the raw materials was a critical factor in choosing the location for the refinery, Sargent pointed out – the daily shipping routes to all Europe’s major ports was an important benefit. But it was Teesside’s decarbonisation landscape that gave it the winning edge. “Planning, as we are, to produce lithium without producing any carbon is a challenge. It’s a thermal process, we use a lot of electricity, we use a lot of gas, so we needed to be in a site that enabled us to decarbonise,” he said, "Teesside gives us all of that, it’s beautifully placed in one of these decarbonisation clusters where we can see an emerging landscape that will provide the infrastructure we need.” This includes access to renewable and low-carbon electricity and access to hydrogen and carbon-capture technologies, of which Green Lithium is exploring modular and industrial options to ensure the maximum carbon reduction for its investment.
“What’s really worrying is there’s a right way and a wrong way to electrify transport,” said Sargent. “There are examples of low-grade minerals being refined in south east Asia at the moment that produce more CO2 than an ICE would over its entire life – so, rather bizarrely, you could be buying an EV and pushing up your carbon footprint. It’s imperative that we find low-carbon solutions.”
As well as decarbonising processes on site, the company's also exploring circular economy opportunities elsewhere. This includes exploring retrieval of lithium from recycled batteries. “Like most things in the sector, people are using old technology to measure what’s being done,” he said, adding that while lithium recovery from batteries is very rare currently due to pyrometallurgy processes which destroy the lithium, the ‘smart money’ is beginning to back hydrometallurgy processes where all battery metals can be extracted.
“There’s a lot of closely guarded secrets in the market at the moment but we think there will be some midstream lithium salts that will be produced by the battery recyclers and we aim to work with them to convert and re-refine those midstream salts back to battery-grade materials.
“The market is not going to be significant until the first generation of EVs start to wear out and they’ve been through their second life opportunities. But ultimately, in the long-term, we think it’s important that once you get the lithium out of the ground, you never waste it. It continues to be recycled through battery metals. We think we’ve got an important part to play as part of that recycling supply chain.”
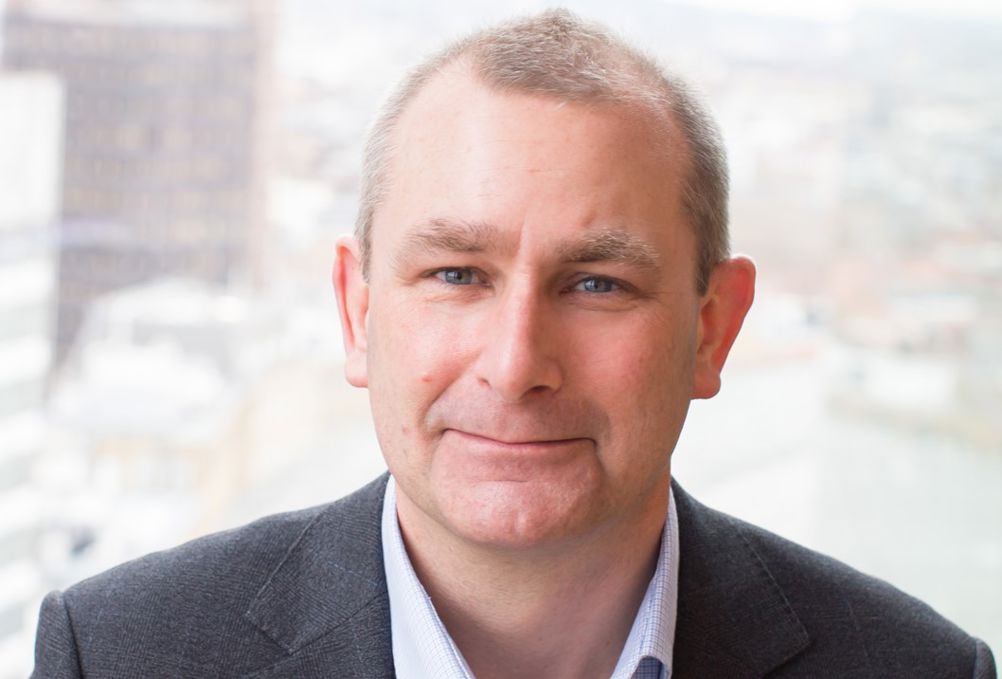
Another key challenge is producing lithium with zero waste, and here Green Lithium is working with Sheffield University to find circular economies for the by-product aluminium sodium silicate. “The key [industry] of focus is the construction industry, but....we’ve probably identified between ten and 20 potential applications for that by-product. A lot of those require conditioning, so we’ll have to do further work.....to make it fit for those markets.”
Overall, the challenge isn’t underestimated by Sargent – he questioned where the resources will come from to meet demand, and with the number of refineries, cathode production facilities and gigafactories that will be required, he pointed to the UK’s skills shortage as another barrier. “These are skills that largely don’t exist in the UK. We haven’t been big in mineral processing for a long time … That’s why I say that things are going to be slower and bigger than anybody realises. We’ve almost got to retrain engineers to be able to meet that challenge before we can deliver it.
“It’s a revolution, and all revolutions in history have had some false starts and some bumps along the way. Our job is to lead from the front, to lead by example, be very visible in what we’re doing and make people realise the importance of this revolution, because without it you can almost guarantee that the 2050 commitments won’t be achieved.”
McMurtry Spéirling defies gravity using fan downforce
Ground effect fans were banned from competitive motorsport from the end of the 1978 season following the introduction of Gordon Murray's Brabham...