From relentless rain and mud, to searing heat and ground baked to the consistency of concrete, the world of farming is faced with a broader range of operating conditions than most other areas of industry. Add to this the potentially crippling cost of downtime in a sector with exceptionally fine profit margins and the requirement for hard-wearing, low-maintenance engineering solutions is clear.
One firm meeting this challenge head-on is Yorkshire-based Sumo UK, which produces a wide range of machinery including cultivators, seed drills, and subsoilers designed to prepare soil, plant seeds, and manage crops with efficiency and precision.
The firm’s reputation for quality has made it a trusted name in the sector and helped build an international customer base but to meet the demands of this growing base and satisfy the requirements of range of different conditions and soil types Sumo faces a constant challenge: finding components that can withstand the rigors of agricultural use while reducing maintenance costs and environmental impact. To address this challenge, it turned to a polymer bearing specialist igus, and its range of igutex bearings.
Agricultural machinery often operates under extreme conditions, bearing heavy loads and enduring constant wear and tear. Traditionally, metal bearings requiring regular lubrication were the go-to solution. However, these bearings not only demand frequent maintenance but can also pose environmental concerns due to the need for lubrication.
The igutex bearings are designed to handle high loads and harsh conditions without the need for lubrication, making them an ideal fit for Sumo's heavy equipment, which often weighs upwards of ten tonnes.
Igutex bearings are made from a composite material engineered with fibers and resins treated under high temperatures and pressures, creating an exceptionally durable product. These bearings can handle extreme temperatures, ranging from -60 degrees to +120 degrees Celsius, making them suitable for various industrial environments.
Giving an extreme example of the conditions encountered by its equipment, Sumo MD Steve Ridley pointed to the challenges faced by customers in Perth, Australia: “They’re trying to cultivate ground that's had no rain for four months. They're trying to go as deep as they can to alleviate compaction. They're driving all day before they make a headland turn. The heat of the ambient temperature, the heat of wearing metal in the ground is on a scale that you'd never ever see in Europe.”
In this unforgiving environment, igutex bearings, and the fact they’re lubrication free, represents a major plus point he said: “there's massive advantage because they're not going to get out halfway through the day with a grease gun and lubricate bearings and points…..that reduced maintenance is a big plus for the end user.”
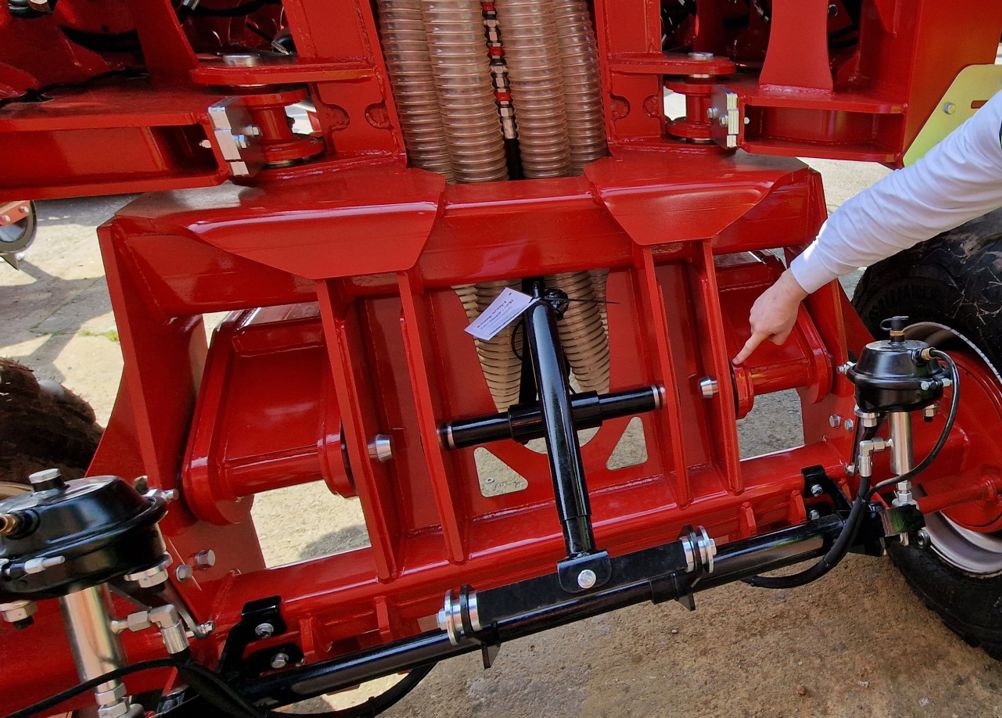
Sumo first began working with igus in 2017, and has been using the company’s iglidur plain bearings on a range of applications ever since. Sumo engineering manager Tim Lord reports being struck by the fact that when taking machines apart for refurbishmnent, the igus bushes being used looked as good as new, and that this positive experience drove a decision to explore other products and specifically see how the igutex bearings fared in high-load applications typically dominated by greased metal bearings.
The results were impressive. After extensive testing, Sumo UK Ltd concluded that igutex TX1 and TX3 bearings were the best components for their equipment. These bearings are primarily used in the articulation geometry on folding hinge points, running on mild steel connection pins, where they withstand heavy-duty loads and also eliminate the need for lubrication, reducing maintenance costs and environmental impact.
Radio wave weapon knocks out drone swarms
Have they tested the effectiveness of the system against the new generation of fibre-optic guided drones now being deployed by both side in the war in...