Software evaluates the cost impact of design decisions early in the development process
Manufacturing businesses across all sectors face a growing challenge to reduce costs and bring products to market more quickly. And an innovative software tool that helps engineers calculate the cost implications of early stage design decisions on the fly is helping a growing number of users achieve exactly that.
Developed by US software firm aPriori, the software – also called aPriori – works by introducing considerations over manufacturability far earlier in the product development process than is often the case. Existing users span a range of sectors and include Alstom, Ford, Whirlpool, Honeywell, Boeing, HP, and Cisco. Integrating smoothly with any CAD package, the software ticks away in the background as the designer makes changes, and provides instant feedback on how these decisions are likely to affect the end cost, as well as guidance and suggestions on changes that the designer might like to make to bring the cost down.
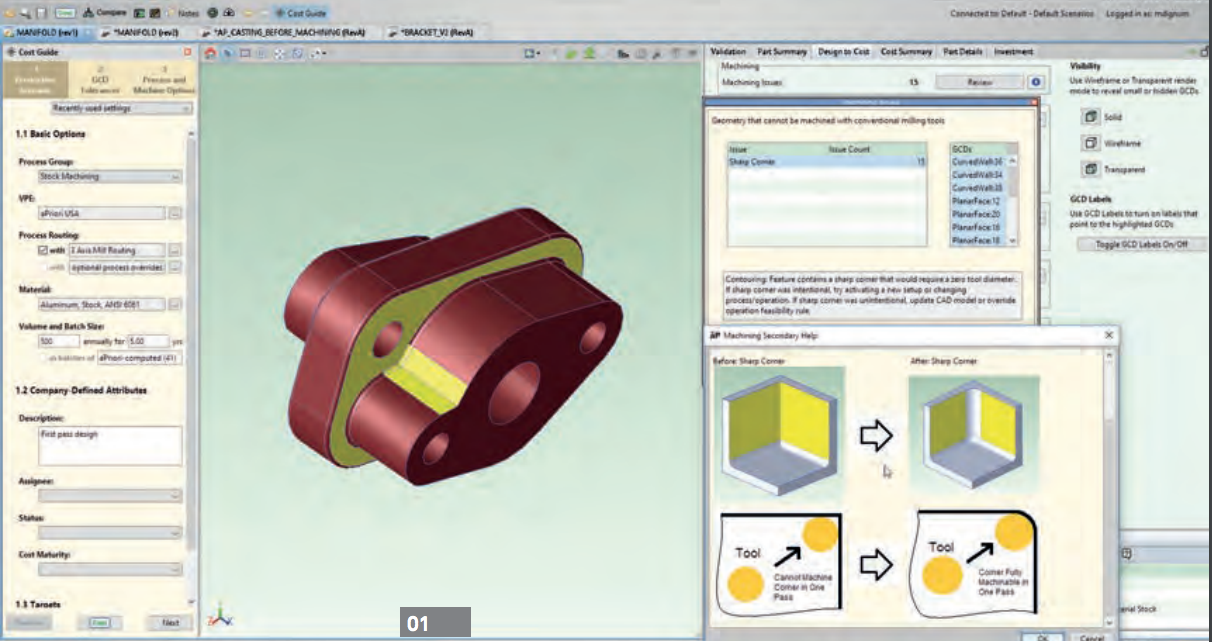

aPriori sales director James Dainty explained that the software begins its work by analysing the geometry of a 3D CAD model. “If it’s looking at a casting it will look for wall thicknesses, voids, holes, and what might be machined features,” he said. “If it’s a sheet metal part it will looking for how many bends there are going to be and things like that. If there are tolerances applied it will also look at the tolerance and surface finish information.”
If you take cost out early in the cycle it has a bigger impact than having to manage it out later on.
Having analysed this information it will then consider the manufacturing processes that could be used. “If it’s a casting it will think, am I going to die cast it or sand cast it?” added Dainty. “If it’s got to have secondary machining will it use a 3-axis mill with multiple set-ups, or a 5-axis mill with a single set-up? If it’s plastic what is the optimal machine it would go on?”
Throughout this process the tool also factors in up-to-date information on the labour and material rates in multiple regions around the world (as well as packaging and logistics costs) in order to calculate the real cost implications of these early stage design decisions. Guy Langley VP, EMEA for the firm, said that the software enables businesses to take a fundamentally different approach to cost reduction.
“There’s not been a great deal of pressure on the design engineer from the perspective of cost,” he told The Engineer. “It’s all been fit, form and function – now we’re starting to see a lot of organisations where the business is turning to engineering and saying you need take cost out – because if you take cost out early in the cycle it has a bigger impact than having to manage it out later on.”
As well as enabling early visibility of cost, the software also helps companies analyse a multitude of design alternatives – potentially as many as 1,000 – for the cheapest fit, form and function. Despite an inevitable perception that tools like this are giving design engineers even more to do, Langley said that the reaction from users has been broadly positive. “You get engineers turning around saying ‘hang on a minute, you want us to design it, analyse it, you want us to use all these other simulation tools and you want us to cost it as well?’, but once they start using it and realise it’s not going to be a huge overhead a lot of them are very positive.”
If it works well you’re going to pay for it within the first year
He added that this is particularly true of younger engineers, who are typically quicker to embrace change and often keen to learn more about the manufacturing process. What is more, he added, there is a strong argument that the tool actually simplifies the design process by reducing the amount of “thrashing” to and fro in an effort to bring down the cost.
The savings that can be enabled by the technology are potentially huge, claimed Langley. “If you work well, within the first year you’ll start seeing benefits. One customer that’s been using the product for five years is getting a nine to one return on investment. If it works well you’re going to pay for it within the first year.”
Guest blog: exploring opportunities for hydrogen combustion engines
"We wouldn't need to pillage the environment for the rare metals for batteries, magnets, or catalisers". Batteries don't use rare...