Expert Q&A: how AI is driving developments in battery technology
Experts from across industry and academia explain how artificial intelligence is being used to drive and accelerate the development of battery technology
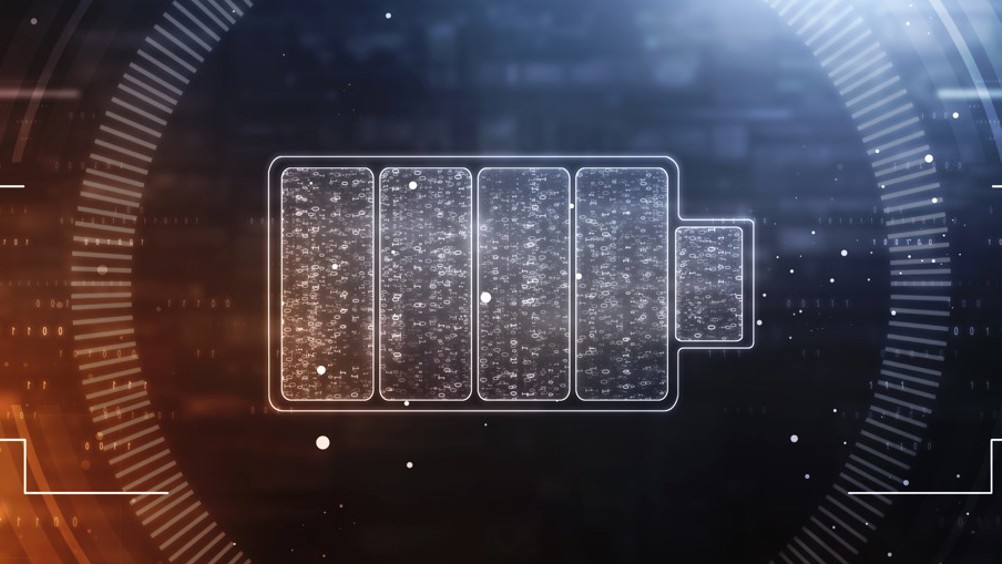
As the low carbon revolution gathers pace, the demand for new and improved battery technologies has become one of the fastest moving areas of technology development, and artificial intelligence (AI) is playing an increasingly important role in delivering the advances required.
Over the following pages we hear from some of those at the cutting edge of developments in this area: from the discovery and characterisation of new materials and chemistries, to the optimisation of manufacturing processes.
We learn how the UK’s Centre for Process Innovation is using AI tools to accelerate the scale up of new battery technologies; how Imperial college Spin-out Polaron has developed AI technology that can fine tune gigafactories; how AI software specialist Monolith is helping engineers analyse test data in ways that can cut weeks off development timelines, and how battery power systems expert Fortescue Zero is using the technology to give unprecedented insights into battery performance and longevity.
Register now to continue reading
Thanks for visiting The Engineer. You’ve now reached your monthly limit of premium content. Register for free to unlock unlimited access to all of our premium content, as well as the latest technology news, industry opinion and special reports.
Benefits of registering
-
In-depth insights and coverage of key emerging trends
-
Unrestricted access to special reports throughout the year
-
Daily technology news delivered straight to your inbox
Water Sector Talent Exodus Could Cripple The Sector
Well let´s do a little experiment. My last (10.4.25) half-yearly water/waste water bill from Severn Trent was £98.29. How much does not-for-profit Dŵr...