Retrofitting Shell’s Patricia Camila LNG tanker with air lubrication
led to significant fuel and emissions savings for the giant vessel. Andrew Wade reports.
C2I 2021
Category: Wildcard
Winner: Patricia Camila Air Lubrication
Partners: Shell Shipping and Maritime,
As with many of the entries across the 2022 C2I Awards, the winner in our Wildcard category has strong environmental credentials. Adapting an emerging technology for a novel application, the Patricia Camila Air Lubrication project saw the first ever retrofit of an Air Lubrication System (ALS) to the hull of an LNG (liquid natural gas) carrier, resulting in fuel savings of around seven per cent.
Air Lubrication Systems create a coating of micro-bubbles at the boundary layer between a ship’s hull and the sea, reducing the friction generated by the ship as it sails through the water. The technology was first conceived of at the start of the century, tested initially in labs, then rolled out on the first vessels as the need to reduce the carbon impact of shipping became more pressing.
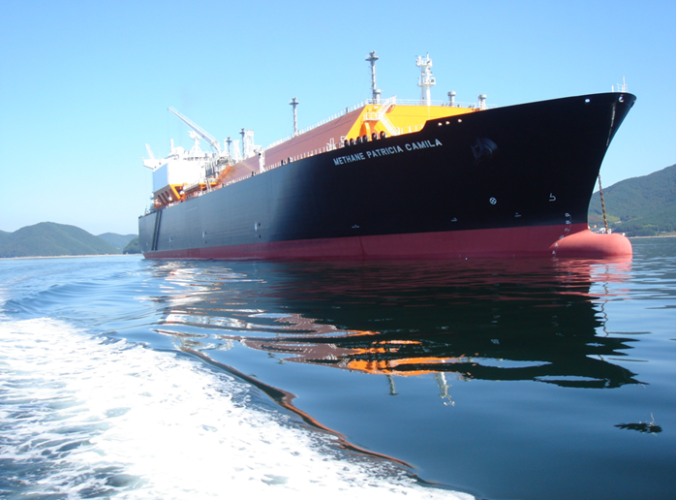
Shell, the owner of the Methane Patricia Camila LNG carrier, deployed ALS on its first oil tanker in 2017. Having seen the benefits in fuel savings and reduction in CO2 emissions, plans to adopt the technology more widely were drawn up, including a design for a retrofit of the Patricia Camila.
“The installation work for this technology consists of two main phases,” explained James Helliwell, Innovation, Research & Development Project Engineer at Shell Shipping and Maritime. “The first phase is the installation of equipment called Air Release Units or ARUs. The ARUs are hull penetrations welded into the forward section of the flat bottom area of the ship.”
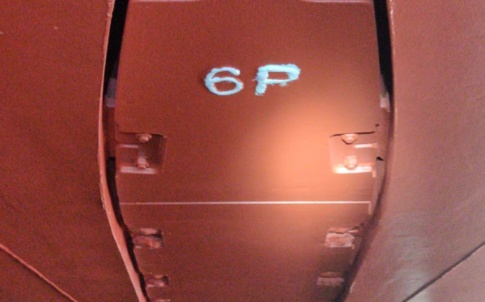
The ARUs are the devices that actually generate the micro-bubbles on the hull. For the Patricia Camila, 16 of these ARUs were installed while the vessel was in dry dock in Singapore. Valves were then fitted to these units to ensure that the openings are watertight.
“Once the ship is back in the water, piping is then installed,” Helliwell continued. “The piping runs from the 16 units in the bottom of the hull to a machinery space above the waterline at the forward end of the ship. In this machinery space, eight air compressors are installed which provide the air for the system. Electrical cabling and control system cabling is also installed to power and operate the full system.”
According to Shell, the full installation was completed in 37 days, with 16 days in dry dock. However, this included some minor delays associated with the COVID pandemic. Without these setbacks, it’s claimed a retrofit installation can usually be completed within a 30-day dry docking period.
“For Patricia Camila, we’ve seen a reduction in fuel consumption of up to 6.6 per cent from the system,” said Helliwell. “To convert this into tonnes of fuel saved, this would roughly equate to a reduction in fuel of 2,138 tonnes saved in a year, depending on where the vessel sails and the speed at which she sails.”
The results so far have been impressive, but the sailing wasn’t all smooth throughout the life of the project. With the two main technical partners (Shell Shipping and Maritime, Silverstream Technologies) based in London, and a retrofit taking place at the Singapore shipyard of Sembcorp Marine, the COVID pandemic made remote collaboration essential.
“It really was a challenge,” said Helliwell. “The design phase was done pretty much entirely over Microsoft Teams and email, with Silverstream sharing all of the technical documentation with the different stakeholders via these tools.
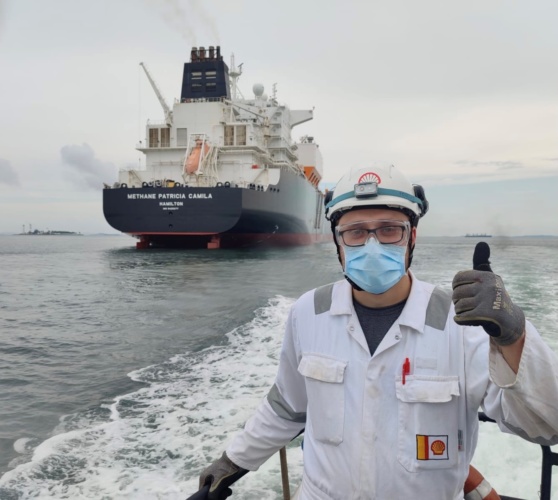
“We would then have weekly design calls via Teams to agree key design decisions, review documentation and work through the design. These calls became bi-weekly and eventually daily as we got closer to the installation. Key to managing the process was an action tracker and decision register, which helped to keep track of all open items and the decisions made.”
The Patricia Camila is the first ever LNG to have the Silverstream air lubrication system installed, which inevitably demanded innovations to meet the challenges of a pioneering project. For example, the ALS had to be integrated with the existing Kongsberg Maritime automation control system onboard the vessel, the first time Silverstream had attempted to do so on an LNG platform. In addition, the project saw the team developing the first ever strategy to optimise ALS for LNG carriers, taking into account the reduction in fuel and the consequent additional gas boil off that must be reliquefied rather than used for propulsion.
“Any reduction in fuel consumption from the ALS is more cargo boil off that needs to be reliquefied and put back in the tank,” Helliwell explained. “Understanding how to optimise ALS and reliquification is an important development. This will also develop further as we continue to gather data from the Patricia Camila.
“We also developed a modified deflector plate for the Silverstream ARU which is now being applied to all Silverstream designs. This modified plate increases diver accessibility should any emergency repairs to overboard valves of the system be required.”
Having demonstrated the effectiveness of ALS technology for LNG carriers, Shell has now committed to rolling it out across all its new-build LNG vessels. The energy giant also has plans in place to retrofit the system to its existing fleet, though doing so requires coordination with the dry dock schedule of a number of ships, with each vessel needing a tailored design and implementation according to its individual characteristics.
“The only barrier is the five-year dry-docking cycle for shipping,” said Helliwell. “Ships dry dock every five years, so we need to wait for the next vessels to get closer to their dry docking period before starting retrofit design work.”
With shipping accounting for around 90 per cent of global trade and 2-3 per cent of global greenhouse emissions, it’s a sector in desperate need of solutions to reduce its carbon footprint. Zero emissions shipping – made possible with nascent technologies like hydrogen-powered propulsion – is claimed by some to be a realistic goal by 2050. In the meantime, however, solutions like ALS can start to chip away at the sector’s emissions, increasing efficiency and helping to plot a course to a greener maritime future.
Comment: Hydrogen requires a long-term mindset
I'm fairly certain there were plenty of nay sayers in the early 19th century that refused to see the benefits of railways and steam power and...