Category: Manufacturing Technology
Project: A single-click automated manufacturing metrology demonstrator
Partners: Midlands Centre for Data-Driven Metrology; Manufacturing Metrology Team (MMT) (Faculty of Engineering, University of Nottingham); The Nottingham Advanced Robotics Laboratory (NARLy); The Advanced Manufacturing Technology Research Group (Faculty of Engineering, University of Nottingham); Intelligent Automation Centre (Loughborough University); Institute for Advanced Manufacturing and Engineering (Coventry University)
In the space of a few decades 3D printing has evolved from a means of visualizing designs in a solid 3D format to a tool that is as vital to manufacturers as machine tools.
In the space of a few decades 3D printing has evolved from a means of visualizing designs in a solid 3D format to a tool that is as vital to manufacturers as machine tools.
3D printing, or additive manufacturing, builds a part layer-by-layer while CNC machinery reduces billet with cutting tools to produce a part.
They are both in the technological toolbox that enables the practice of advanced manufacturing, which TWI defines as the ‘practice of using innovative technologies and methods to improve and enhance competitiveness within the manufacturing sector.’
Common to both production techniques is the use of CAD/CAM to help define and produce a finished product. Another commonality is that parts produced these ways need inspecting before they leave the shop floor.
However, the rapid expansion of advanced manufacturing technologies across sectors such as additive manufacturing, aerospace, automotive, and medical industries has created a pressing need for more sophisticated inspection strategies.
Traditional measuring methods often struggle to optimally measure parts produced by modern manufacturing approaches, especially with complex additively manufactured parts.
The winners of the C2I Manufacturing Award for 2024 have addressed this in a project titled ‘A single-click automated manufacturing metrology demonstrator’.
In this project, team members across multiple sites are seeking to produce the single-click measurement solution utilising several non-contact measurement technologies in combination with machine learning to produce a quick and efficient solution that streamlines complex measurements through automation.
By doing so, the project addresses the need for accurate quality inspection in advanced manufacturing, with potential benefits for several industry sectors.
Customizable and scalable, this R&D demonstrator platform integrates new technologies, custom-code, machine learning, and digital manufacturing trends to improve speed, reduce costs, and enhance quality inspection.
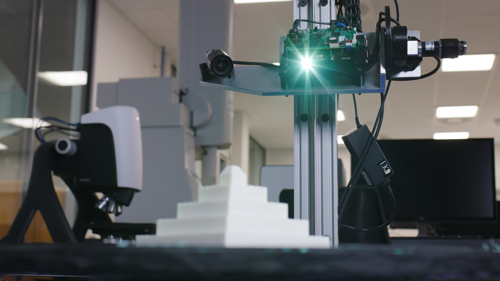
“This grand undertaking leans on foundational research undertaken at the Manufacturing Metrology Team [MMT] at the University of Nottingham over the past seven years, bringing the findings together into a unified demonstrator,” said Prof Samanta Piano, director of the Midlands Centre for Data-Driven Metrology (MCDDM).
Piano explained that MCDDM is a multi-site collaboration between the University of Nottingham, Coventry University and Loughborough University that led the initial phase and has yielded significant progresses in developing customised optical metrology solutions for advanced manufacturing applications.
Piano added that given the complexity of parts fabricated in advanced manufacturing industries, measurement techniques that can capture dimensional information are required not only to act accurately, but also in a way that is user-friendly and allows efficient data capture.
The team focused on integrating front-line optical metrology technologies - fast camera acquisition, automated background removal, three-dimensional (3D) photogrammetry reconstruction, camera-object location optimisation, fringe projection measurements and point cloud analysis - and machine learning into a cohesive system for coordinate measurements. The system’s control software is designed to present a single-click, automated solution, capable of initially detecting the position and pose of a measured object using photogrammetry.
“This integration enhances measurement speed and automation, moving towards a streamlined, user-friendly solution capable of performing reverse engineering that minimises complexity for end-users,” said Piano.
To date, the project has implemented recommendations supported and informed by industrial partners of the MCDDM, including Zeiss, Mitutoyo and MTC.
The project’s success has allowed the team to look at a future second phase that aims to concentrate more on the speed and integration of machine learning to optimise this optical demonstrator into a single-click solution.
“This will develop a platform with low interventions from the user and ensuring the highest quality standards in advanced manufacturing processes,” said Piano.
The demonstrator is one of the primary activities of the MCDDM, which focusses on transferring knowledge from academia to industry through translational research and dissemination.
By integrating the research taking place at MCDDM’s member institutions, the project has created a continuously improving demonstration test bed that showcases the innovation and advancements of a variety of research projects in a single system.
Furthermore, the project has benefited from insights of industrial partners and interactions with 34 SMEs between 2021 and 2023 that have contacted the MCDDM looking for support in digital manufacturing and new inspection technologies.
In the MMT and NARLy, the project's success has been bolstered by different mindsets, expertise, and perspectives, said Piano, who manages the project with Loughborough’s Professor Peter Kinnell in the field of metrology and industrial automation, Coventry’s Professor Marcos Kauffman in digital twin implementation, and Nottingham’s Professor David Branson in the field of dynamics and controls.
Across the collaboration, Dr Luke Todhunter (MMT and technical project manager), Dr Sofia Catalucci (MMT) and Dr Francisco Ulises Hernandez Ledezma (MMT) lead the software integration pipeline with open-source code in python and MATLAB.
Dr Adam Thompson has led the mechanical design of the overall demonstrator along with the installation of hardware, which is complete, while Dr Mojtaba A Khanesar (NARLy) leads the software programming for precise motion control of linear and rotational stages.
The project has benefited also from the input of PhD students Mingda Harvey Yang and Zhongyi Michael Zhang who’ve deployed machine learning and machine vision algorithms to optimise photogrammetry 3D reconstruction and developed novel data fusion algorithms for point cloud registration respectively.
According to Piano, the innovative culture in this project is driving continuous improvement. MCDDM is currently working in existing trends, embracing machine learning technologies, and customer needs to identify gaps and potential areas of improvement.
Looking ahead, the project may collaborate with providers of inspection instruments, such as Bruker Alicona, and incorporating these devices mounted on collaborative robots.
“This integration will contribute an additional layer of expertise to the project's capabilities, enabling the demonstrator to be benchmarked against other commercial products,” said Piano.
As the project evolves, the goal is to maintain an advanced metrology demonstrator at the state of the art, incorporating future research activities within the MCDDM involving optical metrology technology advancements and machine learning enhancements. “The project team is dedicated to pushing the boundaries of metrology to meet the evolving needs of advanced manufacturing with machine learning, thereby contributing to improved component quality, reduced defects, and enhanced overall manufacturing efficiency,” said Piano.
Invinity to build 20MWh flow battery in UK
Yuk - batteries are horrible, poisonous, short-lived and unsustainable things. It is about time that we invested in much more compatible mechanical...