C2I 2021
Category: Information, Data & Connectivity
Project name: Harnessing Industry 4.0 to optimise performance in the aluminium industry
Partners: Air Products with Tandom Metallurgical Group
Category sponsor: PTC
Where would we be without aluminium? The ubiquitous metal touches virtually every aspect of our daily lives, from the cars we drive, the buildings we live and work in, the aircraft we fly in, and the cans we drink from. The uses for aluminium are numerous and too long to list here, but at just over 64.4 million tonnes in 2019, aluminium is the most highly produced metal globally, with China topping the output league at 36,000 tonnes in the same year.
Aluminium is derived from bauxite and the process of taking it from raw material to finished product can be very carbon intensive. That’s the bad news. The good news is that once its made it is almost infinitely recyclable, a fact not lost on producers keen to continue using the versatile raw material while cutting down the environmental impact of their activities.
The winners of the PTC-sponsored Data & Connectivity category of the 2022 C2I Awards have brought further gains in the production of ‘secondary aluminium’ with their entry titled ‘Harnessing Industry 4.0 to Optimise Performance in the Aluminium Industry’.
The story began in 2020 when Air Products teamed up with Tandom Metallurgical Group (Tandom) – a Congleton-based producer of aluminium alloys, master alloys and recycled aluminium products, scrap and dross - to explore how the introduction of smart technology - such as equipment sensors and associated analytics - could generate data that could be used to boost efficiency and productivity, improve yield and reduce carbon emissions.
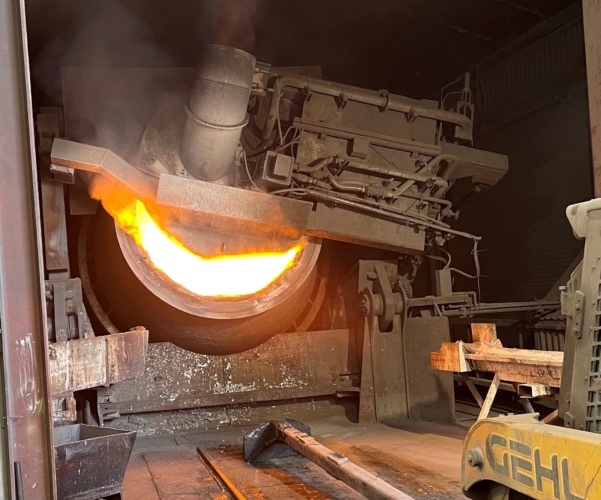
Dr Martin Lawrence, Combustion Development Specialist at Air Products explained that the aluminium recycling sector is heavily reliant on an operator’s skills and experience to predict when the aluminium has reached tapping temperature. This, combined with the significant variability that is inherent in the remelting process, can often lead to suboptimal performance and inconsistent results. This means longer cycle times, reduced energy efficiency and increased aluminium losses.
To overcome these limitations, Air Products and Tandom embarked on a ten-month study that utilised Air Products Process Intelligence (APPI) Process Advisor system to capture and use equipment, process and operational data to create a digital twin of Tandom’s remelting process.
According to Dr Lawrence, the APPI Process Advisor system provided new data insights to Tandom personnel at all levels, giving operators and managers remote access to real time and historical data, which brought a greater understanding of performance and reduced downtime by flagging maintenance issues more quickly.
“The team at Air Products designed the system to capture all operational data that was traditionally recorded on paper, which reduced errors in data collection and provided Tandom with their operational data in real time,” Dr Lawrence said. “Storing the records digitally also meant that the Tandom team could quickly analyse furnace performance, leading to more accurate decisions affecting productivity.”
He added: “Traditionally, this is a sector that has relied solely on human skills and experience of an operator to predict when the aluminium has reached tapping temperature. This often leads to inefficiencies and inaccuracies. The APPI Process Advisor system was developed to address these issues and provide more consistent and accurate results in aluminium remelting.”
Results showed that metal tapping temperature was significantly lower and more consistent, which increased aluminium yield and productivity, as well as reducing fuel consumption and carbon dioxide emissions. Lawrence said the team at Air Products analysed the data from over 2,400 melt cycles to understand the relationship between tapping temperature and performance.
“A clear relationship between tapping temperature and aluminium oxidation was identified, showing an exponential increase in aluminium oxidation with an increase in temperature above the aluminium melting point (660oC),” he said “This was in line with academic lab studies published in the literature and was the first study of its kind to be carried out on a production furnace and confirm that this relationship can be seen…Furthermore, preventing the metal from overheating also saves energy and time, as the majority of the melt cycles were overestimated by the operators without the aid of the model.”
Tandom is committed to continuous improvement and its experience in the sector allowed it to identify inefficiencies in the overall melt cycle that were directly affecting productivity, energy consumption and yield. It did, however, need Air Products’ digital expertise in collecting and analysing sufficient levels of data to create a baseline, and its support in using Industry 4.0 technology to apply a solution.
"The team at Air Products designed the system to capture all operational data that was traditionally recorded on paper, which reduced errors in data collection and provided Tandom with their operational data in real time"
Dr Martin Lawrence, Combustion Development Specialist at Air Products
“This project is an example of how collaboration between industry and specialist third parties is critical - and can create significant results,” said Dr Lawrence. “The partnership didn’t just theorise about identifying an innovative approach to achieving greater productivity, efficiency and sustainability. The collaboration was a crucial element in sharing expert insight, user experience and commercial goals, to make sure the technology was fit for purpose. Thanks to the willingness of both organisations to collaborate and share data, there is now a model in place for the wider sector to follow.”
Dr Lawrence explained that Air Products usually undertakes development projects within a laboratory setting or at an Air Products’ site. This made regular dialogue essential and to that end Air Products visited Tandom’s factory on a weekly basis to work alongside the operators, operators’ supervisors and maintenance manager to make sure they understood what the project’s objectives were. It also meant that Air Products’ engineers could monitor how the technology was being used, if it was working well and make any adjustments as necessary whilst listening to feedback.
“One of the key challenges was to build the operators’ confidence,” said Dr Lawrence. “It was vital to listen to their feedback, as it would help the team to make any changes and in turn, build trust in the technology. The model’s tapping temperature was initially set much higher to guarantee the aluminium was ready for tapping; if it was too cool, the metal would freeze as it moved along the 30-40m launder, causing product loss and a significant clean up. Once confidence was built, the temperature was reduced to 720°C.”
Indeed, a key outcome of the project found that tapping liquid aluminium at 900°C as opposed to 750°C for a charge material with 80 per cent aluminium content will lead to an additional yield loss of about three per cent. Furthermore, the metal tapping temperature also led to an average of 15 per cent reduction in energy consumption.
Category sponsor
We are in the midst of the next industrial revolution when engineers and manufacturing specialists are using data to inform purchasing decisions, create better products, optimise processes and overcome production bottlenecks by preventing machine downtime. With 5G technology becoming more readily available, the time for digital transformation is now. PTC is developing all of its software to help our clients make the most of the information they now have at their fingertips. Collaboration and the development of strong ecosystems will be vital if UK industry is to make the most of digital manufacturing and the advantages of enhanced connectivity. In short, new technology can no longer just be the preserve of large companies with big R&D budgets and the ability to explore new ways of doing things. This is why PTC has chosen to support The Engineer’s Collaborate to Innovate Awards competition.
Radio wave weapon knocks out drone swarms
Probably. A radio-controlled drone cannot be completely shielded to RF, else you´d lose the ability to control it. The fibre optical cable removes...