The UK’s ageing rail infrastructure has always presented a range of challenges for engineers; with many of its 19th Century tracks, tunnels, and stations requiring constant repair, upgrades, maintenance and modernisation to meet the demands of a modern transport network.
One particular headache - and an issue with which UK rail infrastructure-owner Network Rail has been grappling for some time - is the thousands of small and medium sized stations either without footbridges or with structures that are now nearing the end of their operational lives.
Modular design
As part of the latest effort to address this, the AVA consortium, a group of UK engineering firms funded by Innovate UK and Network rail, has developed a novel modular footbridge and lift system that is claimed to be greener, longer lasting, simpler to maintain, more cost-effective and easier to install than existing solutions.
Whilst the first AVA bridge is expected to open in summer 2025 at Stowmarket Station in Suffolk, a prototype demonstrator was installed at the Sittingbourne, Kent HQ of consortium partner specialist steelwork fabricator McNealy Brown, earlier this summer. The Engineer went along to have a look.
According to the team behind the structure - which also includes main contractor Walker Construction, steel-maker Outokumpu, architect Hawkins Brown, consultancy Expedition Engineering and the project’s lift designer, “kinetic solutions” specialist ARX - the new system represents a fundamental rethink on the way that bridges of this kind are designed and built.
The methods used to design, fabricate and build footbridges have changed little since the 1960s with each project bespoke and tailor-made for the peculiarities of its site. It’s an approach that takes time and budget, and limits how many footbridges Network Rail is able to build. “Bridges haven’t changed much over the past 50 years which presents a real challenge for the rail industry,” explained Chris Head, Construction Manager at McNealy Brown. “They take too long to deliver and are too expensive and difficult to maintain. And it’s just not a great passenger experience. We’ve completely changed the manufacturing methods, we’ve changed the materials, and we’ve taken a completely different approach.”
Whereas a traditional bridge of this kind is made by welding beams of steel together to form a frame, the AVA bridge is made from components that have been laser cut and bent from flat sheets of stainless steel, which are then bolted together into sub-assemblies, and ultimately major assemblies that integrate the lighting and services.
Modern manufacturing techniques
This entire process is carried out in factory conditions using the kind of state of the art techniques more commonly associated with the precision manufacturing sector. “We’re using robotics, we’re using fiber laser technology to cut the parts - which is incredibly accurate - and we’re using CNC brake presses to form the shapes. So the quality is very, very accurate and very, very repeatable,” explained Head.
One of the chief advantages of this modular approach is it that it also enables bridge designs to be rapidly adapted and optimized for different sites, making it an ideal solution for the UK’s diverse mix of smaller railway stations. “We’re making lots and lots of standard parts that are then reused over and over again on each module,” said Head, “and we just need to tweak a few bits here and there to make bespoke bits to adapt it to the environment in which it’s going to be located.”
This approach also makes series production possible, a critical consideration for a solution that could potentially be deployed at hundreds of sites across the UK. “Depending on the procurement pipeline, it is even possible to have a whole bridge worth of parts sat on the shelf ready to go before the scheme is even decided. That is completely different to the way things are done at the moment,” added Head.
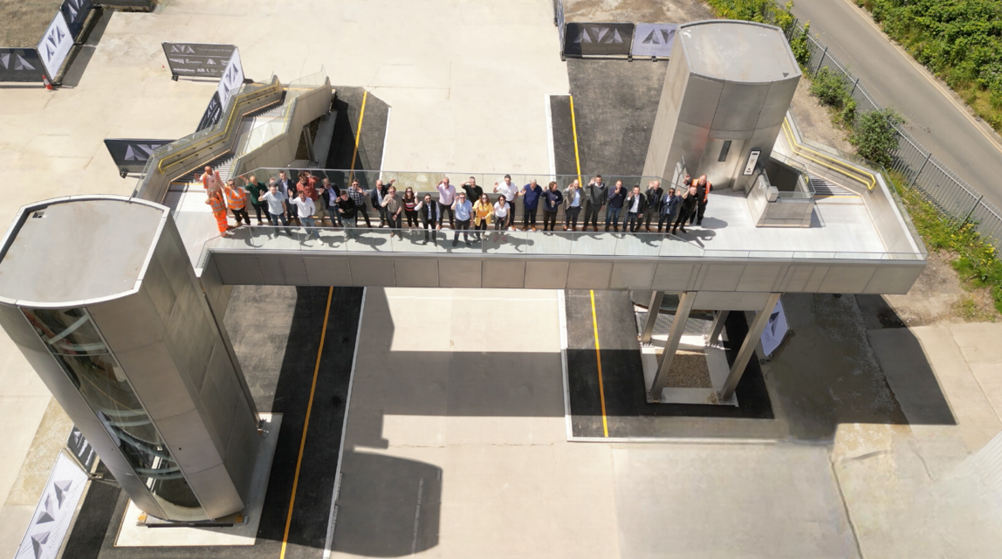
Expanding on the AVA bridge’s advantages over competing structures, Hazel Needham - associate structural engineer at consortium partner Expedition Engineering, said that an estimated design life of 120 years make it inherently greener and more cost effective than other solutions and much of this - she said - is down to a design that minimises the requirement for maintenance.
For instance, whilst maintenance to existing bridges often requires expensive and disruptive shutdowns of the railway, AVA’s design means that all areas of the bridge - such as lighting and electrical systems - can be accessed from the deck. “Access to the areas that you would need to get to on the AVA bridge are all down from the deck. If you need to replace any decking or get under the decking to the drainage, you can just lift up panels …so you don’t need those railway possessions which are difficult and expensive to do.”
A further key to the long life and minimal maintenance requirements is the material used: a corrosion resistant, high strength grade of stainless steel that negates the requirement for regular repainting. According to Bob Atherton, from the project’s steel manufacturer Outokumpu, the duplex grade used has double the strength of other more commonly used stainless steel grades and a design life of 120 years. Plus, unlike the carbon steel used in many bridges its corrosion resistance means that it won’t need recoating. “What you see today as a finished bridge is pretty much what it will look like in 120 years’ time,” he said. “And at the end of its life, you can pull it apart, recycle it and make another one … it’s 100 per cent recyclable.”
Ease of installation
The other major benefit of the AVA concept is the relative ease with which it can be installed, thanks to the fact that it is largely manufactured off-site. According to Jim Arnott, contract manager with consortium partner Walker Constrution whilst a traditional footbridge can take up to twelve months to install, the AVA bridge can be up and running in a fraction of that time.
Outlining the installation process, Arnott said that it will take around 15 weeks to break ground and put in foundations, and then just a matter of hours to crane the pre-assembled sections of bridge into position. Indeed, whilst the prototype bridge took 36 hours to put in place, Arnott’s team has already identified improvements that could get this down to as little as 27 hours for future projects. Once the bridge components are in place, final commissioning then takes a further two to three weeks.
Alongside the assemblies and components of the bridge, the other key element of the overall concept is - of course - the lift.
This has been developed by Sheffield firm ARX, a specialist in moving structures, which has previously worked on projects including the retractable pitch at Tottenham Hotspur’s ground, the retractable roofs at Wimbledon and the seating at Wembley stadium.
Interestingly, despite the firm’s pedigree, it hadn’t actually built a lift before, which according to Market Engagement manager Darren Falkingham enabled it to approach the technology with a fresh pair of eyes and deliver a number of key innovations that further reduce the maintenance requirements of the overall system.
For instance, whilst traditional lifts tend to have the machine gear installed at the top, all of the drive equipment for the AVA lift is installed at platform level, making access easier and safer for maintenance engineers. Meanwhile, the design of the drive system itself is claimed to be more reliable than existing systems: “We have a dual drive system,” said Falkingham, “so if one of those drives goes out of service for whatever reason the other drive picks up the slack and operates at a lower rating”.
Another common area of failure in traditional lifts addressed by the new design is the door mechanism. Whilst station lifts traditionally have flat doors that slide apart from the middle, the ARX team has devised a single piece, curved metal door that pivots around a single point which is claimed to be far more robust than existing systems.
Like the rest of the system, this lift is manufactured, assembled and tested offsite before being transported by road to site for installation and commissioning. According to Falkingham, whilst lift installation for these kind of projects has traditionally taken around 20 weeks, the initial prototype took just five hours to install.
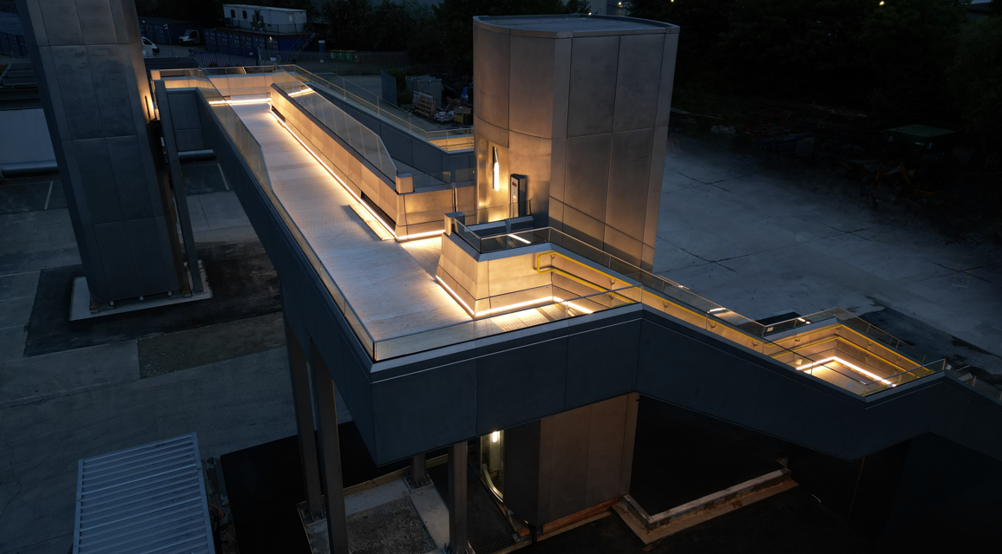
With the team now gearing up for the first full public deployment of the AVA bridge at Stowmarket station next summer, the consortium behind the project is hopeful that its numerous benefits will soon see it adopted across the UK’s rail network.
And while no firm decisions have yet been made on further installations, Anthony Dewar, Network Rail’s head of and architecture is clearly impressed by what he’s seen so far: “We know that there’s a demand and a demand make a step change in cost savings,” he said. “We need to look at guaranteeing volume and look at how we procure in batch. This project has helped us technically and also helped the industry focus on the potential for things like volume, procurement, production and automation.”
More from The Engineer
PMI falls as manufacturers feel the squeeze
17 months or two and a half years - which is it?