The bust and rescue of battery start-up Britishvolt made media headlines this winter. The story highlighted the fragility of the UK’s electric vehicle (EV) industry, whose future is uncertain if it must import costly batteries from abroad – especially from outside the European Union due to rules of origin in the UK’s Trade and Cooperation Agreement.
Batteries are just one part in an EV, albeit c. 40% of the value. They need motors, power electronics, chargers, inverters and more components that convert battery chemistry into motion. Where will these parts come from? Many UK-based suppliers are at different maturity stages. Some serve lateral, smaller automotive markets such as off-highway, and others are developing potentially game-changing technology.
A secure supply chain of active materials
The questionable provenance of some active materials in lithium batteries has dogged the battery industry. Typically the anode active material is graphite or silicon and the cathode is normally made of nickel or cobalt, that can be mined in poor conditions. Sigma Lithium is altering battery chemistry to secure a safe materials supply chain and extend battery range.
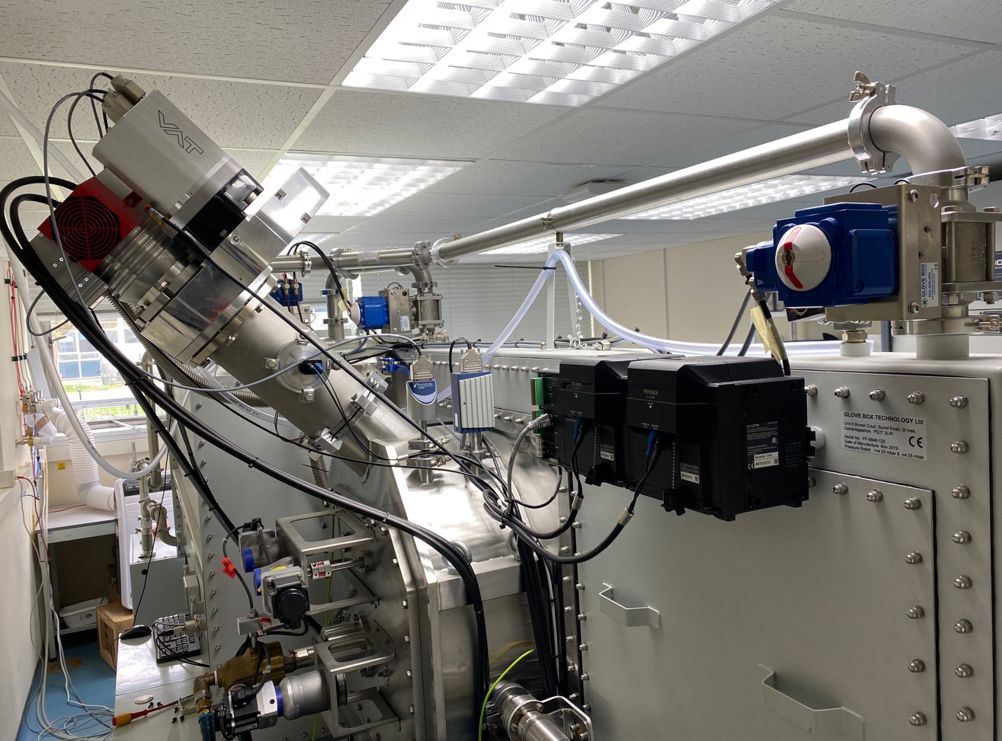
The pre-revenue company is developing a porous anode material made of three-dimensional metallic lithium. Using this as the anode material, mainly in solid-state batteries, can increase a car battery’s range by at least 50%, said CEO Gleb Ivanov. “We have developed composite metallic lithium as a safe anode active material in solid-state batteries, while the cathode will be based on manganese, rather than nickel or cobalt, or on other low-cost materials – maybe even sulphur, which is super-cheap. This will reduce the high-cost pressures of materials sourced from outside the UK, sometimes from unethical sources.” The safety of metallic lithium was holding back its adoption for rechargeable batteries but Sigma’s “3DLi” material has been approved safe for use.
EV battery, power electronics, and electric motors manufacturing need investment in innovation as well as partnerships with the broader global supply chain
Dr Hadi Moztarzadeh, Head of Technology Trends, Advanced Propulsion Centre
Metallic lithium could be sourced domestically from Cornish Lithium, but it is in ample supply in the rest of the world. The nature of this porous 3D lithium gives it two physical advantages that leading car manufacturers have acknowledged. “Being metallic means that we can deliver on mileage i.e. range and being porous three-dimensional means that we can deliver on fast-charging and discharging,” said Ivanov. “Our business model is licensing – we want 3D lithium inside every solid-state battery.” The other key material in the battery cell is a carbon mesh, supplied in high volume by a multinational UK company.
Is the technology compatible for use by the auto OEMs? “It is in the EV manufacturers’ interests to minimize nickel and cobalt content and switch to something superior – there should be ways for us and the OEM to make it work for any vehicle,” Ivanov said.
Mid-volume is natural step for firms that can differentiate
Arguably the biggest challenge for the UK EV industry is scale-up so these companies can supply the big carmakers. McLaren Applied manufactures a family of power electronics components, the control systems for electric drives – ECUs, accelerometers, sensors, inverters for fast charging and more. Volumes are in the mid-range, from several thousand to 50,000 units a year. This is where McLaren Applied and the UK should differentiate, Steve Lambert, Head of Electrification at McLaren Applied says, as firms cannot compete with global giants such as Bosch, Valeo and Continental on volume, and also there are several companies in this mid-range market, including Bentley, Lotus, Morgan and potentially some Jaguar Land Rover platforms and even the Nissan Z.
“Automotive tier ones producing in millions of units to car OEMs has been the established order, but with electric vehicles there is a big disruption in the market,” said Lambert. “There are lots of new entrants coming in, starting at lower volumes. OEMs are trying out new technologies on lower volume platforms with suppliers they have not used before, and some are open to taking these new technologies to mainstream platforms. What used to be called a “Valley of Death” going from niche supply into volume supply is a valley of opportunity, because there’s so much disruption.”
A key product made in higher volumes is inverters. These convert the battery DC current to AC and control the motor. As any manufacturing scales up, new global locations are assessed, but McLaren Applied wants to keep its inverter production in the UK. “Preparing for higher volumes, we now have a government-funded project looking at automating the inverter assembly, with the University of Newcastle, called SCIENZD,” said Lambert.
Get your motor running – efficiently
Motors provide the circular motion to turn the EVs’ axles. Tideturn Technologies’ mission is to make motors – used everywhere in buildings, heating and cooling, and transportation – much more efficient. Tideturn Transport recently bought two UK-based businesses in Gateshead and pledged to a multi-year, £100m investment in the region. In the short-to-medium term, its focus is on commercial vehicles and it is a good example of building manufacturing capacity close to market to mitigate global supply constraints.

“The demand for electrification solutions extends beyond passenger cars, with a growing need in off-highway and commercial transport areas such as construction, agriculture, rail and other industrial,” said Mark Cox, General Manager Transport for Turntide Technologies. “This shift means that a far broader range of enterprises, outside of just the large automotive OEMs, need access to locally manufactured electrification solutions, particularly given issues around geopolitics and complexity in shipping. This is a key reason we manufacture two-thirds of our product portfolio in the North East of England to meet our customer supply reliability and quality needs for electric powertrain solutions.”
Thermal management
Battery cells need full battery systems that are tailored to the vEV platform. Cosworth bought Delta Motorsport two years ago to develop an electrification business, and Delta Cosworth has since produced battery packs for many projects, most publicly for the 1,180bhp (yes) Ariel Hipercar and Envision’s two-seater electric race car.
It uses advanced, off-the-shelf battery cells at the core, that come in three main formats: pouch (like a vacuum-packed coffee bag), prismatic or cylindrical. These can have different kinds of chemistry depending on the requirements, for example, high power for faster charging, high energy for longer range or a combination of both. The company is involved in a £17.2 million project with Norton Motorcycles and partners, part-funded by the Advanced Propulsion Centre, called Project Zero Emission Norton to develop an e-motorbike with race performance and touring range.
One key, complementary activity is vehicle integration – taking a single vehicle or short production run fitted with an internal combustion engine and converting this to electric propulsion. If proven out, the platform volume can be scaled up and once a company is on the electrification path, they need battery systems. “With our Cylindrical Scalable Module (CSM), we have some novel ways of connecting cells together efficiently to offer the best performance for power applications, utilising an innovative method for thermally managing the cells,” said George Paterson, Product Development Director at Delta Cosworth. Another example, is its pouch module development used in British Touring Cars that has a novel cooling plate design allowing for improved thermal energy transfer from cells to coolant while minimising the distance between the cells, reducing the module size and reducing packaging restrictions.
With recent developments in hydrogen engines for industrial equipment, a battery system can provide power assist. “The hydrogen engine is likely to be coupled with a small high-performance battery that can accept regenerative loads and provide the equipment with the “peak power” when it needs extra energy for lifting, drilling or climbing in short bursts,” Paterson said.
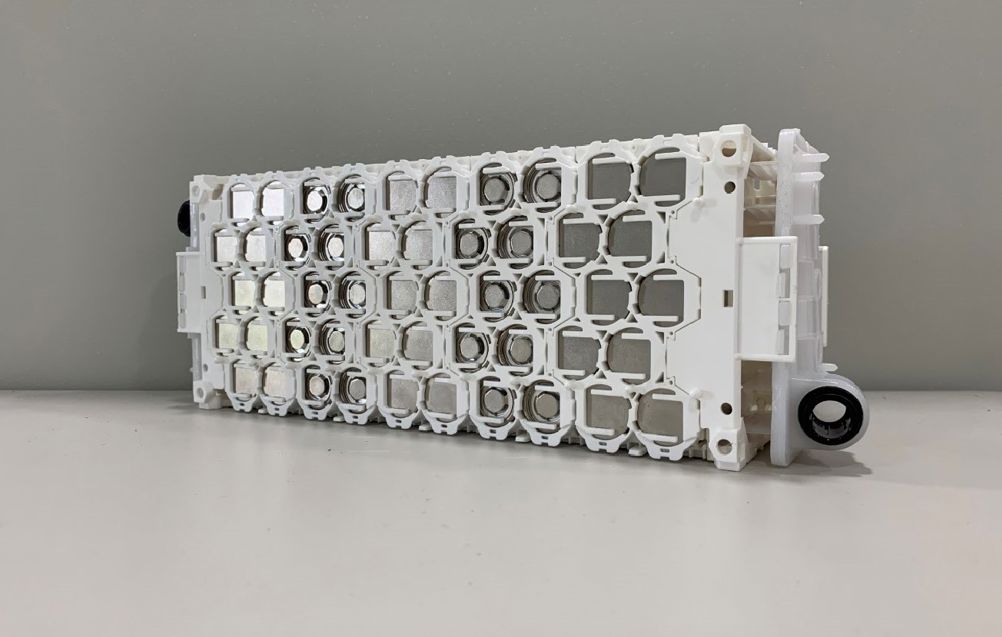
Securing supply of rare earths
Australia-based multinational, Ionic Rare Earths, recently acquired SerenTech, now rebranded as IonicTech, that has developed techniques to recycle permanent magnets using a process for the separation and recovery of rare earth elements from mining ore concentrates and waste magnets. This model is seen as important to secure access to rare earth elements, the supply of which is dominated by China. The Belfast company now has 11 full-time employees, with another 25 positions to be created in 2023 and further expansion planned.
Plenty of clever technology is being brought to market by some great companies. But the clock is ticking for mainstream automotive in Britain; the phase-out date for the sale of new petrol and diesel vehicles is 2030. A lot of cash and system transformation is needed across the whole of the UK supply chain to support the electrification of the automotive industry. Most would accept it is way behind where it needs to be to secure more British content at the high volume end, even though there many opportunities in high-performance markets and industrial markets.

“EV battery, power electronics, and electric motors manufacturing need investment in innovation and R&D, as well as partnerships with the broader global supply chain, mainly the upstream supply chain to secure critical minerals and raw materials, to ensure an end-to-end supply chain,” said Dr Hadi Moztarzadeh, Head of Technology Trends, Advanced Propulsion Centre. “This will make UK auto manufacturers more competitive and bring more investment to the UK.
He points to the APC’s value chain documents, showing where the UK needs more investment to address this. “To accelerate EV adoption, better access to reliable charging infrastructure, both publicly and at home, is needed,” he added. “Another major transformation would be developing a skilled workforce that is capable of designing, manufacturing, and maintaining EVs. We need a coherent and actionable framework between the auto sector, education, and training to translate requirements into skills and workforce development programmes.”
Guest blog: exploring opportunities for hydrogen combustion engines
"We wouldn't need to pillage the environment for the rare metals for batteries, magnets, or catalisers". Batteries don't use rare...