Meet the Experts
Alexander Lyskovsky - CEO, iFarm
Dave Scott - Founder & CTO, Intelligent Growth Solutions (IGS)
James Perry - Business Development Representative, LettUs Grow
What is your approach to vertical farming and what technologies are you employing?
AL: iFarm is an industrial-scale AgTech provider for growing plants vertically in controlled environments. Our proprietary hydroponic farming systems are pre-designed for indoor farming projects, ranging from 500 to 20,000m2, and can grow a variety of crops, including leafy greens, microgreens, strawberries, and vegetables, using NFT, NST, or Flood & Drain techniques. Modularity is the key principle of our farming technologies.
In addition to hardware solutions, iFarm provides iFarm Growtune software that streamlines farm processes such as microclimate control, system monitoring, scheduling and planning, CRM, API, and price management. We also offer agrotechnology: over 200+ plant growth recipes, with new formulas constantly being created, tested and released, to help our clients maximise their yields. iFarm offers one the most cost-effective vertical farming solutions with the lowest CAPEX. It’s important to note that iFarm does not own any farms and does not compete with its customers.
DS: IGS is a vertical farming infrastructure provider. Our customers buy the Growth Tower machines and an airlock from us. The towers come with access to our science backing and continual programme of research and development and crop science, ensuring the outputs of the towers gets better over time. This covers several different parameters, dependent on the customer’s priorities, including yield, elevated flavour, targeted nutrition, or increased shelf life. Our business model is relatively unique: we have made a covenant with the market never to grow crops for commercial sale. Instead, we focus on applying our engineering, crop science and data expertise to make the machine the best it can be, for the many use cases and problems the different regions of the world must solve.
JP: LettUs Grow design and build sustainable agricultural technology. We’re a team of growers, engineers, plant scientists, software developers and business experts, who all care deeply about food and the environment - and we’re also a B Corp. It’s important to say that we’re not targeting vertical farms but the whole Controlled Environment Agriculture (CEA) space - greenhouses, container farms, or anything in between! We specialise in ultrasonic aeroponics - an irrigation system that grows plants without soil. Aeroponics helps crops grow faster, healthier and with far less impact on the planet - it uses less water and zero pesticides. Aeroponics can be used in smaller or large-scale setups - where the impact can also change; you might have a greater social impact in a micro urban farm, but a huge environmental impact in a commercial scale greenhouse. We believe careful innovation in farming can make the world a better place and want to improve our food security and help mitigate climate change by actively working towards a future where affordable, healthy food can be grown and accessed locally.
How does your tech create and sustain the specific climatic conditions required to grow different crops?
AL: An iFarm indoor vertical farm uses a closed-loop air exchange system, with several components including cooling unit, CO2 enrichment unit, humidifier, and dehumidification unit. Lighting is provided via efficient LED lamps and is controlled by the light control unit. Depending on the crop and its growth phase, the lighting may vary. The nutrient solution is prepared in the mixing unit, and then transported to the roots of the plants through a tube system. The water used for the solution is treated with a reverse osmosis filter. iFarm farms have several watering areas, with a storage tank in each. This way we create an individual “menu” for each plant.
Through sensors installed in each area, the system monitors and adjusts the composition of the nutrient solution. The sensors also control the purity of the source water, acidity, light intensity, carbon dioxide levels, and humidity.
DS: Within the towers, each growth tray has its environment controlled by the tray above: the temperature, humidity and light are all delivered this way. CO2 efficiency is maximised by delivering this per tower, based on desired outcomes. For example, customers may put a crop into a tower with elevated CO2 levels for a particular growth stage, then return it to an ambient tower for another.
Having the tray above set the environment and light for the crop below allows future proofing. For example, not all trays need to have the same colour or type of LEDs, enabling a future scientific breakthrough (perhaps a certain colour does an incredible thing for a certain growth stage) to be introduced to a handful of trays. The tower can then automatically rotate trays to ensure that all crops are put under this new light at the correct growth stage to trigger the desired effect.
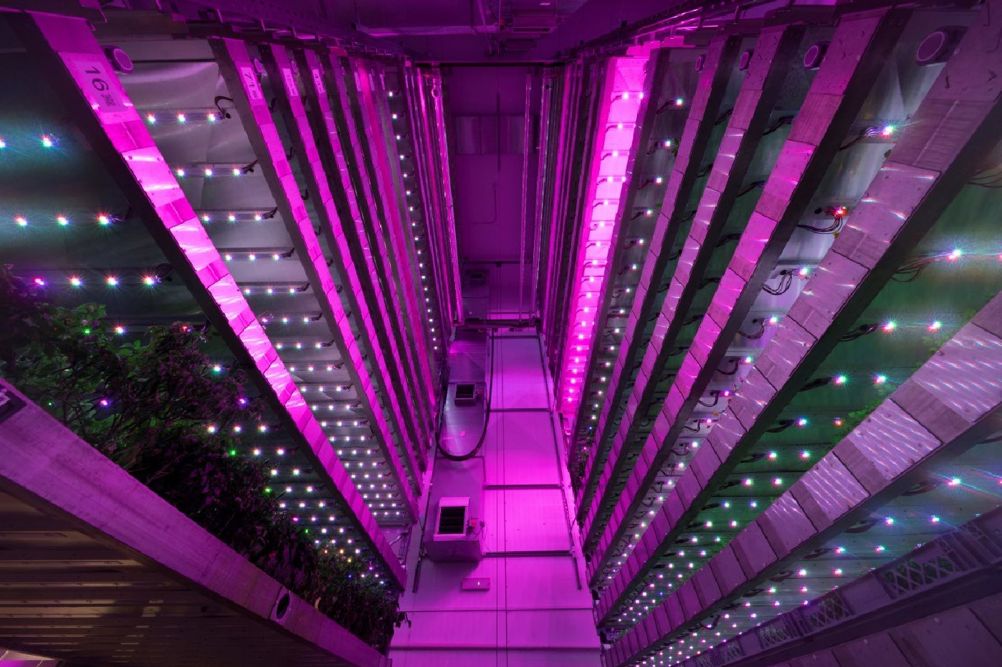
JP: Indoor farming is all about creating the optimal growing conditions for the plant. If we think about growing basil, it likes a warm climate where the days are long, and the plant is sheltered from wind or frost. You can recreate these conditions inside a vertical farm or greenhouse if you have a way of controlling the environmental conditions. At LettUs Grow, we’ve developed our own in-house software, Ostara, to do exactly that. Depending on the crop that you’re growing, different lighting, irrigation, fertigation and environmental conditions will be automated to maximise yield.
How close to price parity is vertical farming compared with traditional farming?
AL: It greatly depends on various factors, including each market, demand for ultra-fresh organically produced food, retail prices, and packaging. In general, we observe indoor vertical farming produce getting closer to outdoor-grown organic products in terms of price parity. However, of course, high quality pesticides-free indoor farming produce cannot compete with non-organic crops and vegetables grown outdoors. It’s important to note that organically grown foods are still mainly niche/premium market products. To become more mass-market, controlled-environment agriculture should keep working on breeding, and developing precise agriculture methods that would lead to an increased production efficiency.
DS: This depends on a number of different factors, however it can be very close indeed. Traditional farming methods employ expensive systems to fight against nature to provide crops with a more optimised environment. Extreme weather events are becoming increasingly more common, creating additional risk for growers. Technology like ours can reduce that risk, while additionally allowing the outcome to be tuned to increase the value of the final crop output, meaning the economics are competitive for many crops today and more in the future. It’s worth highlighting that in our view vertical farming isn’t a replacement for traditional agriculture, rather it is a complementary system.
JP: Vertical farming is never going to replace traditional farming, as it simply doesn’t make sense to grow some crops indoors - it costs money to power LED lights and we can harness the energy of the sun for free! So it then comes down to crop choice and location. Typically, you’ll find that the crops where you’re able to harvest the whole plant and the ones with quick growth cycles are the most likely to add up economically. Sometimes it might also make sense to use vertical farms for only a portion of the growing process - such as with propagation of fruits or tree whips. We do a lot of research and development in this area so we can explore the viability of novel crops.
How do you respond to critics that say vertical farming is too energy intensive?
AL: This is true. Indoor vertical farming faces a significant obstacle in the form of energy consumption necessary to operate climate systems and lighting (LED lamps, air conditioners and dehumidifiers account for 95 per cent of electricity usage). However, the technologies are advancing together with the growing share of renewable energy sources that will make indoor farming way more sustainable. iFarm Stackgrow proprietary farming system for automated indoor vertical farms allows a higher plant density, thus, significantly lower energy consumption compared to traditional racks construction. Incorporating highly precise farm management systems that enhance production quality and maximise productivity while significantly lowering energy consumption is yet another way to make farming operations more sustainable.
DS: IGS ensures the customer does not waste energy and that the system has enough flexibility to guarantee that 100 per cent of what is grown is consumed by the end user. This applies beyond full seed to harvest crops too. For example, by growing strong, high-quality, pest and disease-free crops in a vertical farm before planting out in a more traditional growing environment, farmers significantly increase their chances of success . Also, the tower machines have been designed to be the perfect consumer of three-phase power and to deliver power usage flexibility to an extent never seen before in an industrial process.
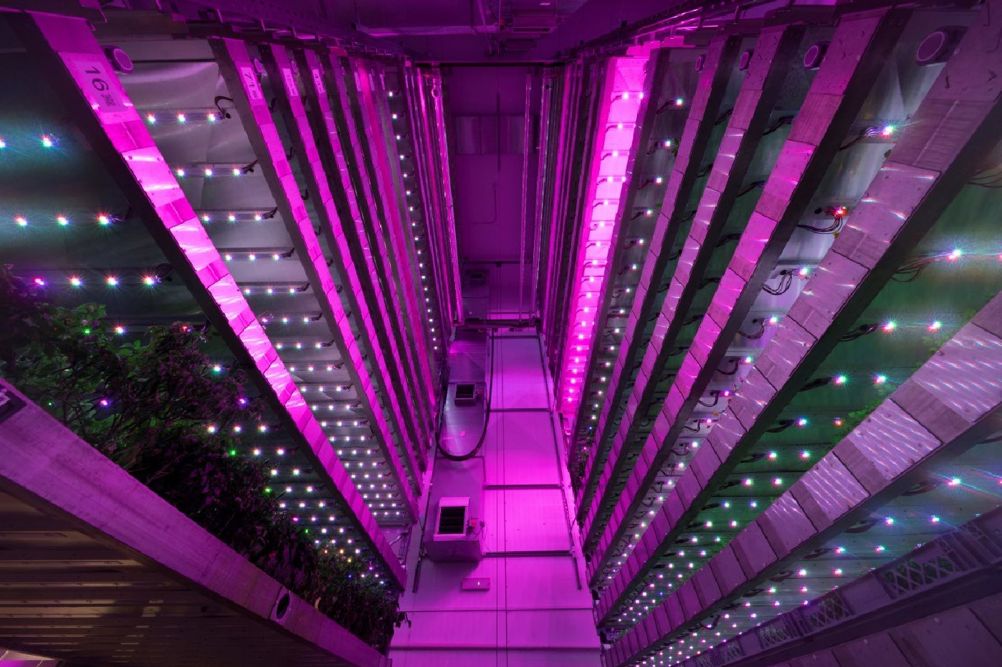
JP: Well, it is a valid criticism. Whilst vertical farming is an efficient use of some resources such as water, it’s less efficient for energy. It’s important not to shy away from the fact it’s energy intensive but to focus on how to get that energy affordably and sustainably. We encourage anyone who’s interested in starting a vertical farming business to consider energy as a top priority as it will be one of the largest operating costs of your business. You can of course get green energy off the grid, but you’re then subject to price volatility. In an ideal world, you’d be co-locating a vertical farm next to a renewable power source. This is what we’ve seen the largest vertical farm in the UK do by locating their farm next to solar panels.
Emergency law passed to protect UK steelmaking
<b>(:-))</b> Gareth Stace as director general of trade body UK Steel, is obviously an expert on blast furnace technology & operation. Gareth...