It’s an unfortunate irony that the race to adopt greener technology could lead to millions of perfectly serviceable vehicles being scrapped before their time.
While electric powertrains have been proven to deliver lower lifecycle emissions, there’s no getting away from the fact that manufacturing a whole new vehicle and disposing of the old one does carry a hefty environmental penalty – especially when that vehicle is a 12-tonne bus.
Equipmake may have the solution. It’s one of a number of UK companies now offering a ‘repowering’ service, where diesel trucks and buses can be re-fitted with an electric powertrain and given a whole new lease of life.
The Norwich-based firm designs and manufactures the majority of the parts for the conversions in-house, including its own motors and battery packs. It’s also in the process of developing its own silicon carbide inverters, which will soon replace the proprietary items used currently.
“Being able to build our own batteries is quite important,” notes Equipmake founder and managing director, Ian Foley. “We do have a standard battery pack, but quite often we find we need to adapt that to a particular vehicle.”
Dealing with an existing vehicle can present some packaging challenges, but the layout of a bus typically lends itself quite well to electrification, Foley explains. The electric motor is mounted right at the back and drives forwards onto a short propshaft, occupying part of the space where the engine and gearbox would normally be. This also provides space for the batteries, although larger vehicles like double-deckers typically require an additional set of batteries mounted further forwards where the fuel tanks would normally sit to even out the axle loads.
Heavy metal
In total, the additional hardware weighs approximately 2.5 tonnes, which sounds like a lot, but more than a tonne of engine, gearbox and fuel system is removed at the same time, leading to a net increase of around a tonne (on a vehicle that may have a gross weight of 19.5 tonnes).
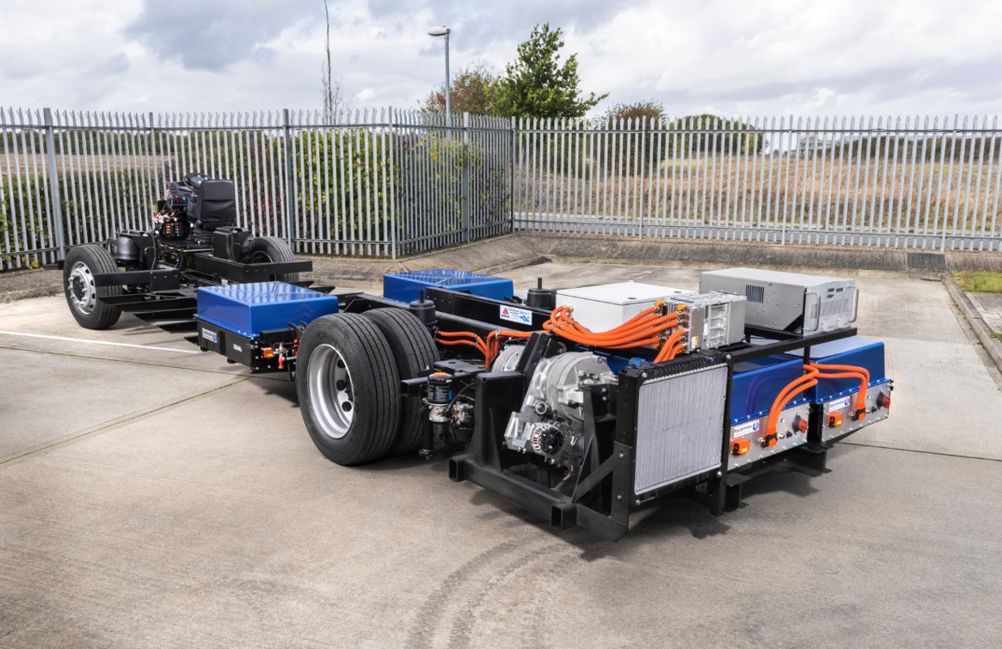
Equipmake manufactures a variety of motors for applications ranging from light aircraft to giant mining trucks. The standard bus offering is an internal permanent magnet (IPM) design with V-shaped magnets on a laminated ring. The electromagnetic design of this motor generates a significant amount of reluctance torque in addition to the standard torque from the permanent magnets. This results in a very high torque density at the cost of a somewhat reduced power density compared to some of the other designs in the company’s portfolio.
“Torque is everything with a bus,” comments Foley. “The average power of a city bus cycle is only about 30 kW with a peak of 200 kW – less than you might find in a large family saloon car. But the torque requirement is huge, because you’re continually stopping and starting something that weighs the best part of 20 tonnes.”
The motor was designed from the outset with this drive cycle in mind, he points out. Rather than chasing bragging rights on peak efficiency figures, the intention was to design something that would offer the greatest combined efficiency over the complete drive cycle.
“Our motor designer used optimisation software to tune the motor design to maximise its efficiency over that cycle,” explains Foley. “There’s a range of things we can play with, including the size and shape of the magnets, and the material properties. For instance, if you put less steel and more copper in, you’re going to have lower I2R losses, but that might affect high speed performance, so there are a lot of incremental trade-offs. It’s hard to say, but overall they probably add up to a difference of more than 10 per cent over the complete cycle.”
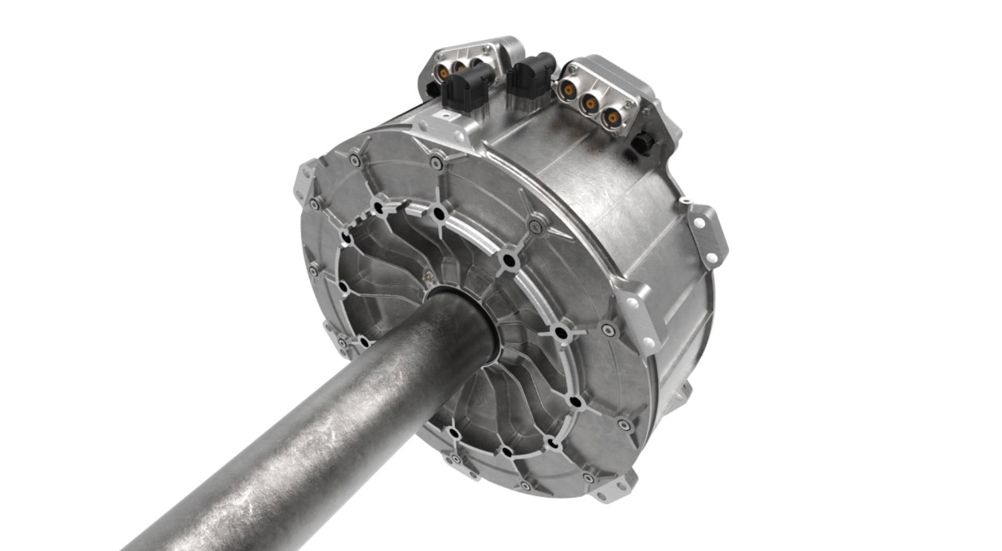
How exactly that translates to range depends on the type of bus and the exact drive cycle. Generally, we’re told, it’s possible to accommodate a total battery capacity of around 400 kWh (roughly four times the size of a large passenger car battery). This typically equates to a usable range of around 150 miles.
“Most city buses cover a maximum of 150 miles a day,” says Foley. “There are operations that can go up to a couple of hundred miles. Most bus operators would say that their dream scenario is 250 miles of range, which would allow it to be used on any route in any conditions, but nobody is there [with an electric powertrain] yet. On the other hand, 150 miles of continuous operation is realistic, and that works for a large part of the city bus market.”
Heating up
Predicting the usable range of a bus can be tricky. For a start, there’s the individual drive cycle. A city centre route with a lot of stop-start traffic, as you might encounter in the middle of London, can allow the bus to recover up 60 per cent of the kinetic energy that would otherwise be lost in braking. On a more typical suburban route that figure might fall to 30 per cent.
Lithium ion cells work best within a relatively narrow temperature band, so the ambient conditions can have a direct impact on the battery efficiency. But the indirect effect of cold weather can be even greater, with the battery also responsible for providing heating, ventilation and cooling (HVAC).
“HVAC is extremely important,” comments Foley. “There’s a debate about what’s a sensible heating requirement for a bus on a very cold day. If it’s minus 10 outside, the chances are everyone is getting on with thick winter clothing anyway. And each of those people is a 100-watt heater, so you might not want any heating at all if the bus is full. Conversely, if the bus is relatively empty on a cold day it can take as much energy to heat it as it does to drive it along. If that’s 20 kW over the course of 10 hours you could use 200 kWh – half the battery capacity – just for heating.”
Equipmake engineers its own HVAC systems for the conversions, based around the same sort of heat pump technology that’s now found in a lot of passenger EVs. The company also uses its own powertrain control system, which takes signals for things like the pedal inputs and the dashboard display off the vehicle’s CAN network. This ECU also interfaces with the existing body control unit, which handles functions like the lights and the doors.
Depending on the specification, the finished powertrains (including the battery) are warrantied for between 350,000 and 500,000 km. Equipmake claims that the cost of repowering a bus can typically be reclaimed over the course of five to seven years. That means a bus that’s converted halfway through its normal life should theoretically pay for itself.
The biggest argument in favour of electrifying city buses, however, remains air quality. While burning hydrogen or synthetic diesel in a combustion engine could theoretically deliver similar net CO2 savings, these technologies still face major challenges around NOx emissions (not to mention cost).
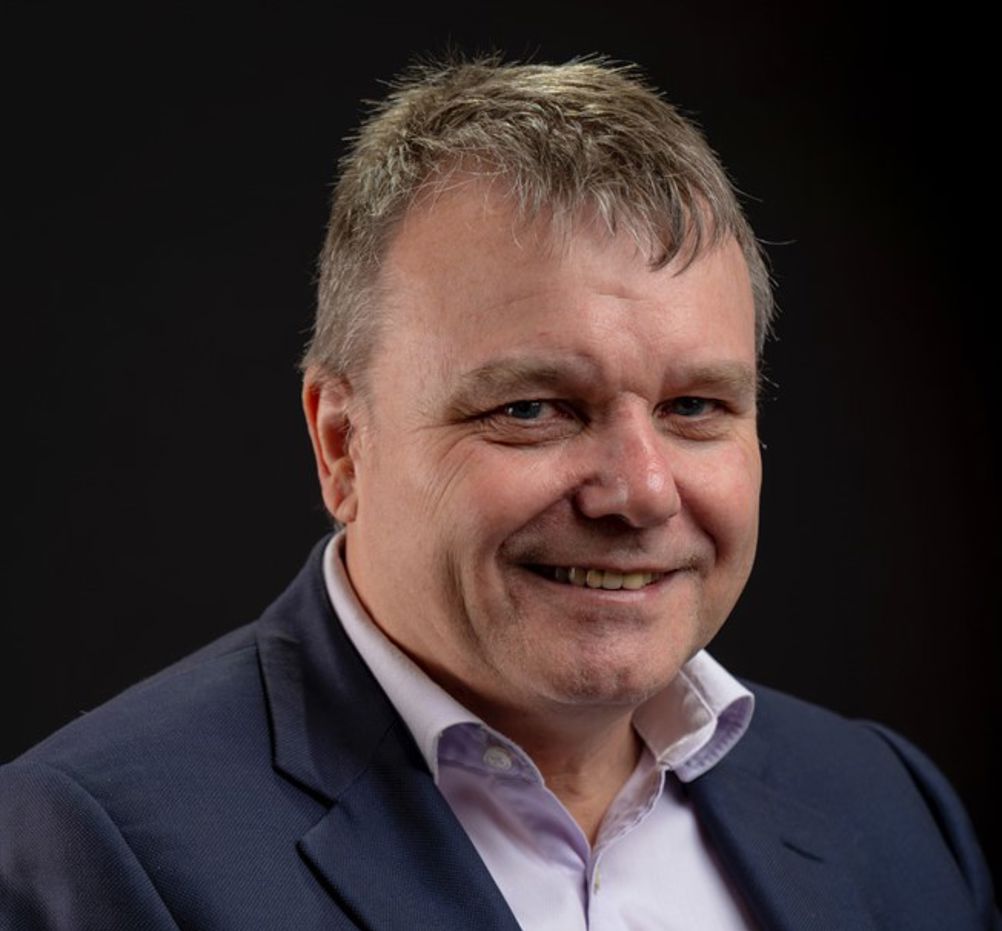
Another option would be electric propulsion with hydrogen fuel cells. Equipmake is currently participating in a government-funded project to develop a fuel cell-powered bus, but the technology isn’t without its challenges.
“We’re technology agnostic – if someone came to us and wanted their buses re-powered with fuel cells, we would do it – but the main issue at the moment is cost,” comments Foley. “With hydrogen, you could get that magic 250-mile range, so I suspect a lot of operators would go down that route if it was cost-competitive with battery electric just to provide the extra flexibility. But the reality is that most operators don’t actually need it, and the cost of both the components and the hydrogen itself is likely to be prohibitive at the moment.”
It seems unlikely that repowering could ever work on a large scale for passenger cars. There, the cost of second hand EVs is rapidly coming down, and most private buyers would rather spend the money on a newer model than refurbishing an old one. But for trucks and buses where the powertrain integration is less complex and the operational life spans hundreds of thousands of miles, it might just be the ideal solution.
McMurtry Spéirling defies gravity using fan downforce
Ground effect fans were banned from competitive motorsport from the end of the 1978 season following the introduction of Gordon Murray's Brabham...